In addition to lining bricks, sleeve bricks, plug bricks, nozzle bricks, and seat bricks are also used in the steel ladle to control the steel flow. Some also use sliding nozzle bricks or rotating nozzle bricks instead of sleeve bricks and plug bricks. This article will help you understand the role of sleeve bricks, plug bricks, and nozzle bricks in controlling steel flow.
(1) Sleeve Bricks
The tapping sleeve is the channel for the molten steel from the converter to flow to the ladle. It is in direct contact with molten steel, and its life directly affects the steelmaking rhythm of the converter. Structurally, tapping sleeve bricks are divided into integral sleeve bricks (also known as tapping pipe bricks) and split sleeve bricks. The integral sleeve brick is generally formed by isostatic pressing, and the split sleeve brick is formed by machine pressing. In order to be easily installed on the converter, the tap sleeve brick is usually used after assembling a steel pipe and a flange.
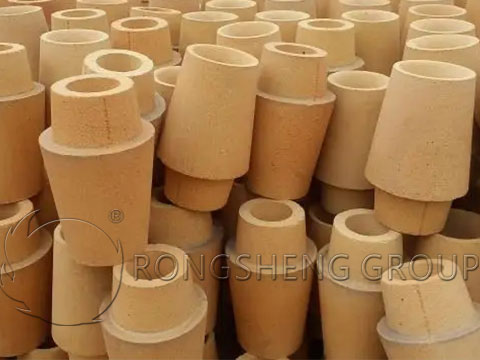
Whether it is an integral type or a split type sleeve brick, the tapped sleeve brick is generally round in shape. The inner hole is a circular structure of a through-hole, the size of the inner hole is determined according to the tapping time, and the wall thickness is generally 50 ~ 100mm. The shape of the hole is divided into a straight-through shape and a flared shape. Experiments have shown that the tapping speed of the tapping hole with a flared inner hole and a circular inlet shape is higher. This means that the interference between the molten steel and the tapping port is weakened, the flow rate of the molten steel is relatively stable, and the round inlet of the tapping port shortens the tapping time.
The working conditions and damage of sleeve bricks are basically the same as those of ladle lining bricks. Often damaged by melting, spalling, and breaking. Slag corrosion is particularly serious at the slag line. The erosion of the brick joints is also heavier. The sleeve bricks of the ladle for degassing and continuous casting use high-alumina bricks or zircon refractories at the slag line or all. In addition, there are also examples of using double-layer sleeve bricks. The outer sleeve bricks are made of chrome-magnesium or high-alumina castables. Others use air-cooled plugs to reduce the erosion rate of sleeve bricks. Generally, the thickness of the sleeve brick is increased to prolong the service life.
(2) Plug Bricks
The plug brick is always under the high temperature of the molten steel and the scour of the steel flow. In order to effectively control the steel flow, it is required that the working surface must be closely matched with the nozzle brick, and no gaps should be generated due to deformation and local corrosion. In order to ensure that the plug rod does not have a broken end accident, the plug head brick cannot be broken due to mechanical action and alternating cold and heat, nor can the metal rod core be embrittled and fused due to the carburizing effect and high thermal conductivity of the plug head brick. . Therefore, the plug brick must be resistant to high temperature, erosion, thermal shock and have relatively high strength.
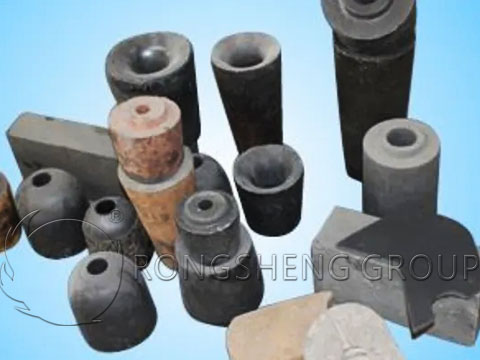
In ordinary ladles, clay stopper bricks are generally used. Among them are fired bricks and unfired bricks combined with water glass. There are also carbon-containing products that have been oil-immersed and light-burned, carbonized by about 5%, and their strength has been improved. In addition, graphite and silicon carbide are added to the clay ingredients to make graphite clay plug bricks containing 15-45% of SiC and C.
For some special steels with high tapping temperature, such as ladle for high manganese steel and stainless steel (or ladle for continuous casting). In order to avoid the damage of the clay plug brick, reduce the intermittent deformation and local corrosion of the plug brick, ensure that the steel flow rate can be strictly controlled and precisely adjusted, and avoid the phenomenon of easy embrittlement and fracture due to carburization of the graphite plug brick, using high alumina plug bricks and zircon plug bricks. Some also use alkaline plug bricks.
(3) Nozzle Bricks
Nozzle brick is also called casting brick. Insert into the base at the bottom of the ladle. It is the place where the molten steel in the barrel must pass. Works with stopper bricks to control steel flow. The erosion effect received by the nozzle brick is basically the same as that of the plug brick, but the erosion is more serious.
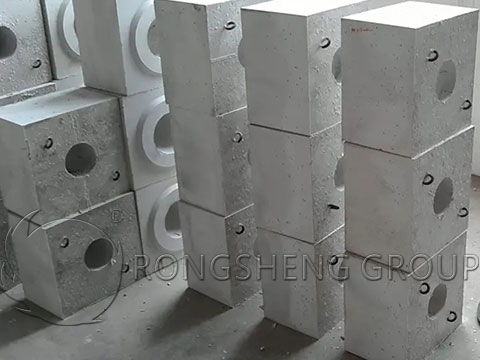
The material used for the nozzle brick is similar to that of the plug brick. It must be ensured that it will always fit tightly with the plug brick. For this reason, the nozzle brick should have proper thermoplasticity at high temperatures. In addition, the nozzle brick should have high volume stability at high temperatures.
Rongsheng Refractory Brick Manufacturer for Foundry Industry
As a powerful refractory brick manufacturer, Rongsheng’s refractory products have been sold to more than 70 countries around the world, such as South Africa, Philippines, Chile, Malaysia, Indonesia, Vietnam, Kuwait, Turkey, Zambia, Peru, Mexico, Qatar, Egypt, Russia, Kazakhstan, etc. In the production of refractory bricks for casting, such as hollowware, sleeves, nozzles, rotolox stoppers, high-alumina sleeve bricks, cast tube bricks, etc., we strictly control the quality management and provide customers with high-quality refractory bricks. At the same time, the skateboards, nozzles, and blocks of Rongsheng manufacturers also received continuous returns from customers. We provide global service, free to get the prices and samples, please contact us. Looking forward to meeting you in the vast crowd.