The existence of pores in refractory materials will lead to a decrease in their density and effective section, resulting in changes in their mechanical and thermal properties. The performance of refractory bricks under a thermal heavy load and resistance to thermal shock and slag corrosion is also significantly affected. In refractory brick products, there are many pores of different sizes and shapes. The pores of refractory bricks can be roughly divided into three categories:
- (1) Open pores, one end is closed, and the other end communicates with the outside world;
- (2) Closed pores, closed in the product and not connected to the outside world;
- (3) Through the air hole, through both sides of the refractory product, the fluid can pass through.
The through-holes are easy to pass through the fluid, so that the corrosive fluid can easily penetrate into the product, and the slag corrosion is aggravated. Open pores can allow fluid to intrude, but when fluid invades, the gas in the pores is compressed, which inhibits the intrusion of fluid, so the hazard of slag erosion is smaller than that of through pores. The closed pores are not intruded by external gas and liquid, and the damage of slag corrosion is small. Sometimes it may also reduce thermal conductivity and facilitate thermal shock resistance.
The pores in refractory bricks that have a significant impact on their physical properties can be divided into coarse pores and cracks above 1 mm; coarse pores above 25 μm and fine pores between 0.1 and 25 μm. Pores of different sizes have different effects on the properties of materials.
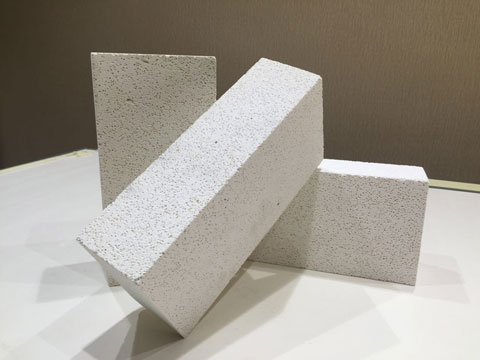
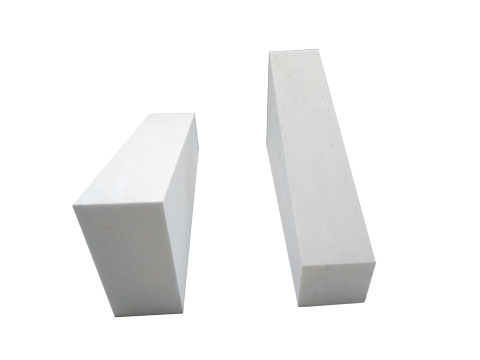
The Porosity of Refractory Bricks
When the pores of the refractory brick contain various pores, the ratio of the volume of the pores to the total volume of the material is called the apparent porosity, also known as the open porosity. Usually, the porosity is expressed as a percentage.
Apparent porosity is one of the important indicators to identify the quality of refractory materials. During use, refractory bricks with large porosity are easily eroded by molten hawthorn and are easy to absorb water during storage and operation. Therefore, the apparent porosity is generally stipulated in the quality index of refractory bricks. For example, the apparent porosity of ordinary clay bricks should not exceed 20% according to the original Ministry of Metallurgy standard.
Porosity refers to the percentage of the volume of pores contained in refractory bricks to the total volume of the product. According to Rongsheng refractory brick manufacturers, the pores in refractory bricks are divided into two types, closed pores, and open pores. The pores that are closed in the refractory brick and do not communicate with the outside world are called closed pores. The pores that communicate with the outside world and can be filled with fluid are called open pores. Among the open pores, the pores that run through both sides of the product and can pass through the fluid are also called through pores.
The Porosity of Refractory Bricks for Blast Furnaces
Different from the tuyere combined refractory bricks for blast furnaces, the ratio of the open pore volume to the total volume of the product is called the open porosity. Often called apparent porosity, denoted as pa. The ratio of the volume of closed pores to the total volume of the product is called the closed porosity, denoted as pc. The ratio of the total pore volume to the total volume of the product is called the true porosity, denoted as pt. The relationship between the three is pt=pa+pc. Except for cast products, asphalt-bonded or impregnated products, and some heat-insulating refractory products, most of the pores in general refractory bricks are open pores. And because the volume of closed pores is difficult to measure directly, the porosity index of products is usually expressed by apparent porosity. The apparent porosity of refractory bricks can be as small as close to zero or as large as 80%. Generally, the apparent porosity of dense products is between 10% and 28%, and those less than 15% are called low porosity products. The true porosity of the insulation material is greater than 45%. Porosity is the basic technical index of most refractory materials. Its size affects almost all properties of refractory products, especially strength, thermal conductivity, slag resistance, and thermal shock resistance. The porosity increases and the strength decreases. This is not just an increase in actual stress due to a decrease in the cross-sectional area of the solid. More importantly, pores are defects in the material, which will cause stress concentration and reduce strength. The effect of coarse stomata is more pronounced.
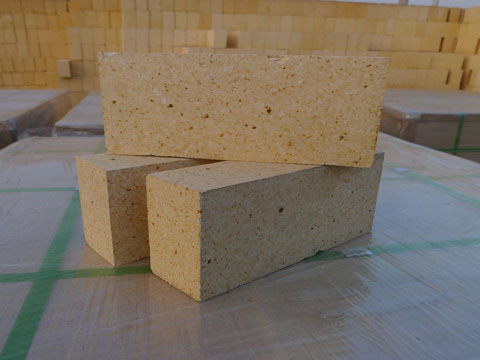
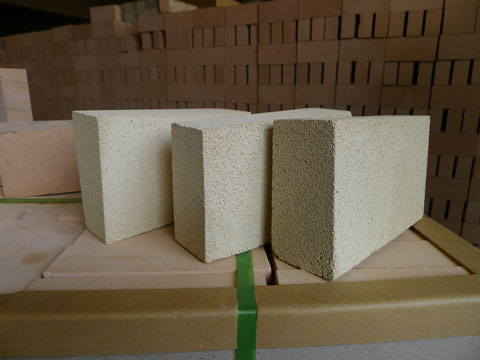
Since the thermal conductivity of air itself is extremely low, increasing the porosity can significantly reduce the thermal conductivity. The large porosity increases the penetration of slag to the product or intensifies the oxidation of carbon in carbon-containing refractory materials, which significantly reduces the slag resistance of the material. Due to the complex influence of porosity on strength, thermal conductivity, linear expansion coefficient, elastic modulus, etc., the influence of thermal shock resistance is also complicated. Rongsheng refractory brick manufacturers pointed out that reducing the porosity is also beneficial to improving the load softening temperature and high-temperature creep of refractory materials. The pores in refractory products are brought in by the raw materials themselves and formed during the molding, drying, and firing processes. It is distributed in the particles, the matrix, and between the particles and the matrix.
It is reported that different refractory materials have certain requirements on the size of the porosity. To produce dense products with low porosity, the first condition is to select raw materials with low porosity. According to the principle of dense packing of Rongsheng refractories, adopting reasonable particle grading, rational use of binders, fully uniform mixing, high-pressure molding, appropriately increasing firing temperature, and prolonging holding time are all important measures to reduce porosity in the production of dense refractory materials. In the production of dense castables, adding ultra-fine powder and dispersant to the ingredients can form tighter packing and obtain products with low porosity. In the production of heat-insulating refractory products that require high porosity, heat-insulating material raw materials are used, and chemical foaming or combustible materials are added to the ingredients to generate pores and increase the number of pores.
Rongsheng Cheap Refractory Fire Brick Manufacturer
Rongsheng refractory brick manufacturer is a refractory brick manufacturer with rich production and sales experience. Our professional technical team and advanced refractory brick production workshop provide our customers with high-quality refractory brick products and technical support. In addition, we can also provide customers with customization of refractory lining materials according to their actual production needs. Contact us for free samples of low-porosity refractory bricks and quotes for refractory lining designs.