Refractoriness refers to the Celsius temperature at which a refractory cone sample can resist high temperatures without softening and melting under no load. Refractory materials are widely used in metallurgy, chemical industry, petroleum, machinery manufacturing, silicate, power, and other industrial fields. It is the largest in the metallurgical industry, accounting for 50% to 60% of the total output. Now, Rongsheng refractory material manufacturer will take you to understand how to use refractory materials in an environmentally friendly cement rotary kiln.
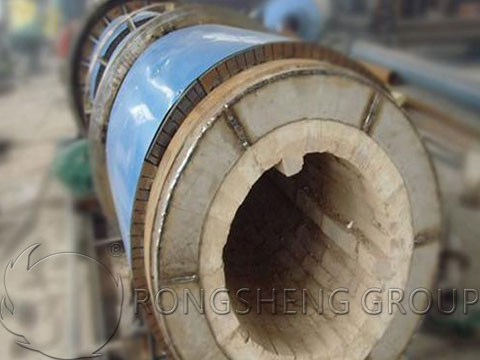
In the production process of environmentally friendly cement rotary kiln, the correct and reasonable use of refractory materials can effectively extend the use time of refractory materials, reduce the maintenance rate of environmentally friendly cement rotary kiln bodies, and improve production efficiency. We know that the inner lining of the environmentally friendly cement rotary kiln will vibrate with the rotation of the environmentally friendly cement rotary kiln, and will also be subject to wear and impact from the charge. The masonry existing in the burning zone will be corroded by the high temperature and the ash contained in the pulverized coal. This requires the refractories of environmentally friendly cement rotary kiln masonry to have high-temperature resistance, stability, wear-resistance, and high strength corrosion resistance.
Use of refractory materials in various parts of environmentally friendly cement kiln
In the interior of the environmentally friendly cement rotary kiln, different areas have different heating temperatures because of different working principles and characteristics. Therefore, the refractory bricks used are different. So, what kind of refractory bricks should be used in the main parts of the environmentally friendly cement rotary kiln?
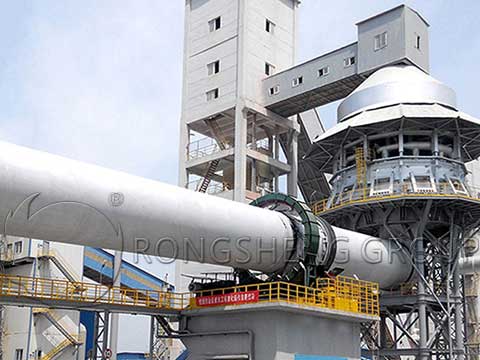
- First, let’s take a look at the kiln mouth. It is best to use refractory materials resistant to thermal shock at the kiln mouth. Such as wear-resistant and heat-resistant high-alumina bricks or steel fiber reinforced castables and low-cement high-alumina castables. However, in large kilns with extremely high kiln mouth temperatures, ordinary or steel fiber reinforced corundum casting should be used.
- The preheating zone generally uses phosphate combined with high alumina bricks, anti-stripping high alumina bricks, or alkali-resistant bricks. The decomposition zone generally uses anti-stripping high alumina bricks. Silica-mold bricks are better than anti-stripping high alumina bricks in performance, and their service life is about twice as long as anti-stripping high alumina bricks, but the price is higher. The kiln tail inlet should adopt anti-skinning silicon carbide castable.
- The kiln skin in the transition zone is unstable, and the kiln lining is required to have good resistance to atmosphere changes, good thermal shock stability, low thermal conductivity, and wear-resistant materials. It is recommended to use magnesia-alumina spinel bricks abroad, but the bricks have high thermal conductivity, high temperature of the cylinder, and relatively large heat consumption, which is not conducive to reducing energy consumption. The domestic silicon-mold bricks have low thermal conductivity, abrasion resistance, and their performance is comparable to imported materials to a certain extent.
- The temperature of the firing zone is high, the flame temperature is above 1,700 ℃, and the chemical reaction is intense. The infiltration of the clinker liquid phase and molten fuel ash at high temperature, as well as the infiltration of kiln gas with alkali sulfate and alkali chloride, etc., have a strong chemical attack on various refractory materials. In kilns where the oxidation-reduction atmosphere is frequently alternated, sulfides are easy to form and condense in the bricks. When the kiln is shut down, it is converted to an oxidizing atmosphere, and the sulfide is converted into sulfate, and the volume increases. Such repeated cycles destroy the structure of the brick and cause the brick to crack. Therefore, in the firing zone, the brick lining is required to be resistant to clinker erosion, and to have a strong resistance to SO2 and CO. Magnesia-alumina spinel bricks are generally used abroad, but it is difficult for the bricks to hang in the kiln. However, dolomite bricks have poor thermal shock stability and are easy to hydrate. Foreign mafic-iron sharp grade stone bricks have a better effect on hanging kiln skin, but the cost is too high. The new low-chromium periclase composite spinel bricks used in China are better.
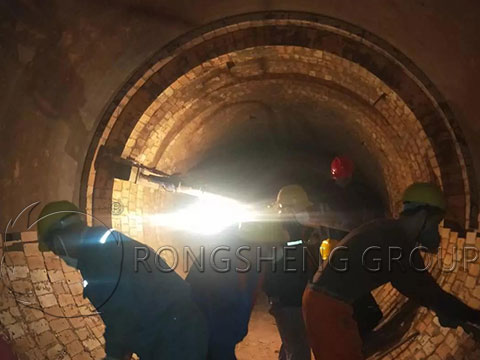
The cylinder of the environmentally friendly cement rotary kiln is not completely rigid. Coupled with the influence of too large ellipse of the kiln, the kiln body of the environmentally friendly cement rotary kiln, especially the tyre part, has large or small deformation during the rotation of the kiln. Compressive, tensile, and shear stresses in the kiln lining, coupled with the continuous relative displacement and local stress between the refractory bricks, causing the bricks to break, crack, peel off, and even fall off. During the heating and cooling process of the kiln lining, the temperature difference stress f thermal stress is generated, which can also cause cracking and peeling of the bricks. There is also a chemical attack to form some new minerals, resulting in volume changes, and also causing new mechanical stress in the bricks. All of the above require refractory bricks to have sufficient strength at room temperature and high temperature before they can be used normally.
Rongsheng Refractory Bricks Manufacturer
Rongsheng refractory bricks manufacturer is an experienced refractory material manufacturer. Rongsheng’s experienced refractory material-technical team provides customers with the production and development of high-quality refractory lining materials. Rongsheng’s refractory products have been sold to more than 60 countries around the world, for example, Thailand, UAE, Turkey, Kuwait, South Africa, Malaysia, Vietnam, Netherlands, Philippines, Singapore, Egypt, Russia, etc. If you want to know Rongsheng refractory material manufacturer or your cement kiln needs refractory lining, please contact us. We will provide you with satisfactory service based on the information on the working conditions of the cement kiln provided by you.