The lining of the rotary kiln used for the production of soda sulfide originally used grade I high-alumina bricks. Due to bursting and large pieces of peeling, accompanied by falling bricks and erosion, not only the service life of the furnace lining is affected, but also the product quality is also affected to a certain extent. Therefore, analyze and solve this situation to ensure the healthy and long-lived operation of the kiln.
Working Conditions of Refractory Brick Lining of Alkali Sulfide Rotary Kiln
The length of the rotary kiln for the production of soda sulfide is 36m, of which the drying zone, the pre-tropic zone, and the soaking zone are 10 meters each. The material outflow outlet in the soaking zone is open, and the maximum working temperature is 1200°C, and the minimum is about 700°C. The action time of materials in the furnace is 1~1.5h, and the production method is pulverized coal reduction method. which is:
Coal powder + sodium sulfate (glauber’s salt) → (reduction reaction at 1150~1200°C) → melt → leaching → solid-liquid separation → evaporation → packaging
Why is the refractory brick lining of the soda sulfide rotary kiln easy to peel off?
According to on-site observations, during use, due to the limitation of production conditions, the temperature changes greatly, and the high-alumina bricks are eroded by rapid cooling and heat and molten materials for a long time, resulting in severe cracking and peeling, and some bricks are falling off. After 4 months of production, only 40~50mm of bricks remained (the length of the original brick was 206mm), and production could no longer be maintained.
From the side reactions in the production of soda sulfide, the chemical analysis of the crushed slag during the production of soda sulfide was carried out. Results (%): SiO2/4.14, AL2O3/4.0, Na2CO3/2.63, Na2S/0.63, Na2SO3/0.06, Na2S2O3/6.13, Na2SO4/68.65. The different metamorphic regions of residual bricks are divided into reaction zone, transition zone and original brick zone. In the reaction zone, there are relatively large mullite, a large amount of corundum with low birefringence, and short columnar nepheline. The closer to the brick body, the smaller the nepheline particles. The transition zone maintains the structure of the original brick, and the development of mullite can still be seen in the particle gaps. In the original brick belt, there are very few residues, and they only gather in the damaged parts of the original brick structure. There is basically no change in the crystal structure of the original brick.
It can be seen from the chemical analysis results of the molten slag that the contents of SiO2 and Al2O3 are both above 4%. This slag has obvious erosion on the furnace lining high alumina brick. The results of petrographic analysis show the melting loss process of bricks. During the production process, the by-product Na2O and salts of the industrial production of soda sulfide interact with the main components of the original brick, such as SiO2 and Al2O3, to form nepheline that can be melted at about 1000 °C. Although it can promote the development and growth of crystals such as mullite and corundum, it is not enough to offset the side effects of nepheline. That is, melting loss of the furnace lining is caused. The above analysis shows that the main factors affecting the service life of original bricks are cracking and spalling, followed by erosion.
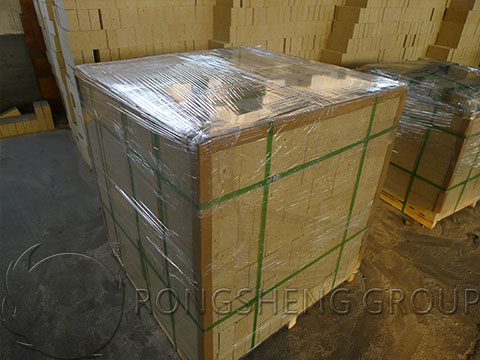
Solutions for anti-flaking refractory brick linings
Aiming at the damage mechanism of the grade I high-alumina bricks used in the soda sulfide industry, a kind of anti-stripping high-alumina bricks resistant to sodium sulfate erosion was studied. A new high-alumina product with high-alumina bauxite as the main raw material was tested. The thermal shock resistance of the new product was doubled compared with the original product, which greatly improved the thermal shock resistance of bricks. The anti-slag test also shows that because the apparent porosity of the new product is lower than that of the original brick, the erosion resistance of the brick body is improved. Through the refiring line test of the first-grade high-alumina bricks and new products, the results showed that the high-alumina bricks showed slight shrinkage. The new product maintains a slight expansion, which ensures the good integrity of the furnace body.
The damage of lining bricks in the soaking zone of alkali sulfide rotary furnace is mainly related to the erosion of rapid cooling and rapid heating and strong alkali slag. The new product produced with high alumina bauxite as the main raw material has low apparent porosity, good volume stability, slag corrosion resistance, and rapid cooling and rapid heating resistance. It solves the problems that the grade I high-alumina bricks are easy to peel off and not resistant to corrosion. To purchase high-quality anti-flaking high-alumina brick products, and get free solutions for the easy-flaking kiln lining and short furnace lining life, please contact Rongsheng refractory brick manufacturer. We can not only provide you with high-quality refractory lining products but also provide you with refractory lining solutions suitable for your production needs.