Refractory brick lining plays a very important role in the blast furnace. However, in the production process, the refractory brick lining of the furnace wall is gradually corroded due to various effects. To extend the service life of the blast furnace, it is necessary to purchase refractory brick linings reasonably.
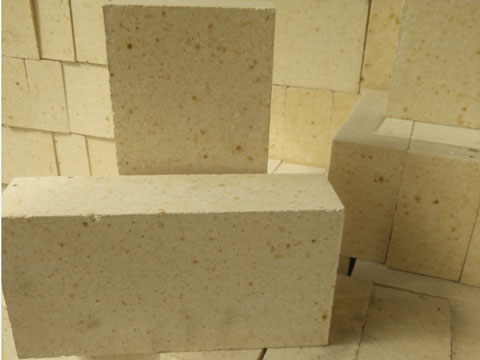
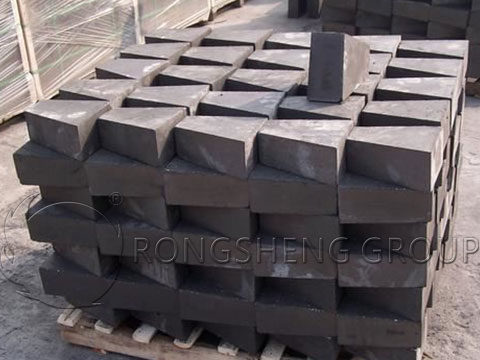
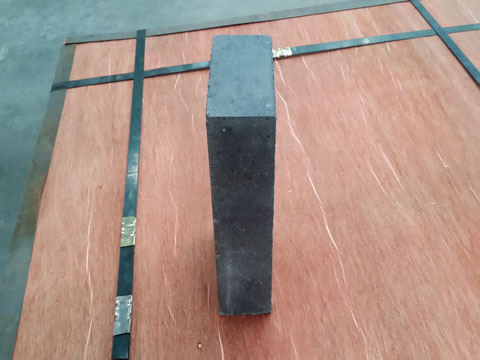
How to reasonably choose the refractory bricks used in different parts of the blast furnace? There are the following references.
- Furnace throat: withstand the impact and wear of the incoming charge. Generally, steel bricks or water-cooled steel bricks are used.
- The upper part of the furnace: This part is seriously corroded by alkali metal and zinc vapor. In addition to the erosion and wear of the falling charge and the rising gas flow, dense clay bricks with good chemical resistance and wear resistance, three-grade high alumina bricks or phosphoric acid impregnated clay bricks should be selected, that is, phosphorous-impregnated clay bricks.
- The middle and lower part of the furnace body and the furnace waist: this part is severely corroded by the first slag. The brick lining should be made of refractory materials resistant to thermal shock, initial slag erosion, and erosion resistance. Large-scale blast furnaces at home and abroad choose silicon carbide bricks with good performance to achieve a life of more than 8 years. However, aluminum-carbon bricks can also be used in blast furnaces below 1000m3. Because aluminum carbon bricks are cheap, the cost will be reduced accordingly.
- Hearth: The hearth is scoured by high-temperature gas and slag iron, and the heat flow is strong. Generally, high-alumina bricks and aluminum-carbon bricks with high refractoriness, high load softening temperature, and large volume density are used.
- Hearth tuyere: This part is the area of oxidation reaction, the temperature reaches 1900-2400℃. The brick lining is subjected to thermal stress caused by high temperature, as well as high-temperature gas erosion, slag iron erosion, alkali metal erosion, and cyclic movement coke erosion. Modern blast furnaces use combined bricks to build the hearth tuyere, made of high alumina bricks, corundum mullite bricks, silicon carbide bricks combined with brown corundum and silicon nitride, and hot-pressed carbon blocks are also used.
- The lower part of the hearth and the bottom: This is the place where the lining of the entire blast furnace is seriously corroded, and the degree of corrosion determines the life of the blast furnace. Large-scale blast furnaces use ceramic cups, staggered bites, etc. There are also high-quality brown corundum bricks, gray corundum bricks, carbonaceous microporous bricks, and hot-pressed bricks. However, the penetration and dissolution of molten iron on carbon bricks, the chemical attack of alkali metals on carbon bricks, and the destruction of carbon bricks by thermal stress are still important factors that threaten the life of the furnace bottom and hearth.
In short, the production conditions of each part of the blast furnace are different. Therefore, choose different refractory bricks for different parts. In order to avoid unnecessary trouble caused by refractory brick lining not meeting the requirements.
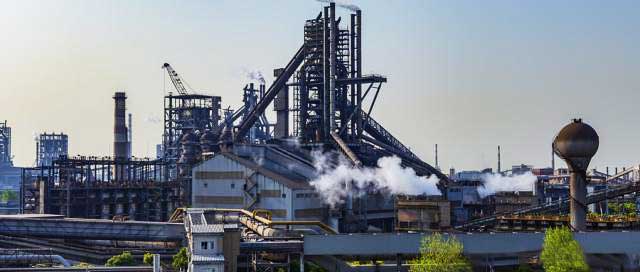
Analysis of the Causes of the Damage of Refractory Brick Lining of Blast Furnace
The refractory brick lining of the blast furnace is enclosed to form a smelting space, so it is the working surface during production operations and is damaged by many factors. In summary, they are divided into two categories. One type is determined by the characteristics of the blast furnace smelting process and is a continuous effect; the other type is structural production factors. The former is the first and the latter is the second. Designers and producers should try to overcome the effects of the second category of factors and reduce the effects of the first category of factors.
Factors belonging to the first category include temperature effects, mechanical erosion, and abrasion, the chemical effects of alkali metals and other elements brought in by the charge with the brick lining, as well as carbon evolution reactions and zinc deposition. Factors belonging to the second category include the unreasonable design of furnace wall structure, poor quality of refractory materials used, poor quality of furnace construction, and improper operation, such as excessive development of edge airflow, nodules, and edge pipes.
Generally speaking, under the action of the above factors, the normal brick lining corrodes faster at the beginning of the furnace. It can reach 20-40mm/month on a thick-walled blast furnace. After 2 to 4 months, it gradually slows down. Under the action of cooling, the hot working face begins to form a slag, and the erosion rate drops to 5-20mm/month. After about 3 years, the slag skin becomes the main furnace lining, forming an operating furnace type. On the thin-walled blast furnace, the brick lining is 150mm thick, or the bricks are not laid but only unshaped refractories are sprayed. Therefore, the slag skin was used as the lining of the furnace earlier.
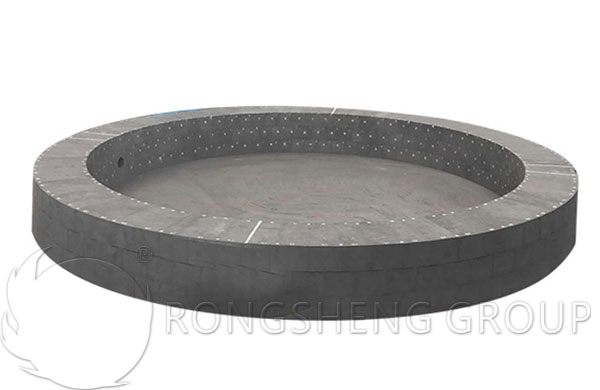
Rongsheng Refractory Brick Manufacturer
Rongsheng refractory brick manufacturer is a refractory material manufacturer with rich experience in production and sales. Rongsheng’s refractory products have been sold to more than 60 countries around the world, for example, Russia, South Africa, Kazakhstan, Philippines, Chile, Malaysia, Uzbekistan, Indonesia, Vietnam, Kuwait, Turkey, Zambia, Peru, Mexico, Qatar, etc. Rongsheng’s hot-selling refractory brick products mainly include high alumina bricks, wear-resistant bricks, corundum bricks, insulation bricks, phosphate bricks, magnesia bricks, magnesia chrome bricks, etc. If you need to buy refractory brick products, please leave your specific requirements on our website, for example, your working conditions, or the physical and chemical indicators of refractory bricks you need. We will provide you with refractory products that best suit your production needs according to your specific needs, and save production costs to the greatest extent.