Among the nitride-bonded refractory materials, one type of material that is widely used is Si3N4 bonded SiC material. Like silicon oxynitride bonded silicon carbide products and Sialon bonded silicon carbide products, this material is also obtained by reaction sintering in a nitriding furnace. Both silicon nitride and silicon carbide are covalently bonded crystals, sintering is difficult, and a certain way is needed to combine the two. Next, let’s understand the preparation method of silicon nitride bonded silicon carbide brick.
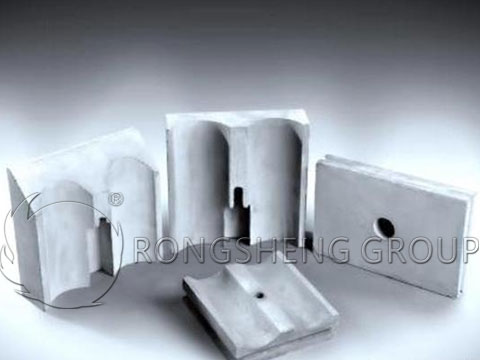
Generally, other methods for preparing silicon nitride bonded silicon carbide materials include reactive sintering, carbothermic reduction of silicon dioxide, hot pressing sintering, atmospheric sintering, self-propagating high-temperature synthesis, and so on. By understanding these preparation methods, it may be helpful to understand the properties of silicon nitride bonded silicon carbide bricks.
(1) Reaction sintering method
The reaction sintering method is also called the nitriding sintering method. The main chemical reactions are as follows.
3Si+2N2→Si3N4
The product after nitriding is a mixture of α-Si3N4 and β-Si3N4. This method is the most widely used production method in the industry. Using this method, adding SiC to the raw material can be combined with Si3N4. Due to the presence of trace O2 in the atmosphere, a small amount of Si2N2O is often present in the product. At the same time, the degree of nitridation reaction is also limited, so some unreacted free Si may remain inside the product. Compared with oxide-bonded silicon carbide products, silicon nitride-bonded silicon carbide products show more excellent high-temperature performance and slag corrosion resistance.
There are two main mechanisms for the formation of Si3N4. One is indirect nitriding. Due to the presence of a trace amount of O2 in the atmosphere, O2 reacts with Si on the surface to form SiO(g), and SiO(g) reacts with nitrogen in the atmosphere to form Si3N4 in the gas phase. The Si3N4 produced by this gas-gas reaction is generally fibrous α-Si3N4. The second is the direct nitriding. Si reacts with N2 to directly generate Si3N4, where the state of Si can be solid or liquid. The Si3N4 produced by this gas-solid reaction or gas-liquid reaction is generally β-Si3N4.
The advantage of the reaction sintering method is that the expansion of the reaction is mainly the expansion inside the green body. The increased volume can effectively fill the voids in part of the blank, and increase the densification of the product. At the same time, the apparent size of the product is basically unchanged, which is suitable for manufacturing products with complex shapes. The disadvantage of the reaction sintering method is that the degree of nitriding of the product is limited. This is because N2 gradually penetrates from the outside to the inside. After external nitriding, it becomes more difficult for N2 to penetrate into the inside, and the inside tends to be less nitridated. Some studies have found that after the sample is fired in a nitrogen atmosphere, the nitrogen content of the surface and the center area is significantly different. The nitrogen content on the surface of the sample is relatively high, and it is mainly fibrous Si3N4. The nitrogen content in the central area is relatively low, and the Si3N4 is columnar. This result may be caused by different generation mechanisms outside and inside the sample. Therefore, the components of silicon nitride bonded silicon carbide products are unevenly distributed.
(2) Carbothermal reduction of silica method
The raw materials used in the carbothermic reduction silicon dioxide method are SiO2 and SiC, and the atmosphere is a nitrogen atmosphere. In this atmosphere, carbon is used to reduce silicon dioxide to silicon. Si reacts with nitrogen in the atmosphere to form silicon nitride. The possible reactions are as follows.
3SiO2(s)+6C(s)+2N2→Si3N4(s)+6CO(g)
△G1-4=1317.04-750.57×10-3T
SiO2(s)+3C(s)→SiC(s)+2CO(g)
△G1-5=614.04-376.18×10-3T
2SiO2(s)+3C(s)+N2(g)→Si2N2O(s)+3CO(g)
△G1-6=-305.32+189.4×10-3T
According to the variation of Gibbs free energy △G of each reaction with temperature, it is found that the theoretical products at different temperatures are different. From the △G of the reaction, it can be calculated that when the temperature is higher than 1755K and the nitrogen flow is higher, the product is Si3N4. When the temperature is higher than 1633K and the nitrogen flow is low, SiC is formed. When the temperature is lower than 1600K and the nitrogen flow is low, Si2N2O is formed. Thus, silicon nitride bonded silicon carbide products, self-assembled silicon carbide products, and silicon oxynitride bonded silicon carbide products can be obtained respectively. Therefore, by controlling the sintering temperature and nitrogen flow rate, different products can be obtained and the reaction process can be controlled.
(3) Si(NH)2 thermal decomposition method
The Si(NH)2 thermal decomposition method decomposes Si(NH)2 into Si3N4 at a temperature of 900 to 1200°C. There are two main methods for preparing precursor Si(NH)2. One is to use SiH4 and NH3 to obtain Si(NH)2 through gas-phase reaction. Another method is to react SiCl4 dissolved in an organic solvent with liquid nitrogen at a lower temperature to produce Si(NH)2, and then the obtained Si(NH)2 is treated with ammonia water. The difference between the two methods is that the former uses a gas phase reaction to generate Si(NH)2 in a tube furnace. Although this method has higher requirements for others, the reaction process is controllable. The latter is obtained by reacting in an organic solvent at low temperature to obtain Si(NH)2, and then washing, the process operation is relatively simple.
Si3N4 obtained by decomposition is usually amorphous. Amorphous Si3N4 is heated in a protective flowing nitrogen atmosphere (1400℃~1600℃) to crystallize and obtain α-Si3N4 whiskers. As the temperature continues to rise, α-Si3N4 gradually transforms to β-Si3N4, and the content of β-Si3N4 increases. The main reactions are as follows.
SiCl4+6NH3→Si(NH)2+4NH4CI
3Si(NH)2→Si3N4+3H2+N2
Si3N4 (atmosphere) →Si3N4 (whiskers)
(4) Self-propagating high-temperature synthesis method
The self-propagating high-temperature synthesis method is also called the combustion synthesis method. It uses a large amount of heat released when the material is burned to cause the Si, C, and N materials in the compact to undergo a violent chemical reaction, and automatically spread to form a ceramic compound.
Combustion synthesis can be used under different pressure atmospheres, such as in air, high-pressure vessels, or vacuum environments. The synthesis of silicon carbide ceramics combined with silicon nitride must be carried out in a pressure vessel filled with nitrogen. The advantage of the self-propagating high-temperature synthesis method is that the energy consumption of the reaction is relatively small, and the chemical energy released by the combustion process is mainly used without external heating. At the same time, the equipment required for the reaction is relatively simple, the reaction speed is fast, and the purity of the prepared product is high.
However, this method also has shortcomings. The fast reaction speed causes the temperature to change too fast, and it is impossible to implement more precise control of the reaction process. The final product tends to have low density and low strength.