Rotary waste incinerators have many properties of waste incinerated, and the lining materials are also different. But at present, the proportion of chrome corundum bricks is the largest. If the waste incinerator is used to process domestic waste, the temperature is relatively low. The rotary waste incinerator processes medical hazardous waste, and the atmosphere and erosion in the furnace are serious. The requirements for refractory materials for lining are relatively high. Usually, the temperature of the hazardous waste furnace is 1400℃~1600℃. At the same time, the acid and alkali components of the molten slag in the furnace add up, causing the atmosphere in the furnace to change continuously.
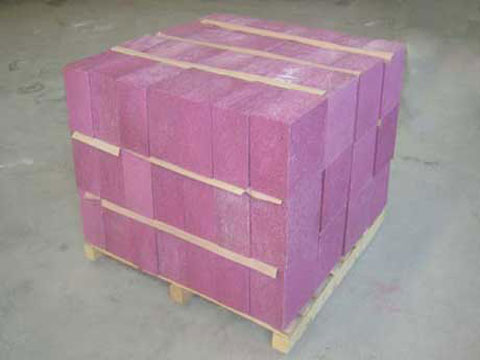
Why is the rotary waste incinerator lined with chrome corundum bricks?
At present, materials such as magnesium chromium, aluminum chromium, high alumina brick, and silicon carbide materials are available in the market. However, due to the uncertainty of the atmosphere, operating temperature, and slag in the waste incinerator, it is difficult for these materials to reach the expected operating time. Chromium corundum bricks are mostly used, which have strong resistance to slag erosion, wear resistance and erosion resistance, and good thermal shock resistance.
Chromium corundum bricks are formed by machine pressing and fired at 1450~1700°C. Especially suitable for the lining of kilns burning toxic waste. Chrome corundum bricks can be used at a temperature of 1700 ° C, and their structural elasticity and corrosion resistance are still very stable.
Why is there uncertainty in the use of chrome corundum bricks?
Chromium oxide has a certain amount of chromium pollution due to its excellent resistance to slag erosion. And after being used for a period of time in the garbage incinerator, the odor will be unbearable, which will damage the human body. Therefore, users who use chrome corundum bricks have also changed to corundum mullite bricks. The bulk density of corundum mullite bricks must be above 2.9 in order to resist strong erosion in the waste incinerator.
Silicon carbide material also has high wear resistance and erosion resistance. The effect of using it in other parts of the waste incinerator is also quite obvious, and it will also become the choice of the chromium-free lining of the waste incinerator.
Chromium corundum bricks have strong corrosion resistance and wear resistance, but chrome pollution is a major influence. Therefore, whether chrome corundum bricks are suitable for rotary waste incinerators also needs to be considered.
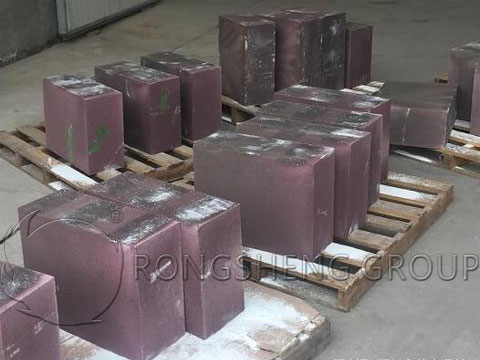
The working conditions of the rotary kiln waste incinerator are harsh
The rotary kiln waste incinerator is one of the processing equipment for incinerating waste (including domestic waste and medical waste). It can fully guarantee the environmental protection requirements of stabilization, safety, reduction, and harmlessness of medical waste. At the same time, it is in line with the development trend of contemporary medical waste treatment. The temperature in the waste incinerator is usually 1400 ℃ ~ 1600 ℃, and some parts reach 1700 ℃. The molten slag in contact with the hot surface area in the furnace contains Na2O, K2O, C1-, K2SO4, etc., with an alkalinity of 0.3~1.5. The rotation mode of the rotary kiln is positive and negative swing, and the atmosphere in the furnace is constantly changing. Garbage types, moisture content, etc. vary greatly. Therefore, refractory materials are required to have excellent resistance to slag erosion and permeability. High strength, erosion resistance, wear resistance, and good thermal shock resistance to adapt to the impact of mechanical stress and thermal stress. At present, the refractory materials used in waste incinerators mainly include magnesium chromium, aluminum chromium, high aluminum, silicon carbide, and other materials. However, due to the uncertainty of the atmosphere in the furnace, the operating temperature, the calcium-silicon ratio in the slag, and the variability of garbage types, it is difficult for the above materials with better performance to achieve their expected use effects.
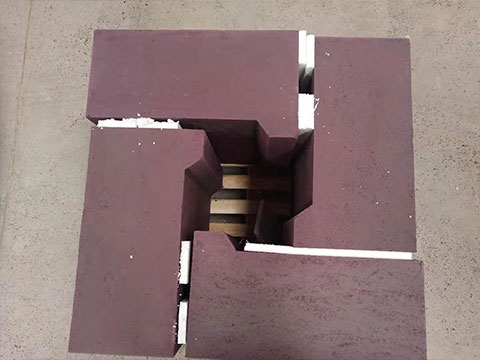
Application advantages of chrome corundum refractory bricks in waste incinerators
A refractory material and a related refractory brick are provided for a rotary kiln burning waste, especially a rotary kiln burning toxic waste. It can be used in furnaces with slag, severe thermal shock, and high operating temperature (1600°C). Refractory brick material manufacturers provide chrome corundum material, and chrome corundum bricks are made from this material.
Specifically, the composition of this chrome corundum brick refractory material is as follows, 5%~35% (a more suitable amount is 10%~30%) Cr2O3, and the particle size is <0.1mm. 1%~10% (more suitable amount is 3%~6%) ZrO2, particle size 0.5~4.0mm. 55%~94% (more suitable amount is 62%~87%) Al2O3 (corundum), particle size is 0.2~0.4mm. This chrome-corundum material can be machined or rammed into bricks. Firing between 1450~1700°C.
By selecting the corresponding raw materials, adjust the content of Cr2O3, ZrO2, and AL2O3 and SiO and Fe2O3 in the raw materials (the content of Fe2O3 should be <0.5%) to ensure that the particle size of each raw material is consistent with the above mentioned. This chrome corundum brick can be made by firing at 1450~1700°C. The open porosity of this brick is between 9% and 18%, the elastic modulus is less than 3000MPa, and the temperature cycle stress value is greater than 30.
By changing some of the parameters mentioned above, the modulus of elasticity of the brick can be reduced to 1500Mpa. This chrome corundum brick has good corrosion resistance and is especially suitable for rotary kilns burning toxic waste. This kind of brick is used at a temperature as high as 1700 ℃, and its structural elasticity and erosion resistance is still very good.
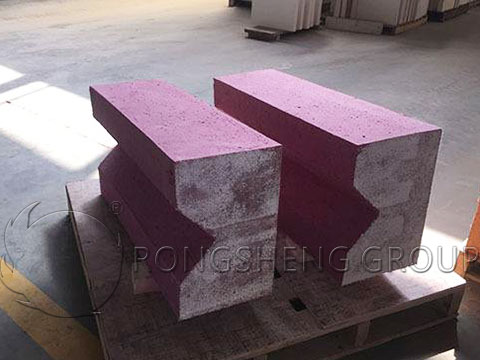
Development trend of refractory materials for waste incinerators
(1) Due to its excellent slag erosion resistance, chromium oxide bricks will continue to be used as linings for waste incinerators, but their high density and strength lead to poor toughness of the material. Therefore, the material has poor structural spalling resistance, and the method of introducing microcracks into the material can balance the gap between the material’s erosion resistance and spalling resistance. (2) Most waste incinerators are equipped with water-cooled structures, and SiC castables are ideal masonry materials due to their high thermal conductivity. Its use in other parts of waste incinerators will also become an important direction for chromium-free refractory materials for waste incinerators. (3) The chromium-free refractory materials used in waste incinerators will continue to be documented as the focus of research.
Buy refractory materials for waste incinerators and refractory materials for rotary waste incinerators. Please choose a strong Rongsheng refractory manufacturer. The refractory products of our refractory factory meet the requirements of environmentally friendly production, covering various alumina bricks, chrome alumina series, corundum bricks, chrome bricks, etc. It has been sold to more than 70 countries and regions around the world. For example, South Africa, Philippines, Chile, Malaysia, Indonesia, Vietnam, Kuwait, Turkey, Zambia, Peru, Mexico, Qatar, Egypt, Russia, Kazakhstan, etc. Contact Rongsheng manufacturers to obtain samples and price information of chrome corundum refractory bricks for free, so as to save production costs for your production.