Insulating Bricks Kiln Linings, also known as lightweight refractory brick. Its most notable features are small volume density, low thermal conductivity and compressive strength, and high apparent porosity. It can effectively prevent the heat flow from passing through the enclosure structure and reduce the heat loss of kilns and other high-temperature equipment. Insulating fire bricks are generally used as linings or insulation layers of industrial kilns. Saving energy can effectively improve production efficiency.
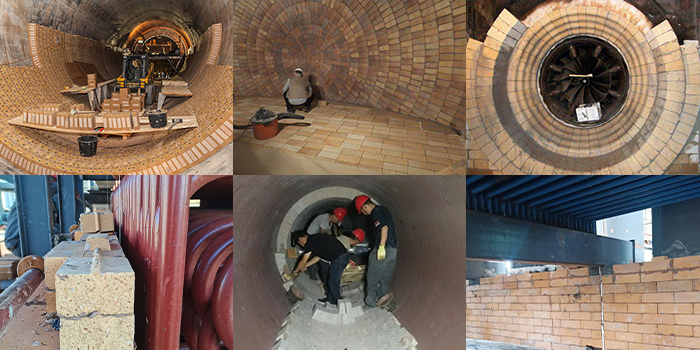
Briefly of Refractory Materials for Kiln Linings
Insulating fire brick, Insulating Fire Bricks(IFB) Used for Kiln Linings, are of different materials. When used for kiln linings, can increase the heat storage function of industrial kilns and reduce the loss of energy. Read More for Refractory Bricks, insulating bricks, insulating fire bricks, and Kiln Linings.
What is the Difference between Insulating Fire Brick and Refractory Bricks? From the definition, refractory materials are generally divided into two types, unshaped refractory materials, and shaped refractory materials. Shaped refractories generally refer to refractory bricks, including Insulating Bricks.
Performance of Insulation Refractory
Refractory fiber is a highly efficient heat preservation and heat insulation refractory material has both the general fiber soft, characteristics of high strength, and can be processed into various products. such as blanket, cords, belts, carpets, etc., and has the performance of ordinary fibers, such as oxidation resistance, corrosion resistance, high-temperature resistance, etc. To make up for general refractory materials too brittle faults. And refractory fiber volume density is small, usually, 0.1~0.2g/cm3, is ordinary clay brick 1/20~1/10, light clay brick 1/10~1/5.
Therefore, the use of refractory fiber instead of firebrick, can reduce the weight of the furnace body, and reduce the thickness of the furnace wall. In addition, refractory fiber-specific heat is low, only ordinary firebrick 1/72, and light clay brick 1/42. Therefore, it is often used as intermittent kiln lining, which can significantly reduce heat storage loss, save fuel, and increase the heating rate. Refractory fiber products have been widely used in industrial kilns and have achieved obvious energy-saving effects. For continuous operating furnaces, the use of refractory fiber products can save energy of 3%~10%, for intermittent operating thermal equipment, the use of fiber refractory material energy saving is more obvious, energy saving up to 10%~30%, or even higher. The masonry method of refractory fiber products has a great influence on its thermal insulation effect. The adiabatic board is a kind of not to burn product, by fireproof fiber material, fireproof raw material, union agent, and admixture composition, and is an important variety of heat preservation and heat insulation refractory material. According to the material, the insulation plate is divided into silica, magnesium, magnesium olivine, aluminum silicate, and floating beads.
This refractory material is characterized by low thermal conductivity, low density, and good corrosion resistance. It is mainly used in ingot cap and continuous casting tundish, so it is called tundish adiabatic plate and cast mold adiabatic plate respectively. The insulation plate of Tundish is divided into a wall plate, bottom plate, and impact plate. Insulation refractory materials should be selected reasonably according to the purpose and requirements of energy saving, structural characteristics, working conditions, and service life of the furnace. where to buy fire bricks? We are a professional refractory material manufacturer, refractory products of all kinds, stable and reliable quality, you are welcome to consult and purchase. Rongsheng Refractory Company.
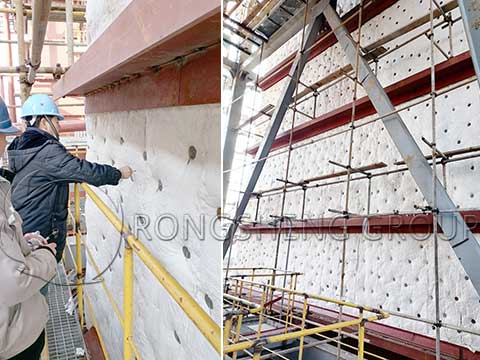
What is the Difference between Insulating Fire Brick and Refractory Bricks?
From the definition, refractory materials are generally divided into two types, unshaped refractory materials, and shaped refractory materials. Shaped refractories generally refer to refractory bricks. This means that the insulating fire brick is a kind of refractory brick. However, there are still some differences between insulating fire bricks and refractory bricks. where to buy insulating fire brick? Rongsheng High Alumina Insulating Fire Brick, Get a Free Quote Now! Refractory bricks have high mechanical strength and long service life. And good chemical stability, no chemical reaction with the material, and good high-temperature resistance, higher heat resistance temperature can reach 1900 ℃. It is especially suitable for the lining of smelting furnaces and can withstand high temperatures of 1580℃-1770℃. Of course, there are many other thermal furnaces’ refractory linings that also require refractory bricks for masonry. Refractory brick has the advantages of high density and high strength; good wear resistance and corrosion resistance; small thermal expansion coefficient.
Due to the characteristics of the refractory brick itself, the main components of the refractory bricks determine the quality and characteristics. Generally, the most prominent advantages of refractory brick products with different raw materials are also different. Where to purchase fire bricks for kiln linings? Refractory Bricks from Rongsheng Manufacturer, Get a Free Quote for Insulating Fire Brick. Insulating fire brick, also known as lightweight refractory brick. Its most notable features are small volume density, low thermal conductivity and compressive strength, and high apparent porosity. It can effectively prevent the heat flow from passing through the enclosure structure and reduce the heat loss of kilns and other high-temperature equipment. Insulating fire bricks are generally used as linings or insulation layers of industrial kilns.
Saving energy can effectively improve production efficiency. However, due to the large apparent porosity of the refractory products, loose structure, low strength, poor resistance to various types of erosion, and wear resistance, it can only be used more in the heat insulation layer of kilns and other high-temperature thermal equipment. Generally, it is not suitable for work lining and heavy load-bearing parts. RS Mullite Insulating Fire Bricks. Differences between insulating fire bricks and refractory bricks. Refractory bricks and insulating fire bricks are very different. Their working environment, applications, and the role played in the refractory lining are all different. Density. Insulating fire bricks are used as insulation materials, and their general density is around 0.8-1.0 g/cm3. However, as a refractory material, refractory bricks have higher density requirements. The density of refractory bricks is basically above 2.0g/cm3. Because of the greater density of refractory bricks, the better the compactness and the higher the strength.
Refractoriness. The performance of thermal insulation bricks is mainly in thermal insulation. Although it has certain fire resistance, it is still not as good as fire brick in fire resistance. The fire resistance of insulating fire brick is generally below 1400 degrees. But refractory bricks are different. As a refractory material, refractory bricks have refractoriness above 1400℃. Therefore, its fire resistance can achieve flame retardant or even non-combustible effect. Insulation performance. The thermal conductivity of light insulation bricks is generally 0.2-0.4 w/m.k, (average temperature 350±25℃). The thermal conductivity of refractory brick is above 1.0 w/m.k, (average temperature 350±25℃). It can be concluded that the thermal insulation performance of thermal-insulating fire bricks is much better than that of refractory bricks. Rongsheng Manufacturer with Kinds of Refractory Bricks. Any furnace is not built with only one kind of refractory bricks, it needs a variety of different types of refractory bricks to be used together. Insulation bricks and refractory bricks have their advantages in performance. Therefore, when choosing, it must be based on the working conditions of thermal equipment.
Of course, if your thermal furnace needs other types of refractory materials, Such as high alumina bricks, silica insulation bricks, magnesia bricks, chrome bricks, etc. Rongsheng Refractory Bricks Manufacturer will also provide you with suitable recommendations! Related refractory materials for kiln linings, Anti-Stripping High Alumina Bricks are High Alumina. 0.8 Lightweight Fire Brick High Alumina Lightweight. Refractory Bricks for Lining of Aluminum Smelting. Refractory Materials for Incinerators Linings. Magnesia Bricks with Refractoriness Above 2000℃, High Temperature and Corrosion Resistant Burner Bricks. Cement Kiln Lining Refractory Bricks for Sale, Direct Bonded Magnesia Chrome Brick, etc.
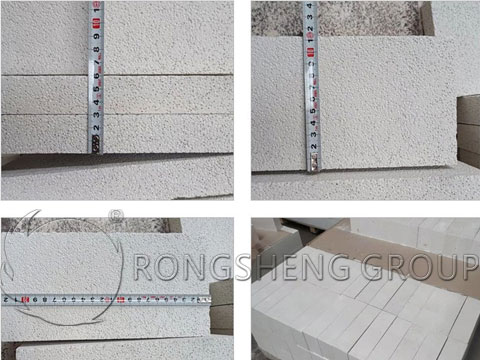
Rongsheng Mullite Insulation Bricks For Sale
Mullite insulation bricks are a new type of refractory material in China, which can directly contact flame and has the characteristics of high-temperature resistance, slightly high thermal conductivity, small energy-saving effect, and so on. Mullite insulation brick is a high alumina refractory with mullite as the main crystal phase. Introduction To Mullite Insulation Brick. High refractoriness, up to more than 1790℃. The starting temperature of load softening is 1600 ~ 1700℃. The compressive strength is 70 ~ 260MPa at normal temperature. Good thermal shock resistance. There are two kinds of sintered mullite brick and electrofused mullite brick. Sintered mullite brick with high bauxite clinker as the main raw material, adding a small amount of clay or raw bauxite as a binder, through molding, fired, and made.Mullite Insulation Bricks Application. Used for lining cracking furnaces, hot air furnaces, ceramic roller kilns, electric porcelain drawer kilns, glass crucibles,s, and various electric furnaces.
Glass Melting Kiln Superstructure Brick
Glass melting kiln superstructure brick, material passage brick, cover plate, metallurgy is very other industry medium temperature kiln furnace lining, carbon black reaction furnace quench section, stay section lining. The lining of an upper crown, crown brick, and other industrial heating equipment of glass melting kiln. Glass furnace superstructure brick, cover plate, molding parts, medium temperature carbon black reactor, and other thermal equipment lining. Mullite and corundum saggers for high temperature. Glass furnace superstructure brick, material path brick, cover plate, molding parts, medium temperature carbon black reaction furnace lining, and other thermal equipment lining. Corundum and mullite saggers for high temperature. The lightweight mullite brick is made of imported plate-shaped corundum and high-purity fused corundum with the application of advanced ultrafine powder-adding technology. It is mixed, dried shaped, and fired in a shuttle kiln at high temperature. Mullite light brick is widely used in residue gasifiers, second-stage reformers of synthetic ammonia, carbon black reactors, and refractory furnaces. The size of the products, physical and chemical indicators, and service life are up to customer requirements.