As we all know, among the refractory bricks used in cement rotary kilns, there are silicon molybdenum bricks, silicon molybdenum red bricks, and magnesium alumina spinel bricks. These refractory bricks are used in different parts of the cement rotary kiln with their unique performance advantages.
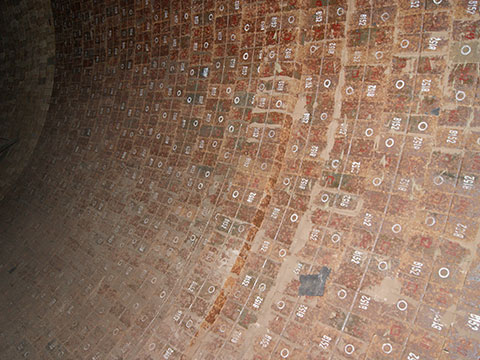
Application of SiC Mullite Bricks and SiC Mullite Red Bricks for Cement Kilns
Silica molybdenum bricks are widely used in the decomposition zone, preheat zone, grate cooler high-wear parts of cement dry kilns, and other high-wind-speed erosion parts. Silica-Mobile red bricks are based on conventional Silica-Mobrick bricks, which further strengthen the thermal shock resistance and heat insulation effect, and at the same time increase the load softening temperature.
Silica molybdenum red bricks have high load-bearing softness, good high-temperature resistance, high strength, wear resistance, not easy to peel off, and corrosion resistance. It has the advantages of low thermal conductivity, good thermal insulation, strong flexibility, good thermal shock resistance, moderate density, and reduced cylinder load. Silica molybdenum red bricks are widely used in the transition zone and cooling zone of rotary kilns. Silica molybdenum bricks and silicon molybdenum red bricks are widely used in high-temperature kilns such as rotary kilns.
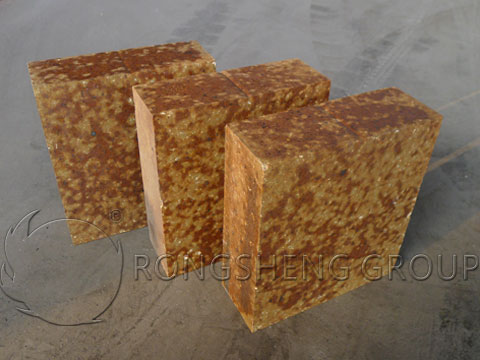
Performance Advantages of SiC Mullite Bricks and SiC Mullite Red Bricks
Silica mullite bricks are fired bricks composed of mullite (3Al2O3·2SiO2) and silicon carbide (SiC) as the main minerals. Also known as SiC-Mullite bricks. The components of silica-molten bricks are special-grade high-alumina bauxite, mullite, silicon carbide, raw bauxite, bonded clay, white corundum bricks, etc. SiC-Mullite bricks have high thermal conductivity and a small thermal expansion coefficient, and the products have good thermal shock resistance.
The brick surface temperature in the transition zone of the cement rotary kiln is around 1400°C, and the temperature in the preheating zone, cooling zone, and other parts are lower than that in the transition zone. The firing zone is protected by the kiln skin, and the temperature of the brick surface is not high. The load softening starting temperature of silica molybdenum brick is above 1500 ℃, especially since the product structure is dense. It is composed of high-hardness minerals, corundum, silicon carbide, and mullite. It has particularly good wear resistance and is an ideal brick type for the transition zone. The compressive strength and load softening temperature are significantly higher than the anti-flaking high-alumina bricks. Its thermal shock stability, corrosion resistance, and wear resistance are good, and the thermal conductivity is not high. It is exactly what the process characteristics of the post-transition zone require, and its service life is 1.5 to 2 times that of anti-flaking bricks.
Silica molybdenum red brick is a transition zone brick developed based on the stringent requirements for refractory materials in large and medium-sized cement rotary kilns. It is based on conventional silica molybdenum bricks by adding andalusite raw materials. Further strengthen the thermal shock resistance and thermal insulation performance, and increase the load softening temperature.
Depending on the raw materials used, the load softening temperature and bulk density of silica molybdenum red bricks are slightly different.
Raw materials used for silicon molybdenum red bricks. Silica molybdenum red bricks are made of special-grade high-alumina bauxite, SiC, andalusite, fused white corundum, raw bauxite, bonded clay, etc., and are fired at high temperatures.
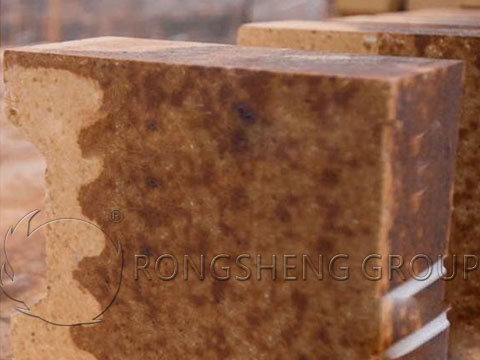
SiC Mullite Red Bricks Have the Following Performance Characteristics
- ① High load-bearing capacity and excellent high-temperature resistance.
- ② High strength, not easy to peel and corrode.
- ③ Low thermal conductivity and good heat insulation effect.
- ④ Strong flexibility and excellent thermal shock resistance.
- ⑤ Moderate density to reduce cylinder load.
What is the Difference between Special SiC Mullite Bricks and Magnesia-Alumina Spinel Bricks for Cement Kilns, and What are Their Performances?
As an indispensable refractory material for building a cement kiln, silico-molybdenum bricks are essentially different from magnesia-alumina spinel bricks. It also has many advantages in all aspects of performance and is extremely suitable as a transition zone. So how to choose silica molybdenum brick? What are the features?
Silica wear-resistant bricks are made of high-quality high-alumina bauxite, silicon carbide, andalusite as the main raw materials. As one of the hardest materials, silicon carbide significantly improves the wear resistance of products. Silicon carbide is oxidized at high temperatures and reacts with high-aluminum matrix components to form secondary mullite, which improves the thermal shock stability and corrosion resistance of the product. Andalusite has micro-expansibility and corrosion resistance, which further improves the high-temperature volume stability and thermal shock stability of the product.
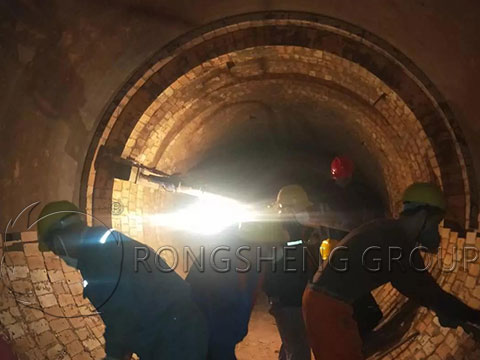
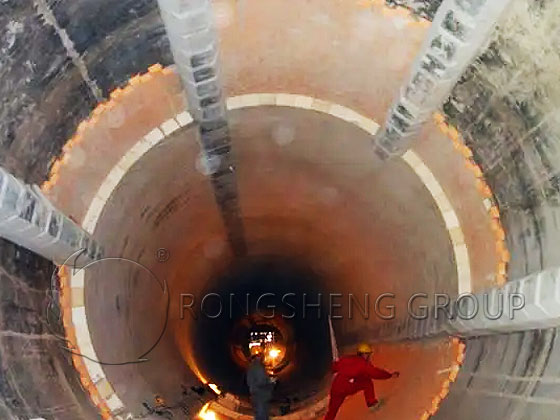
Silica molybdenum brick has a dense structure, high-temperature compressive strength, high-temperature structural strength, and good thermal shock stability. It can continuously form a protective layer during use and has good wear resistance, and strong peeling resistance. It is widely used in the transition zone, preheating zone, tertiary air duct, five-stage preheater, and lime kiln discharge chute of cement rotary kiln.
Compared with magnesia-alumina spinel bricks, the thermal conductivity of silica-molded bricks is relatively low, and under the same conditions, the cylinder temperature of the parts where silica-molded bricks are used is relatively low. Therefore, under the social development trend of increasing emphasis on energy conservation and environmental protection, silica-modified bricks are increasingly used in cement rotary kilns. In general, we usually divide the transition zone into two sections, the upper transition zone and the lower transition zone. Generally, the part close to the preheat zone is called the upper transition zone, and the part close to the kiln entrance is called the lower transition zone. Generally, 1650 silicon molybdenum bricks can be used in the upper transition zone. In the lower transition zone and the kiln mouth, due to the high temperature and serious wear and erosion, only magnesia-alumina spinel bricks or 1680 silica molybdenum bricks can be used. Due to the high temperature in this area, the service life of the refractory materials used in the transition zone is generally about 12 months. 1550 silica molybdenum brick is suitable for the tertiary air ducts of cement production lines with high wind speed and severe erosion, decomposition furnaces with severe material erosion, and fourth- and fifth-level preheaters that are prone to crusting.
Generally speaking, due to its cost-effectiveness, molybdenum silica bricks have a tendency to replace magnesia-alumina spinel bricks in cement rotary kilns in China. Silica molybdenum bricks are mostly used in cement rotary kilns at the end of the kiln and the transition zone. After practice, the transition zone of cement rotary kilns of 4000t/d and below is currently mostly constructed with silica molybdenum bricks. The transition zone of the 5000 t/d rotary kiln is complicated due to working conditions. Although it has been partially adopted, it has not been fully promoted.