Directly bonded magnesia-chromium bricks are MgO-Cr2O3 refractory products made from high-purity magnesia and chromium concentrate with low impurity content, ground together and fired at high temperature (above 1700°C). Due to the high direct bonding rate of high-temperature mineral phases, it has strong slag resistance, good high-temperature strength, and excellent thermal shock resistance. Rebonded magnesia-chromium bricks are MgO-Cr2O3 refractory products that use fused magnesia-chromium sand as raw material, are formed by high pressure, and are fired at a high temperature of 1800℃. Due to the higher direct bonding rate, low apparent porosity, and high volume density. Rebonded magnesia chromium bricks have higher high-temperature strength and slag erosion resistance than directly bonded magnesia chromium bricks. However, the thermal shock resistance of combined magnesia-chromium bricks is poor. The refining ladle slag line is made of MgO-Cr2O3 refractory material.
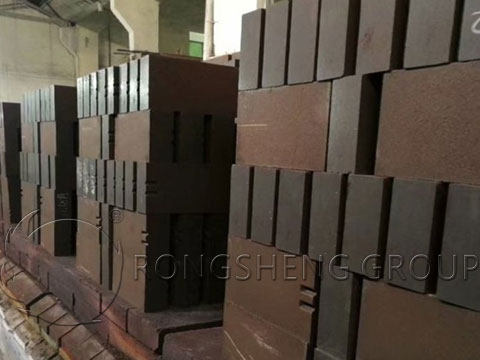
Damage to the MgO-Cr2O3 Refractory Material Used in the Refining Ladle Slag Line
The main characteristics of damage to the MgO-Cr2O3 refractory material used in the refining ladle slag line are Chemical erosion of slag, structural spalling caused by slag penetration, and erosion of high-temperature molten steel slag. MgO-Cr2O3 refractory materials have certain corrosion resistance for CaO-SiO2 series slag with low CaO/SiO2 ratio (ratio less than 2). However, for CaO-SiO2-based slag with a high CaO/SiO2 ratio at high temperatures, especially when the Fe2O3 content is high, the eutectic temperature drops rapidly and the corrosion resistance is very poor.
Improve the Durability of MgO-Cr2O3 Bricks Used in the Refining Ladle Slag Line
Improve the durability of MgO-Cr2O3 bricks used in the refining ladle slag line, that is, improve their thermal shock resistance, slag resistance, and erosion resistance. These are related to the properties, production amount, size and distribution of secondary spinel in the brick. Most researchers at home and abroad have confirmed that the formation of secondary spinel in bricks is related to brick-making raw materials, admixtures and brick-making processes.
- (1) The number of secondary spinels directly bonded to magnesia-chromium bricks increases as the proportion of chromium ore (or Cr2O3 content) in the ingredients increases. The number of secondary spinels in rebonded/semi-rebonded magnesia chromium bricks increases with the increase in the total amount of fused magnesia chromium sand R2O3 (Cr2O3, Al2O3 and Fe2O3), the decrease in the Fe2O3 content in R2O3, and the increase in the Al2O3 content. increase.
- (2) When the specific surface area of the fine powder in the recombination magnesia-chromium brick ingredients reaches 5~6m2/g, the amount of secondary spinel will be the largest.
- (3) When the firing temperature of directly bonded magnesia-chromium bricks is above 1700°C, secondary spinel with self-crystallizing characteristics can be observed. Both the size and number of secondary spinels increase with further increase in firing temperature. When the sintering temperature is increased to 1800°C, the amount of secondary spinel generated reaches 6% (volume fraction).
A large number of research results confirm:
- (1) As the amount and size of secondary spinel in bricks increases, for example, the volume fraction of secondary spinel in directly bonded magnesia chrome bricks reaches 6% and the volume of secondary spinel in rebonded magnesia chrome bricks When the fraction reaches 8%, its high temperature flexural strength reaches its highest value. High-temperature flexural strength is an important indicator for measuring the high-temperature wear resistance of MgO-Cr2O3 bricks, and high-temperature wear resistance can reflect an important indicator of resistance to high-temperature molten steel and molten slag erosion. Therefore, the resistance to high-temperature molten steel and slag erosion of direct bonded and rebonded (semi-rebonded) magnesia-chromium bricks that generate a large amount of secondary spinel will inevitably be improved.
- (2) There are a large number of secondary spinels in rebonded magnesia-chromium bricks that prevent slag erosion, so they have the highest slag resistance.
- (3) Increase the fineness of the fine powder in the ingredients. For example, when the specific surface area of the fine powder reaches 5m2/g, the thermal shock resistance of combined magnesia-chrome bricks will be significantly improved. In short, by using brick-making processes such as optimized raw materials and ultra-high-temperature firing to increase the amount of secondary spinel in the bricks, direct-bonded and re-bonded (semi-re-bonded) magnesium-chromium refining ladle slag lines with high comprehensive performance can be produced brick.
Some countries have used alumina to replace chromite to produce MgO-MgO·Al2O3 bricks (Al2O330%~40%, MgO60%~70%) with good thermal shock stability. However, bricks containing chromium spinel have strong slag resistance because the solubility of chromium spinel in silicate solution is lower than that of aluminum spinel.
Direct bonding and rebonding (semi-rebonded) magnesia-chromium bricks occupy the refining ladle slag line for the longest time. Even now, it is still an important refractory material for use in the refining ladle slag line. However, the production complexity of these magnesia-chromium bricks, price issues, and the harm of hexavalent chromium to human health have forced people to develop their substitutes.