Low porosity fire clay bricks are kinds of fire clay bricks. Fire clay bricks use refractory clay or flint clay clinker as the main raw material. Its alumina content is 30% ~ 46%, and its refractoriness is 1580 ~ 1770C. It is a weak acid refractory material, which with good thermal shock resistance, corrosion resistance to acid slag, and have a wide application. Fire clay bricks made of refractory clay as the main raw material are called ordinary fire clay bricks. Which made of Flint Clay clinker as the main raw material and showing a porosity of 17% are called low-porosity fire clay bricks.
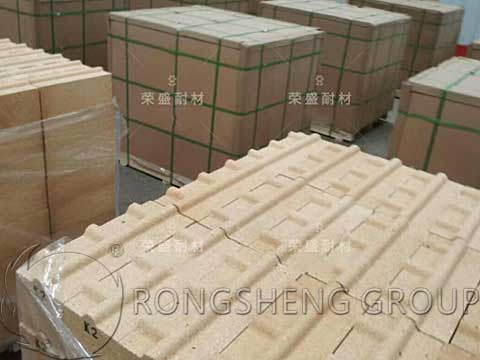
Low Porosity Fire Clay Brick
Alumina Content: 30% ~ 46%
Refractoriness: 1580 ~ 1770C
Features: Low apparent porosity, strong resistance to penetration, and erosion.
Uses: Mainly used in steel, glass, chemical industry, and other industries for the refractory ling of thermal furnaces, such as blast furnace, hot blast stove, glass kiln, roaster, etc.
Classification of Fire Clay Bricks
According to the uses of fire clay bricks, they are mainly divided into fire clay bricks for blast furnaces, fire clay bricks for hot blast stoves, large fire clay bricks for glass kilns, etc.
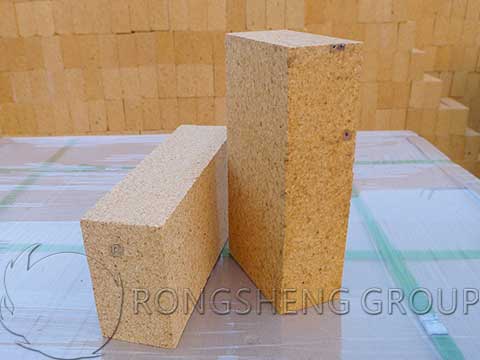
Clay Refractory Brick for Blast Furnace
Clay refractory bricks for blast furnaces are made of refractory clay as raw materials and used to build the refractory lining of blast furnaces. Clay refractory bricks for smaller blast furnaces refractory lining are mainly for the parts like the throat, shaft, hearth, bottom. For the large blast furnace, mainly used as the refractory lining for the part of furnaces body.
Clay refractory bricks for blast furnace requires:
- High refractory strength at room temperature, able to resist long-term wear and tear of furnace charge;
- Under long-term operation at high temperature, the volume shrinkage is small, which is conducive to maintaining the integrity of the lining;
- Low apparent porosity and low Fe2O3 content to reduce carbon deposition in the pores. At the same time, avoid refractory bricks being damaged due to expansion and looseness during use;
- Generating less low-melting products;
- Clay refractory bricks for blast furnace have better performance than ordinary fire clay bricks.
Clay refractory brick for hot blast stove
Clay refractory bricks for hot blast stoves are made of refractory clay as raw materials and used to build refractory lining for blast furnace hot blast stoves. Clay refractory bricks for hot blast stoves are used for hot blast stoves, regenerators, and partition walls. Fire clay bricks for hot blast stoves require good thermal shock resistance, high load softening temperature, and small creep.
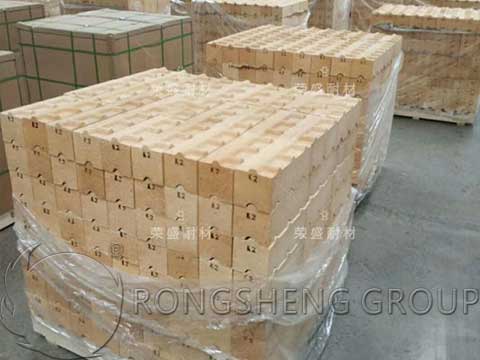
Low Porosity Fire Clay Bricks
The main raw materials of low porosity fire clay bricks are dead burned clay material, dead burned combined clay, and Henan white coke gemstone. They are broken into 5-3mm, 3-1mm, and ≤ 0.088mm respectively. Then mix with other 6 kinds of additives to make 6 kinds of mud materials and mix them, and then add binder and fine powder. After being mixed evenly, on a 260T brick press, it is pressed with standard bricks models to make bricks. Next, it is dried in a drying kiln at 110 ° C for 16h, and when the moisture of the brick is less than 1%, it is loaded into the tunnel kiln for firing. Finally, reduce the temperature of the bricks to the room temperature.
There are many varieties of low porosity fire clay bricks, RS refractory bricks manufacturer can produce kinds of low porosity fire clay bricks specifications, there are mainly “three-low” fire clay bricks (DDD), low porosity fire clay bricks (DN-12, DN-15), and ordinary fire clay bricks (N-1, N-2a). They are widely used in glass furnaces, blast furnaces, hot blast stoves furnaces, cement kiln furnaces, chemical kilns, and other thermal equipment. According to their working conditions, the roaster can use clay refractory bricks with low creep and low porosity. The Rongsheng refractory manufacturer has customized low-creep and low-porosity fire clay bricks for the roasters of Egyptian customers and delivered them smoothly.
The practice has proved that,
- It is feasible to use clay clinker with low water absorption as the main raw material to produce low porosity fire clay bricks.
- Compared with ordinary fire clay bricks, properly increasing the firing temperature can reduce the porosity of the products and increase the bulk density.
- The use of additives can make the product form a large number of micropores. Therefore, thermal shock stability is improved when the pores of the product are low.
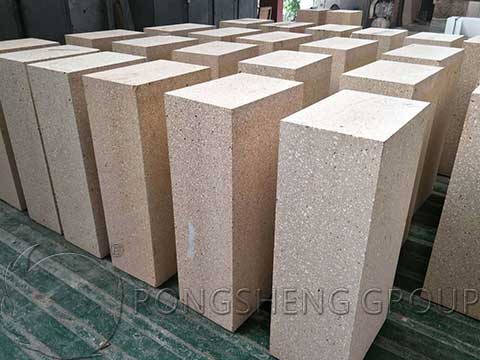
Low Porosity Fire Clay Bricks for Glass Kiln
Generally, large fire clay bricks for glass kilns are clay refractory bricks with a unit weight of not less than 50 kg used for building glass kilns. China Metallurgical Standard (YB / T 5108-1993) stipulates the physical and chemical indicators, size tolerances, and appearance of large clay refractory bricks for glass kilns.
Low-porosity fire clay bricks for glass kilns are mainly used in the regenerators of glass kilns. It is mainly made of high-alumina bauxite and Flint Clay, added with sillimanite and andalusite in proportion and added with a binding agent, binder, kneaded, shaped, dried and then kiln fired. Its porosity is generally below 17%.
Characteristics of low-porosity fire clay brick for glass kiln
- Low porosity and strong density.
- Good penetration resistance and good erosion resistance.
- High-temperature strength and long service life.
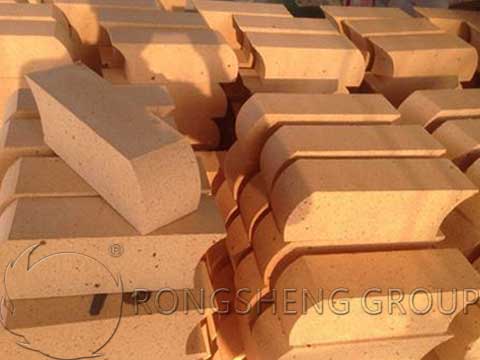
Low Porosity Fire Clay Brick for Hot-metal Bottle
With the development of smelting technology, the requirements for refractory materials for Hot-metal Tanks are getting higher and higher. Many Hot-metal Tanks use common fire clay bricks, but their furnace age is not long. For example, when a 75t Hot-metal Tank in a steel plant has a furnace age of about 400 times, there along with a phenomenon that the brick flakes. This has a certain impact on the quality of the finished products. And frequently Hot-metal Tank’s removal is time-consuming and laborious. To this end, refractory manufacturers have developed low-porosity clay refractory bricks to meet production needs.
Applying low-porosity clay refractory bricks to Hot-metal Tanks can increase the service life by more than twice compared to ordinary Hot-metal Tanks’ fire clay bricks lining. If it is widely promoted to steel mills, the economic benefits will be very significant.
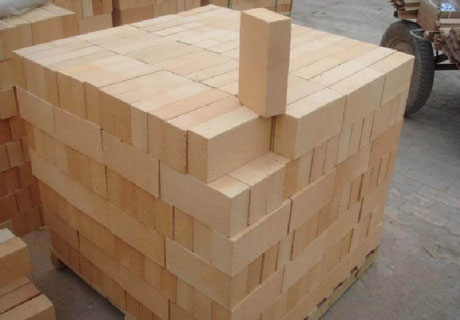
Advantages Summary of Low Porosity Clay Refractory Bricks
Choosing raw materials with high density and low water absorption rate through reasonable gradation is the key to making low-pore bricks. When firing low-porosity fire clay bricks, the maximum temperature is generally controlled at 1350 ~ 1380 ° C. Properly increase the firing temperature of the low-porosity brick (1420 ° C), the shrinkage of the product increases slightly so that the volume density of the product slightly increases, and the low porosity can be reduced.
Low-porosity clay refractory bricks, after trial by many companies, have not been cracked by the reaction. At the same time, low-porosity fire clay bricks also have the advantages of corrosion resistance, high-temperature resistance, good thermal stability, and regular shape. The service life of the lining used to build kilns is 3 to 4 times that of ordinary fire clay bricks.