As the prices of natural gas, heavy oil, and coal tar continue to rise. Petroleum coke powder has the characteristics of high calorific value, easy processing, good fluidity, cheap price, and convenient supply. Driven by some manufacturers and technicians, it has become an emerging fuel that gradually replaces the above-mentioned energy sources. However, this fuel substitution has brought about various problems. Some petroleum coke powder manufacturers may not have discovered its negative effects yet due to the short time of promotion and use. Or they are aware of the disadvantages but avoid talking about them in actual use. The sulfur, vanadium, and small amounts of alkali metals, nickel, and iron introduced by this kind of fuel have the most serious corrosion on the kiln refractory materials, especially the alkaline materials such as the regenerator walls and grids. The influence of the carbon and sulfur-reducing atmosphere flame on the melting process and the influence of trace elements such as nickel, manganese, and titanium on the quality of the glass cannot be ignored.
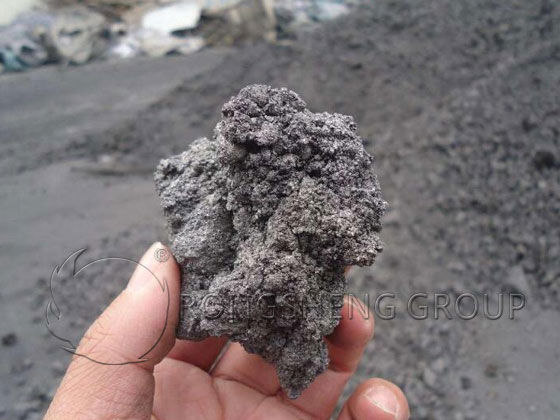
Erosion of petroleum coke powder to regenerator refractory materials
(1) Direct burning damage to regenerator refractory material caused by petroleum coke powder flame
After using petroleum coke powder for fuel replacement, the combustion process characteristics of petroleum coke powder are different from those of coal tar, natural gas, and other liquid and gaseous fuels. Petroleum coke is a solid fuel. After processing and grinding, the particle size reaches 200 mesh (0.074mm). However, its powder flow characteristics are still quite different from those of liquids and gases. The carbon particles in the coke powder are not fully mixed with the combustion air, and the black zone of the flame is long. The length of the black zone is about 1m, resulting in a lower temperature at the fire root and a higher temperature at the fire tip. In addition, the petroleum coke powder transportation atomization system is sometimes not stable enough, showing a surge and becoming “jumping powder”, which makes the flame unsuitable for adjustment and control. Therefore, the flame of petroleum coke powder is relatively turbid, the flame oxidation is not enough, the combustion speed is slow, and the flame stroke is long. Unburned carbon powder can easily enter the opposite small furnace and the upper part of the grid body. Secondary combustion occurs in this part with the residual oxygen in the flue gas, resulting in a higher temperature in the upper part of the grid body and serious damage to the small furnace and regenerator.
(2) The erosion mechanism of petroleum coke powder on alkaline materials
The upper walls of the heat storage room and exterior walls are made of electro-fused and bonded 97 magnesia bricks. The bricks appear to be “cracking”, peeling and partially collapsed. The erosion is mainly due to the reaction of SO3 and V2O5 contained in petroleum coke powder combustion products at high temperatures with CaO, MgO, and other components in alkaline materials under the action of glass dust SiO2. Generate dicalcium silicate (C2S), forsterite (CMS), forsterite (M2S), rhodonite (C3MS2), calcium vanadate, etc. that are eutectic, easy to peel off, and have large volume changes.
The reaction causes the volume of the brick surface to expand, causing tiny cracks to appear. Over time, the cracks gradually increase until they peel off. It seriously affects the structural strength and service life of the bricks, and is the intrinsic reason for the burning of the regenerator wall.
The main reasons for the erosion of high-purity magnesia bricks by V2O5 in petroleum coke powder flue gas are as follows.
The V2O5 in the petroleum coke powder flue gas penetrates, causing the fused magnesia bricks to densify and cause initial erosion of CaO in the interstitial phase of the calcite. This is mainly because V2O5 and Ca easily combine to form calcium vanadate and calcium magnesium vanadate in an oxidizing atmosphere, and they easily form calcium vanadate in a reducing atmosphere. V2O5 erodes the brick interstitial phase Ca2SiO4, causing CaO to escape from Ca2SiO4. As MgO is eroded, Ca3Mg(SiO4)2 (rhodonite C3MS2) is formed. According to the analysis of the test results of high-purity magnesia brick samples after using petroleum coke powder as fuel. When V2O5 erodes the brick interstitial phase Ca2SiO4, it will also cause the final formation of Mg2SiO4 (forsterite M2S), which coexists with the vanadate phase and MgO.
These newly formed low-melting vanadate phases sparsely surround single and gradually growing periclase crystals in the sample. When the interstitial phases CaO and MgO are eroded, the increase in vanadate disperses and isolates periclase crystals. The result of erosion is a weakening of the bond strength and structural degradation. In the CaO-MgO-V2O5 system, V2O5 erosion can be observed at approximately 1100°C.
Due to the condensation of the binding phase, the growth of periclase crystals, and the formation of coarse pores, the magnesia brick structure is significantly densified and embrittled. Experimenters observed the growth of periclase crystals in high-purity magnesia bricks. Depending on the run time and the presence of melt to support crystal growth, up to 10 times the size of the original periclase crystal. All structural degradation processes cause structural fragility in solid-phase systems. Even under normal thermal cycling, prolonged loading may cause chipping. At higher temperatures, since the vanadate in the interstitial phase melts first, the refractory resistance of the material will decrease sharply and cause mechanical creep to deform and bend.
Therefore, in a sense, energy cost control and changes in operating conditions come at the expense of reducing the life of refractory materials. As the demand for lower energy costs grows, fuel corrosiveness is also likely to increase.
Blockage of the grid mainly comes from two reasons
On the one hand, during the long-term operation of the kiln, the ash and glass dust in the petroleum coke powder exhaust gas form vitrification on the surface of the grid. Then they accumulate and adhere to the surface of the lattice body, causing its volume to gradually expand and the lattice holes to decrease.
On the other hand, it is due to the daily peeling, collapse, cracking, and falling of impurities from the walls and grids inside and outside the regenerator, as well as the broken bricks dropped during hot repair of the target wall of the regenerator, etc., which blocks the upper grid. Resulting in blockage of the upper lattice body pores.
Therefore, when saving production energy, the refractory materials will be damaged to a certain extent. Therefore, refractory brick material manufacturers and production enterprises can modify refractory materials or appropriately improve production energy according to changes in their production conditions. Strive to save production energy while also reducing damage to refractory lining materials. Help enterprises better save production costs.