Refractory bricks are the basic materials used in high-temperature kilns and are closely related to the masonry of kilns in various industries. Various industrial kilns have different requirements for refractory bricks, which are the basic materials of their main body, due to their different purposes and conditions of use. Different types of refractory bricks also show different basic characteristics due to differences in chemical mineral composition, microstructure, and production processes. Therefore, if we want to build high-quality industrial kilns, we must master the knowledge of refractory bricks.
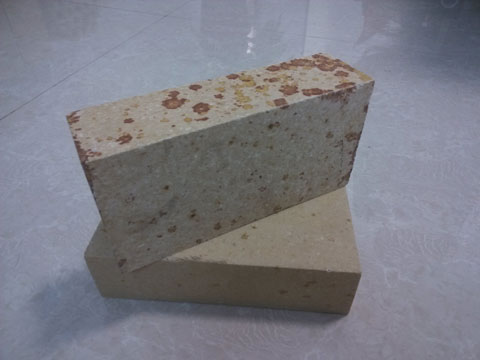
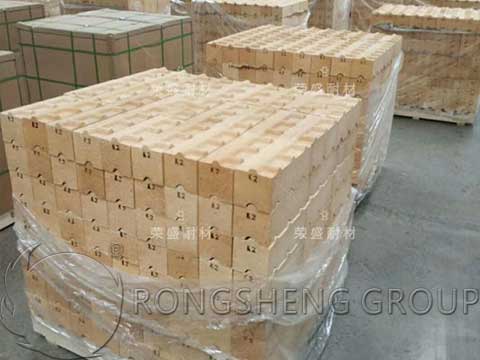
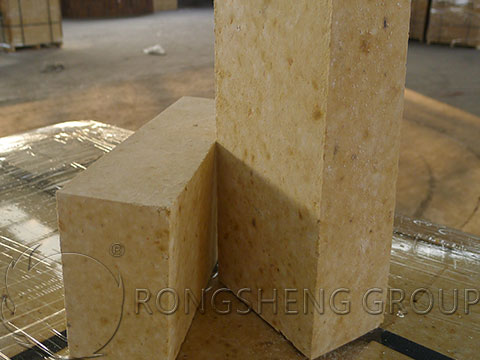
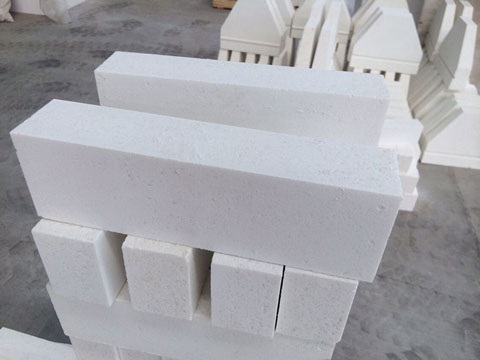
Below, the editor from Rongsheng introduces silica-alumina refractory bricks for everyone. In the refractory industry, silicon-aluminum refractory bricks are based on the phase diagram of the AL2O3-SiO2 binary system as the basic theory. It mainly includes the following four types.
Classification of Aluminum Silicate Refractory Bricks
- Silica brick. Silica bricks are mainly acid refractory materials composed of tridymite, cristobalite, and a small amount of residual quartz and glass phases. The silica content is above 94%. The true density is 2.35g/cm3. It has resistance to acid slag erosion. Higher high-temperature strength. The starting temperature of load softening is 1620~1670℃. It will not deform after long-term use at high temperatures. It is mainly used for building coke ovens, but also for the vaults and other load-bearing parts of thermal kilns for various glass, ceramics, carbon calciners, and refractory bricks. It is also used in the high-temperature load-bearing part of the hot blast stove. However, it is not suitable to be used in thermal equipment below 600°C and with large temperature fluctuations.
- Fireclay bricks. Fireclay bricks are made of 50% soft clay and 50% hard clay clinker, which are batched according to certain particle size requirements. After molding and drying, it is fired at a high temperature of 1300 to 1400°C. Clay bricks are weakly acidic refractory products, which can resist the erosion of acidic slag and acidic gas, and have slightly weaker resistance to alkaline substances. Clay bricks have good thermal properties and are resistant to rapid cold and rapid heat. It is a refractory brick commonly used in blast furnaces, hot blast stoves, heating furnaces, power boilers, lime kilns, rotary kilns, glass kilns, ceramics, and refractory brick firing kilns.
- High alumina bricks refer to an aluminum silicate refractory with an Al2O3 content of more than 48%. It can be classified according to its mineral composition, generally divided into five types of refractory bricks: low mullite, mullite, mullite-corundum, corundum-mullite, and corundum. Its mineral composition is mainly corundum, mullite, and glass phases. The softening temperature of high alumina refractory bricks increases with the increase of Al2O3 content. High alumina bricks are widely used in the steel industry, non-ferrous metal industry, and other industries.
- Corundum bricks. Corundum brick refers to a refractory brick with an AL2O3 content of not less than 90% and corundum as the main phase. After scientific and reasonable grading, adding high-performance additives, high-pressure molding, high-temperature sintering made of refractory products. Its characteristics have excellent corrosion resistance, wear resistance, high-temperature strength, load softening, creep, and other thermodynamic properties. It is widely used in important parts such as metallurgy, chemical industry, ceramics, glass, non-ferrous metals, refractory materials, high-temperature furnace lining, combustion chamber, and so on.
Application of Aluminum Silicate Refractory Bricks
Aluminum silicate refractories often contain 5-6 kinds of impurity oxides such as Fe2O3, TiO2, Ca0, Mg0, K2O, and Na20. These impurities exist in the silicon-aluminum binary system and have a great influence on the refractoriness of aluminum silicate refractory materials products.
Aluminum silicate refractories have a wide range of raw materials, simple production process, low cost, low price, and high-temperature adaptability. Furnaces in the industrial sectors of metallurgy, machinery, chemical industry, power, and silicate are widely used aluminum silicate refractory materials as the main furnace building materials. Among them, the most used are the metallurgical industry, blast furnaces, hot blast furnaces, mixing furnaces, heating furnaces, and soaking furnaces in the iron and steel metallurgical industry. And thermal equipment such as rotary kilns, boiling furnaces, blast furnaces, reverberatory furnaces, aluminum melting furnaces, and non-ferrous metal heating furnaces in the non-ferrous metal industry. These thermal kilns all use a large number of clay bricks, high alumina bricks, mullite products, and corundum products as furnace building materials.
For example, the first-grade high alumina bricks for activated carbon high-temperature converters of a certain company are aluminum silicate refractory bricks with an Al2O₃ content of not less than 75%. The production process is similar to clay refractory bricks. According to the different grades of bauxite clinker used, different quality requirements, and the choice of formula binding agent, the appropriate proportion is distributed, and it is formed by using a brick press and then calcined. This high alumina brick is a neutral refractory material. It has good resistance to acid, alkali slag, corrosion of molten metal, oxidation and reduction reactivity, etc. It also has the characteristics of high thermal stability, refractoriness above 1790℃, and good slag resistance.
FAQ:
Q: How are the aluminum silicate refractory materials’ inner-black bricks made of?
Answer: The outside of the aluminum silicate refractory brick is yellow, but the inside is black. This may be because there is a problem with the raw materials used to make the refractory bricks, which may contain too much iron.