The RH device is mainly used for the dehydrogenation of molten steel and later added vacuum decarburization and vacuum deoxidation. Improve the purity and alloying of molten steel. The RH method has the advantages of a short processing cycle, large production capacity, and good refining effect. Ideal for use with large steelmaking furnaces. Magnesium chromium and magnesium zirconium are mainly used for refractory bricks of RH refining equipment.
Application of Magnesia Refractory Brick in RH Refining Equipment
The working environment of the RH refining furnaces lined with refractory materials is a vacuum and high temperature. The thin container of the RH furnace can be divided into upper, middle, and lower parts which can be replaced and partly immersed in molten steel. The service life of the refractory depends on the installed parts, the lower the service life, the shorter the service life of the elevator tube. According to the corrosion factors of the working lining of the RH furnace, the refractory lining of the RH refining furnace is usually lined with magnesia-chrome bricks or alkaline ramming materials. Or use the comprehensive lining of partition lining according to the use conditions of different parts.
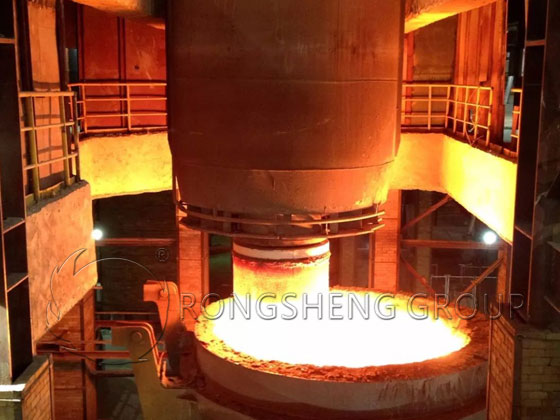
Refractory materials The refractory materials used in the lining of RH devices are generally less damaged because they do not directly contact molten steel and slag. The intermediate tank damages the refractory lining due to contact with molten steel and slag or spalling at high temperatures. The lower tank, including the refractory lining of the dip tube, is a high corrosion area of the unit and often determines its service life. In the lining of the lower tank, due to the infiltration of slag into the brick to form a metamorphic layer, the metamorphic layer cracks parallel to the non-modified layer, resulting in spalling and advanced damage. At the same time, due to the infiltrated slag, the particle combination of the lining material is cut off, so the particles become easily lost. Therefore, this part should be selected with less tissue deterioration. It is difficult for the slag to penetrate, and even if it penetrates, it can maintain the combination of particles and a refractory with high spalling resistance.
The upper part of the RH vacuum chamber
When the upper part of the RH vacuum chamber is evacuated, the oxygen pressure is lower. When the air is stopped, the oxygen pressure is higher, which changes the price of iron oxide in the magnesia-chrome brick and produces a volume effect. Ordinary magnesia-chrome bricks are usually built on the upper part of the vacuum chamber, and obviously, ordinary aluminum-magnesium spinel bricks can also be used. However, magnesia carbon bricks should not be used, because, under vacuum conditions, it will promote the self-consumption reaction of magnesia carbon bricks.
Vacuum Chamber Lower, Bottom, and Throat
In terms of corrosion resistance, corrosion resistance, and permeability of iron silicate slag and desulfurization slag, the better refractory material is a high Cr2o3 content directly combined with magnesia-chrome bricks. Among them, are the fused magnesia-chrome brick or the high Cr2o3 content in the matrix. Magnesia-chrome bricks with fine pores are more suitable. Therefore, in the lower part of the RH furnace vacuum chamber. High-quality direct-bonded magnesia-chrome bricks fired at high temperatures should be built at the bottom and throat.
Refractories for Dip Tube Lining
At present, the lining of the dipping pipe is mainly made of magnesia-chrome bricks with good heat resistance and shock resistance. One of the effective ways to improve the heat resistance and shock resistance of magnesia-chrome bricks is to reduce the content of iron oxide and increase the content of Al2O3. The content of iron oxide in magnesia chrome brick is high. When a redox change occurs in the atmosphere, such as when contacting molten steel at high temperatures, the hot surface iron oxide exists in the magnesium fuidite (Mgo·Feo)O according to the Fe-O state diagram. When in contact with air when stopped, it will be converted into high-valent iron oxide. This change between magnesium ferrite Mgo·Fe2o3 and magnesium fuustenite will cause the cracking of magnesia-chrome bricks. Increasing the Al2o3 content of magnesia-chrome bricks can also increase the degree of direct combination of magnesia-chrome bricks, thereby increasing the strength of the bricks.
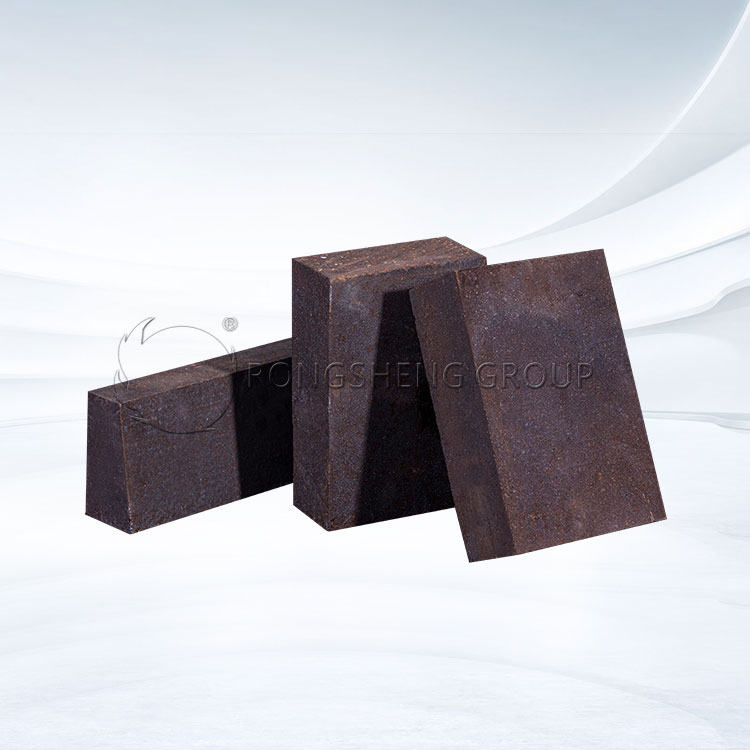
Application of Magnesia Chrome Refractory Brick in RH Refining Equipment
Magnesia-chrome refractory bricks Magnesia-chrome refractory bricks are directly combined with magnesia-chrome refractory bricks. Combination and semi-combination of magnesia-chrome refractory bricks. Magnesia-chrome refractory bricks are used in refining furnaces outside the furnace, such as VOD, AOD, and RH dipping tubes. A vacuum chamber works better. The main reason for the damage of magnesia-chrome refractory bricks is the spalling of the refractory brick structure caused by the penetration of slag. Magnesia-chrome refractory bricks fired at high temperatures (such as direct combination, recombination, and semi-combination magnesia-chrome bricks) have been widely used in refining furnace linings because of their strong resistance to low alkalinity slag corrosion. There are many varieties of magnesia-chromium refractory bricks, and the production process, organizational structure, and performance are quite different. Magnesia-chrome refractory bricks can be divided into magnesia-chrome bricks according to the Cr2o3 content (Cr2o3 content is 5~20%). Chromium-magnesia bricks (Cr2o3 content is 20~35%) and chrome bricks (Cr2o3 content is greater than 35%) are divided into fired bricks and fused cast bricks according to the production process.
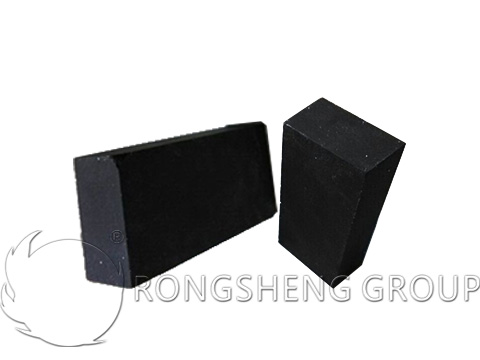
- (1) Directly combined with magnesia-chrome refractory bricks. Directly combined with magnesia-chrome refractories, it is made of chrome concentrate and pure magnesia with low impurity content, and the firing temperature is above 1700°C. Its structural characteristics are that the refractory grains are mostly in direct contact, and the direct combination of periclase (solid solution)-periclase (solid solution) and periclase (solid solution) spinel (solid solution) in the brick is high. Therefore, it has high-temperature performance. Good slag corrosion resistance and high-temperature volume stability is better than ordinary magnesia chrome bricks.
- (2) Semi-bonded magnesia-chrome refractory bricks. Magnesia-chrome bricks with artificial synthetic raw materials as particles and chrome concentrate and magnesia as fine powder are called semi-bonded magnesia-chrome bricks. In my country, fused magnesia-chrome material is used as particles, co-sintered material is used as a fine powder or chrome concentrate, and magnesia powder is used as a mixed fine powder. The produced magnesia-chrome bricks are called semi-bonded magnesia-chrome bricks. The firing temperature is above 1700°C, and the refractory grains in the brick are mainly directly bonded. Its advantages are good thermal shock resistance, corrosion resistance, and good erosion resistance.
- (3) Fused cast magnesia-chromium refractory bricks. Use magnesia chrome ore as the main raw material, add a small amount of additives, and mix. The compact is bisque-fired, broken into pieces, melted in an electric arc furnace, and then injected into a mould. Annealing produces mother bricks, which are made into products of various specific shapes through cold processing such as cutting and grinding. The structural feature of fused cast magnesia-chrome bricks is that the components are evenly distributed. The refractory grains are in direct contact, the silicate is in the shape of an island, and the brick is resistant to melt corrosion. Penetration scour is particularly good, but thermal shock stability is poor.
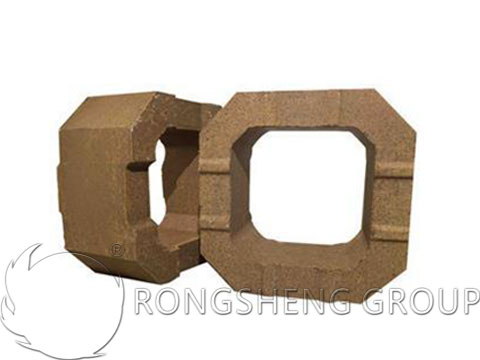
Magnesium-Zirconium Refractory Bricks
Magnesium-zirconium refractory bricks are mainly used for firing magnesia-zirconium refractory bricks. Magnesium-zirconium bricks are refined outside the furnace, such as RH dipping tubes. A vacuum chamber works better. The main reason for the damage to magnesia-zirconium bricks is the structural spalling of the refractory bricks due to the penetration of slag. At present, magnesia-zirconium bricks have not been widely used. On the one hand, zirconium will analyze that the product quality stability is poor, on the other hand, the price is higher than magnesia spinel brick or corundum spinel castable.
Magnesia Spinel Series Refractory Bricks
Spinel series refractory bricks are divided into two categories: magnesium-rich spinel series refractory bricks and aluminum-rich spinel series refractory bricks. Magnesium-rich spinel series refractory bricks are used well in refining furnaces, such as VOD, AOD, RH vacuum chambers, and bottoms. The main reasons for the damage of magnesia spinel bricks are the structural spalling caused by the penetration of slag and the deterioration of bricks. Alumina-rich spinel series refractory bricks are used in refining furnaces, such as the lower and bottom parts of RH vacuum chambers. Dip tubes work better for external use. The damage of aluminum spinel refractory bricks mainly considers melting and structural spalling.
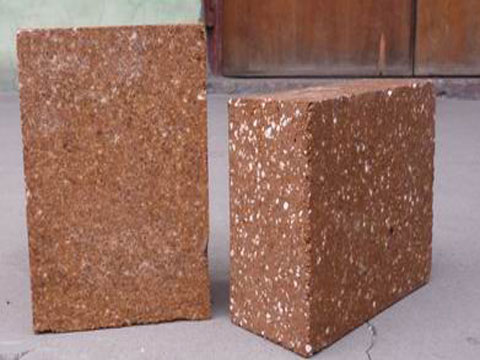
At present, spinel series refractory bricks have been gradually popularized and applied. On the one hand, due to the stable and reliable indicators of the original refractory bricks, the product quality is well-controllable. Spinel itself has the advantages of good thermal shock resistance, good slag resistance, high strength, good volume stability at high temperatures, etc., which significantly improves the performance of refractory bricks. On the other hand, the price is lower than that of magnesia-chrome bricks or magnesia-zirconium bricks, especially non-combustible refractory bricks, which have good energy-saving and emission-reduction effects.
Rongsheng Cheap Fire Bricks Manufacturer
Rongsheng Refractory Brick Manufacturer is a refractory brick manufacturer with rich production and sales experience. Our refractory brick products have been sold to more than 80 countries and regions all over the world, for example, South Africa, Chile, Egypt, Colombia, Uzbekistan, Italy, Indonesia, Ukraine, Hungary, Spain, Kenya, Syria, Zambia, Oman, Venezuela, India, Peru, the United States, Ethiopia, etc. Moreover, our new insulation brick products have good insulation performance and almost no shrinkage under high-temperature conditions. Rongsheng Cheap Fire Bricks Manufacturer sells high-quality magnesia refractory bricks, magnesia chrome bricks, magnesia zirconium bricks, and magnesia spinel bricks, contact us for free samples and quotations.