In recent years, with the widespread application of high-active lime in the metallurgical industry, many active lime kilns have been built, and advanced calcination equipment has put forward higher requirements for alkaline refractory materials. In the past, lime kilns mostly used magnesia-chrome bricks with good corrosion resistance and thermal shock resistance. In recent years, with the improvement of environmental protection awareness, chromium-free bricks have gradually replaced magnesia-chrome bricks. High-purity magnesia bricks have good corrosion resistance, but their thermal shock resistance is poor and cannot be used in locations with frequent temperature fluctuations. Although the thermal shock resistance of magnesia-aluminum spinel bricks is good. However, due to the high content of Al2O3, it is easy to react with the CaO in the lime and other impurities in the fuel such as CaO, SO3, ZnO, etc. to form low-melting substances, destroy the structure of the brick, and reduce the service life of the refractory material.
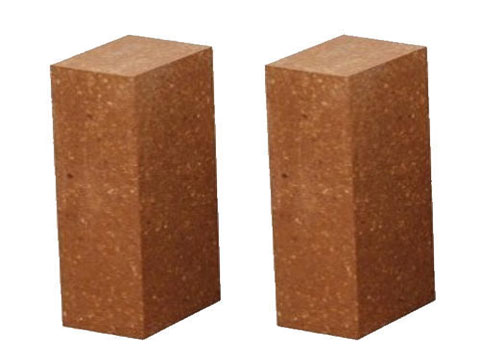
A steel plant has a 500t/d sleeve lime kiln. The main problem in the past is that the arch bridge has fallen bricks and has a short service life. Later, the arch bridge was changed to special magnesia brick. Until the recent major repairs, the arch bridge bricks have been used well, and the service life is 4 to 5 times longer. The arch bridge brick is a special magnesia refractory brick. In order to understand the damage of the refractory material in this part, the refractory material preparation of the sleeve lime kiln was optimized, and the residual bricks were analyzed.
Arch Bridge Brick Working Environment
Figure 1 is a schematic diagram of the work of the arch bridge.
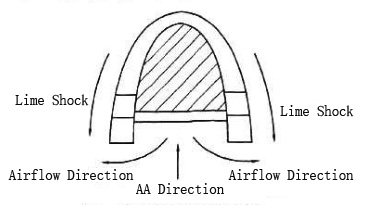
As shown in Figure 1, because the arch bridge bricks support the weight of the entire arch bridge, the refractory materials are required to have high strength. Since the chemical composition of lime decomposition and fuel combustion will corrode the refractory material, the refractory material in this part is also required to have good corrosion resistance. In addition, temperature fluctuations under high-temperature conditions have a great influence on refractory materials. Therefore, it is required that the refractory material should have good thermal shock resistance.
Damage of Special Magnesia Bricks for Arch Bridge Bricks
Special magnesia brick residue was retrieved from the lower arch bridge of a 500t/d sleeve kiln in a steel plant. The thick part of the residual brick is 78 mm, the thin part is 64 mm, and the length and width are 185 and 168 mm respectively.
Appearance Damage of Special Magnesia Bricks for Arch Bridge Bricks
Observed from the outside, a layer of magnesia fire clay is distributed on the surface of the remaining bricks. There are many cracks on the surface, especially the places close to the hot surface, where the cracks are more concentrated. The black surface is closer to the fire point of the combustion chamber, and the degree of erosion is greater. It can be inferred that during the use of the brick, the flame intensity of the burner leads to temperature changes, which promotes a large number of cracks in the brick. According to the surface color of the bricks and the surface cracks, the remaining bricks are divided into 4 layers, 1# 0~10 mm, 2# 10~50 mm, 3# 50~110 mm, 4# 110~168 mm.
Through analysis and comparison, it is found that the content of impurities such as SiO2, Al2O3, Fe2O3, CaO, etc. gradually increases from the cold surface to the working surface. Especially the increase of CaO content is more obvious, and the amount of ZrO2 is also increasing. With the penetration of impurities, the amount of low-melting-point phases is also increased. Because the low melting point phase and the main crystalline phase have different expansion rates. Cracks occur during use, resulting in a decrease in the compressive strength of the refractory material, a decrease in volume density, and an increase in porosity, which will eventually make the structure of the refractory material lose and peel off.
Microscopic Damage of Special Magnesia Bricks for Arch Bridge Bricks
Through the SEM photograph and energy spectrum analysis of special magnesia bricks, the following results are obtained.
The zirconia particles react with calcium oxide (contained in magnesia or brought in by lime), and the resulting calcium zirconate is wrapped on the surface of the zirconia particles. Part of the zirconia also diffuses into the magnesia and reacts with the calcium oxide in the magnesia to form calcium zirconate, which has a good bonding effect and improves the high-temperature performance of the magnesia brick. In addition, zirconia has a high toughness, which slows down the spalling of bricks.
Impurities mainly composed of calcium silicate enter the interior of special magnesia bricks and corrode them. A large number of low-melting silicate phases are formed in the matrix, filling the periclase crystals, reducing the degree of direct bonding between periclase, and reducing high-temperature performance. However, zirconia, which has been exposed to high temperatures for a long time, gradually diffuses into the matrix driven by the concentration gradient. It reacts with the calcium oxide in the raw material and the invading calcium oxide to form calcium zirconate, which is also filled between the substrates. Because calcium zirconate has good high-temperature performance, it helps to improve the high-temperature performance of magnesia bricks.
The Characteristics of Special Magnesia Bricks for Arch Bridge Bricks
The selection of special magnesia bricks containing zirconium can increase the service life of refractory materials and is more suitable for the special working environment of arch bridges than ordinary high-purity magnesia bricks. Zirconia-containing special magnesia bricks not only have good corrosion resistance and high-temperature strength but also because of the toughness of zirconia, special magnesia bricks have higher thermal shock resistance. The application of zirconia-containing special magnesia bricks to the simple lime kiln has good results.
To purchase high-quality magnesia bricks, please contact the refractory brick manufacturer.