Generally speaking, the main purpose of using refractory bricks as refractory lining in kilns is to satisfy the more efficient production of kilns. The refractory bricks used in furnaces cannot become an obstacle to the production process and delay production. Therefore, refractory bricks lining for kilns should be based on the longevity and efficient production of kilns. Refractory bricks are inorganic non-metallic materials with refractoriness not less than 1580℃. Since refractory bricks are mainly used as structural materials for high-temperature kilns and other thermal equipment as well as industrial high-temperature containers and components, it can withstand various physical and chemical changes and mechanical effects in it.
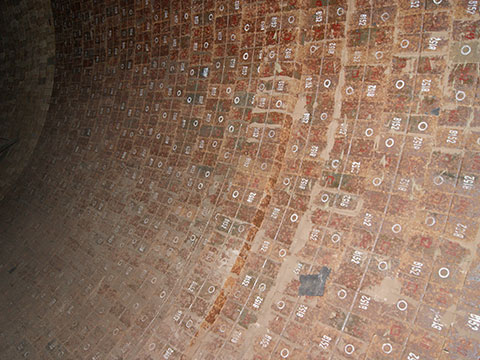
Selection of Refractory Bricks Used in Industrial Kilns
There are many types of industrial kilns, and the structure is relatively complex. The selection and application of refractory bricks for industrial kilns are often very different. No matter what kind of refractory bricks are used in industrial kilns, they must meet the following requirements:
- First, it can withstand high temperatures without softening or melting.
- Secondly, it must bear the high-temperature load, and it must not lose the internal structure strength of the refractory brick, and it will not deform. It has good high-temperature volume stability, a small linear change on reheating, and can resist high-temperature gas erosion and slag erosion.
- Finally, the size specifications of the refractory bricks are regular, and the specific location of the kiln furnace needs to be determined by the actual situation.
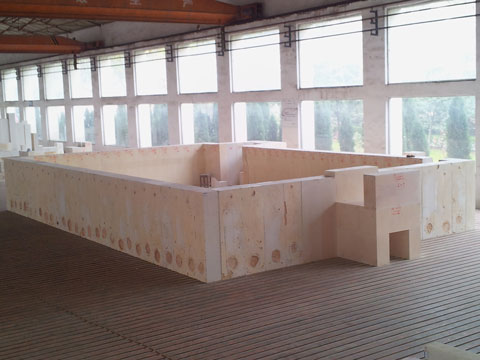
Refractories for Different Kilns
- Refractory materials for glass kilns: clay bricks, silica bricks, zircon bricks, fused zirconium corundum bricks, thermal insulation materials, etc.;
- Refractory materials for cement kilns: alkaline refractory materials, aluminum-silicon refractory materials, thermal insulation refractory materials, castables;
- Castables for ceramic kilns: clay refractory bricks, high alumina bricks, silica bricks, magnesia bricks, corundum bricks;
- Refractory materials for coke oven: clay brick, silicon brick, etc.
Refractory Bricks for Furnace Hearth
The furnace chamber of the kiln is a closed combustion chamber made of refractory bricks and isolates the flame burning in the kiln from the outside world. Refractory bricks for kiln hearths must have fairly high heat resistance and thermal insulation. Therefore, refractory bricks for kiln furnaces are mostly high alumina bricks. The overall structure of the furnace and the required refractories are as follows:
Industrial boilers with kiln furnace capacity of less than 40t/h are mainly heavy-duty structures. The furnace is built directly on the basis of the boiler. The hearth is composed of two layers, inside and outside. The inner lining is usually made of t-3 standard brick high-alumina refractory brick. The outer layer is a thermal insulation layer, built with thermal insulation bricks. The bricks at the corners of the inner and outer layers need to bite each other to form a whole.
The furnace roof structure is mostly arched or hanging. The arched furnace roof mostly uses arch foot refractory bricks and thermal insulation bricks. Hanging bricks and insulating bricks are mostly used for hanging furnace tops.
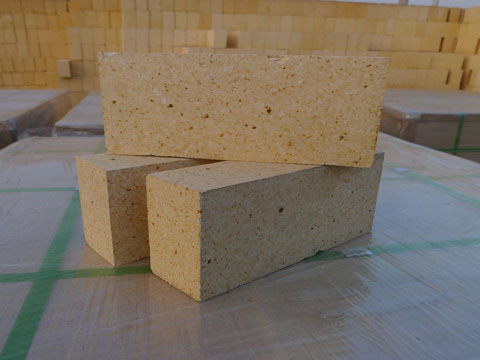
Principles to be Followed When Choosing Refractory Bricks for Industrial Kilns:
- To understand the characteristics of industrial kilns. Refractory bricks are selected according to the design of the kiln, the working environment, and the working conditions of each part. It is necessary to analyze the damage mechanism of refractory bricks used in industrial kilns and select refractory bricks in a targeted manner.
- To understand the nature of refractory bricks. Familiar with the own properties and characteristics of refractory bricks. For example, the chemical mineral composition, physical properties and working performance of the refractory raw materials used in refractory bricks, in order to give full play to the advantages of refractory raw materials selected for refractory bricks. The reasonable configuration of the refractory raw material formula can make the refractory bricks have better performance.
- Reasonably control the overall use of the kiln. The use environment and working conditions of different parts of the kiln are different, and the selected refractory bricks should also be reasonably matched. It is necessary to confirm that there will be no chemical reaction and melting damage between refractory bricks of different materials under a high-temperature environment, but also to ensure the balanced loss of various parts of the lining of the kiln. Reasonably control the overall use of the lining of the refractory bricks of the kiln to ensure the overall service life of the furnace and avoid different repairs of different parts of the kiln.
- Refractory bricks for industrial kilns must not only meet the needs of users but also need to consider the rationality of economic benefits. If clay bricks can meet the needs of industrial kilns, there is no need to choose high-alumina bricks, so the selection of refractory bricks for industrial kilns needs comprehensive consideration.
The quality of refractory brick depends on its nature, it is the standard for evaluating products. The correct and reasonable selection of refractory kiln bricks is also based on their properties as an important basis. Rongsheng Refractory kiln bricks manufacturer provides all kinds of refractory kiln bricks, and our refractory materials have been delivered to more than 60 countries and areas. If you are in need of refractory bricks used in furnaces, please contact us.