Fire-resistant insulation materials are a type of material with high fire resistance and good thermal insulation properties. It is widely used in metallurgy, chemical industry, petroleum, machinery manufacturing, silicate, power, and other industrial fields. Especially in the metallurgical industry, the largest amount is used, accounting for 50% to 60% of the total output. This type of material not only has the characteristics of high refractoriness and good stability. It also has good thermal insulation properties, which can effectively reduce energy loss and improve the energy efficiency of industrial equipment.
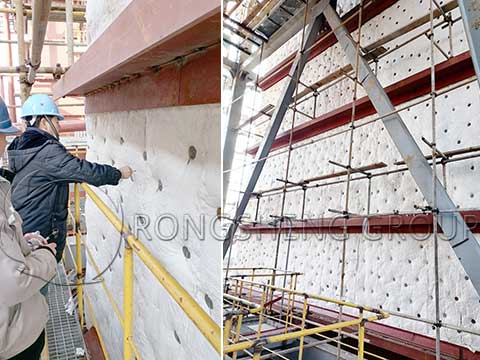
Types of Refractory Insulation Materials
There are many types of refractory insulation materials, including but not limited to those listed below.
- Class A fireproof insulation material. It is a material with fire protection grade A and has excellent fire resistance. Mainly divided into A1 level and A2 level. Class A1 materials are single inorganic non-combustible materials, while Class A2 materials are composite organic non-combustible materials.
- Fireproof insulation board. Usually made of inorganic materials (such as cement), reaching A1 level fire protection standards. It has good fire resistance and stability and can last as long as the building.
- Special refractory materials. Including acidic, alkaline, aluminum silicate, and other types. It has high melting point, high fire resistance, and excellent performance in high-temperature environments.
- Glass wool insulation materials and mineral (rock) wool insulation materials. It is an inorganic fiber heat-insulating and sound-absorbing material with good heat-insulating properties and certain compressive strength.
- Calcium silicate thermal insulation materials and composite silicate thermal insulation materials. A closed-cell network structure material connected by a solid matrix, which has good thermal insulation properties and high mechanical strength.
The application of these materials not only improves the safety of industrial production but also promotes energy efficiency. It is an essential basic material to ensure the production operation and technological development of the above-mentioned industries.

Thermal Insulation Principle of Thermal Insulation Refractory Materials
Insulating refractory materials refer to refractory materials with low thermal conductivity and low heat capacity, also known as insulation refractory materials. The basic principle of thermal insulation is to reduce the thermal conductivity. Since the thermal insulation material contains a large number of pores, the heat transfer through the thermal insulation material is the heat transfer between the solid phase and the gas phase. Solid-phase heat transfer is mainly conduction, and heat transfer through the gas phase is more complicated than heat transfer through the solid phase.
When heat is transferred from the high-temperature area to the interior of the insulation material, the heat transfer process is carried out in the solid phase before it encounters the pores, that is, through the conduction of the solid phase. After encountering the pores, the possible heat transfer routes become two: one is heat transfer still through the solid phase. Due to the change in conduction direction, the route of heat conduction is greatly increased, which means that the thermal resistance increases. Another route is heat transfer through the pores. Heat transfer through pores includes conduction, convective heat transfer and radiation heat transfer through the gas. It can be seen that the heat transfer process of insulating refractory materials includes two heat transfer channels. That is, through heat transfer in the solid phase and through heat transfer in the gas phase.
The thermal insulation effect of insulating refractory materials is due to the presence of a large number of pores, and the gas in the pores has good thermal insulation properties. Heat transfer through pores mainly includes the following aspects.
- Heat conduction. The thermal conductivity of the gas is very small, and the gas in the pores of most insulating refractory materials is air. The thermal conductivity of air is much smaller than that of solid materials, so the conductive heat transfer through the pores is very small.
- Convective heat transfer. Since the pores in most insulating refractory materials are very small, the flow of gas in the pores is restricted and the speed is very small. Therefore, the convective heat transfer of the gas in the pores is not large. The smaller the pore diameter, the poorer the fluidity of the gas in the pores, and the smaller the convective heat transfer. When the pore diameter is smaller than the free path of molecular motion of the gas in the pores, the molecules in the pores stop moving and there is no longer convective heat transfer through the pores.
- Radiation heat transfer. Because the gas in most insulating refractory materials is air, that is, oxygen and nitrogen. Their molecular structures are all symmetrical diatomic, and these gases have very little ability to absorb and emit radiant energy. Therefore, the radiation heat transfer through the pores is mainly the radiation from the high-temperature wall of the pores to the low-temperature wall. But overall, the radiation heat transfer through the pores is not large.
From the above analysis, it can be seen that the heat transfer through the pores in insulating refractory materials is very small, and most of the heat is transferred through the solid phase. Heat transfer through the solid phase accounts for a large proportion of all heat transfer mechanisms. It should be pointed out that the high proportion of solid phase heat transfer does not mean that the insulation effect of the insulation material is poor. It is precisely the good gas phase heat insulation effect that leads to a high proportion of solid phase heat transfer.
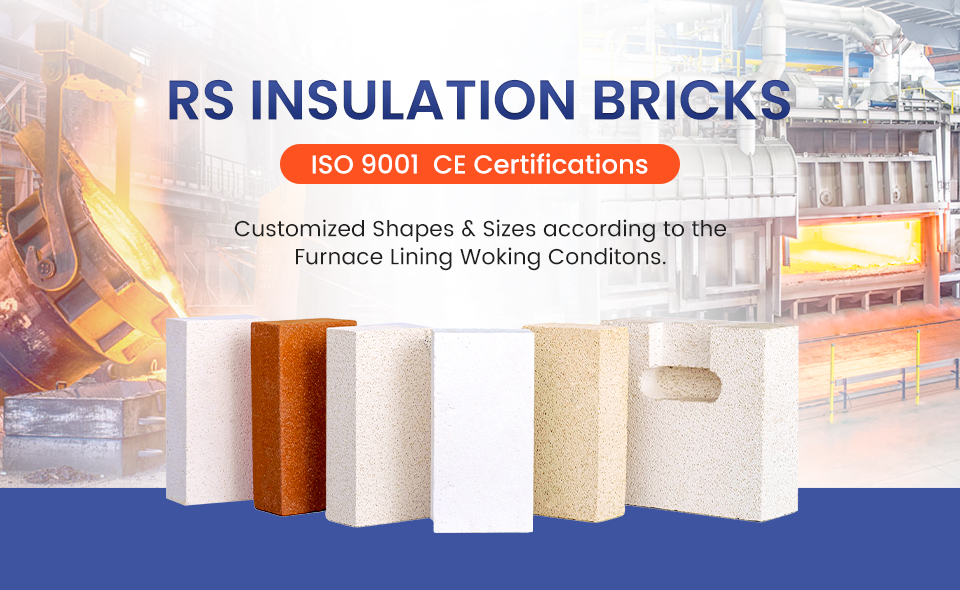
How Many Years Is the Service Life of Kiln Insulation Materials?
The service life of kiln insulation materials is usually about 3-5 years.
-
Types of kiln insulation materials
Kiln insulation materials mainly include aluminum silicate fiber, alumina fiber, high alumina ceramics, microcrystalline glass, calcium silicate board, insulating firebricks, etc. They all have good thermal insulation properties and high-temperature resistance. Among them, aluminum silicate fiber and alumina fiber are the most widely used materials. Because of its light texture and low thermal conductivity, it can meet the insulation requirements of most kilns.
-
Service life of kiln insulation materials
The service life of kiln insulation materials is mainly affected by the following factors, such as the temperature of the inner wall of the kiln, the frequency of kiln temperature changes, the way the kiln is operated, the quality of the materials, etc. Generally speaking, the service life of kiln insulation materials is about 3-5 years. If handled improperly or the temperature of the inner wall of the kiln is too high, the service life of the material will be shortened. And with good maintenance, its service life will also be extended.
-
Maintenance and replacement of kiln insulation materials
In order to extend the service life of kiln insulation materials, we can take the following measures.
- Frequently check the status of the kiln insulation materials, and promptly detect and deal with damage or aging.
- Control the temperature of the inner wall of the kiln to avoid damage to the insulation material due to excessive temperature.
- Avoid sudden cooling and heating when operating the kiln to reduce the frequency of temperature changes.
- Carefully select and use kiln insulation materials to avoid degradation in insulation performance due to material quality problems.
When the kiln insulation material is aged, damaged, or has other problems, we need to replace the material in time. To replace the insulation material, you need to clean the inner wall of the kiln first, peel off the aged and damaged insulation material, and remove the residue. Subsequently, appropriate insulation materials can be selected and replaced based on the actual conditions of the kiln. Rongsheng refractory material manufacturer provides refractory material services for high-temperature kilns. Customized insulation material solutions. Free quote.