Electric furnace smelting in non-ferrous metal smelting is to melt the material by passing electric energy through the electric arc generated by the electrode and the charge or directly through the high temperature generated by the molten slag as a resistance. And can control any temperature within the range of 1200~1600℃. The electric smelting furnace is mainly used to smelt materials containing a large amount of refractory ore. In areas with sufficient power resources, it is also used to smelt general ores. In our country, the smelting of copper, nickel, zinc, tin, etc., the heat preservation and dilution of molten slag, etc., all use electric furnaces.
Electric Furnace for Non-ferrous Smelting
The furnace type of the smelting electric furnace. The electric furnace for smelting copper sulfide concentrate and copper-nickel sulfide ore can have rectangular, oval, and circular shapes. In non-ferrous metal smelting, large-scale smelting electric furnaces generally use fixed rectangular closed electric furnaces. The rectangular electric furnace allows a larger hearth area and power, which is more suitable for the configuration of the transformer. And it is conducive to the separation of matte and slag, and the furnace body is convenient to build.
The size of the rectangular electric furnace is 10-35.66m long and 4.5-10.67m wide. The slag temperature is 1200~1380℃. The final product of smelting is copper-nickel matte (it is an alloy of nickel, copper, and iron) or copper matte. The temperature is about 1050~1250°C, and the production is continuous.
Advantages and Disadvantages of Electric Furnaces for Non-ferrous Smelting
The main advantage of electric furnace smelting is that the bath temperature is easy to adjust and can reach a higher temperature. The theoretical amount of smoke is low. The thermal efficiency is high, up to 60% to 80%. The amount of slag is small and the total recovery rate of smelted metal is high.
The main disadvantage of electric furnace smelting is that it consumes a lot of electricity and the processing cost is higher than that of reverberatory furnace smelting. The moisture content of the charge is generally not more than 3%. Infrastructure investment is slightly higher.
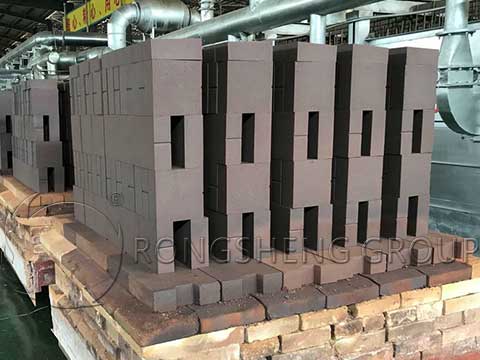
Magnesia Chrome Refractory Bricks for Non-ferrous Metal Industry
The refractory bricks used in the non-ferrous metal industry mainly include magnesia-chrome refractory bricks, corundum refractory bricks, and high alumina refractory bricks. Among them, magnesia-chrome refractory bricks are widely used in copper smelting, nickel smelting, and lead smelting industries. The characteristics of the three metal smelting are that the flue gas contains a large amount of SO2 gas. The melt not only contains oxides, metals, but also a lot of sulfides. The melting temperature of the melt is relatively low, but the fluidity of the melt is better. The slag is FeO-SiO2 slag, and the amount of slag is very large. The temperature in the furnace fluctuates greatly, and the melt erodes the refractory bricks seriously. Magnesium chromium refractories have a strong resistance to the corrosion of iron-silicon slag and the corrosion of SO2. It also has good resistance to melt erosion and is currently the most widely used refractory brick for smelting three types of metals.
Magnesia chrome refractory bricks are refractory brick products composed of magnesium oxide (MgO) and chromium trioxide (Cr2O3) as the main components, and periclase and magnesia chromium spinel as the main minerals. Magnesia chrome refractory bricks have the advantages of high refractoriness, high-temperature strength, strong resistance to alkaline slag erosion, and strong thermal shock resistance. Generally used in non-ferrous metal smelting furnaces.
There are many types and varieties of magnesia-chrome refractory bricks. According to its combination method, it can be divided into ordinary magnesia chrome bricks, directly combined magnesia chrome bricks, combined magnesia chrome bricks, semi-recombined magnesia chrome bricks, and so on.
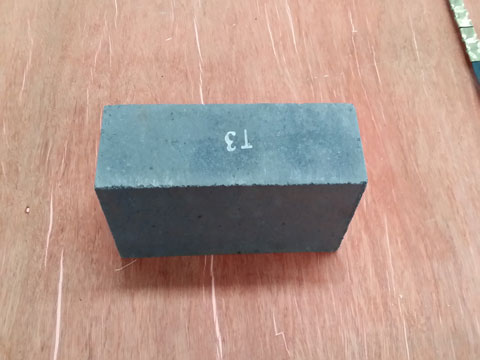
Rongsheng Refractory Bricks Manufacturer
Rongsheng is an experienced refractory brick manufacturer. Rongsheng’s refractory products have been recognized by customers in more than 60 countries and regions all over the world. For example, Thailand, UAE, Turkey, Kuwait, South Africa, Malaysia, Vietnam, Netherlands, Philippines, Singapore, Egypt, Russia, etc. Rongsheng’s magnesia chrome brick series, magnesia alumina brick series, magnesia brick series, magnesia carbon brick series, etc., all have high product quality. For more information about refractory materials for non-ferrous smelting, please contact us. We will provide you with services according to your specific needs.