The color of silica molybdenum bricks has a certain relationship with the firing temperature, but the most important thing is the firing atmosphere. During the firing process, the reducing atmosphere is most suitable for the firing of SiC Mullite Bricks.
If the brick is exposed to an oxidizing atmosphere at the firing temperature, the brick will oxidize, no silicon carbide will be reflected on the surface, and the strength will also decrease. Silica molybdenum bricks are characterized by wear resistance and good seismic stability and are mostly used in the transition zone before and after cement rotary kilns.
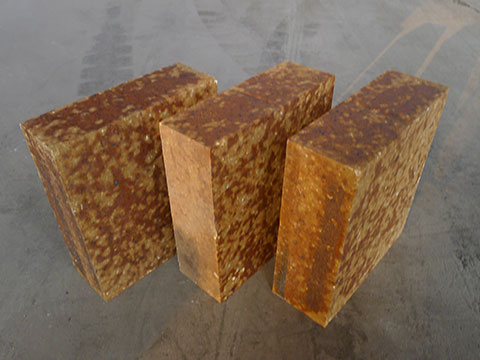
SiC Mullite Bricks have a dense structure, stable mullite, and SiC crystals, and can prevent erosion by gases and molten materials. However, silicon carbide has high thermal conductivity, a small thermal expansion coefficient, and good thermal and shock resistance, so the bricks are not easy to break and peel off. The performance of silicon molybdenum bricks used in cement rotary kilns is relatively better than anti-flaking high-alumina bricks and phosphate high-alumina bricks with better wear resistance.
But in many cases, the firing atmosphere of silica molybdenum bricks is different from that of high alumina bricks or magnesia bricks. Because carbon silicide is suitable for firing in a reducing atmosphere, silicon carbide is oxidized in an oxidizing atmosphere, and the use effect will be greatly reduced. Some manufacturers will add a certain proportion of metal aluminum powder to adjust the oxidation of silicon carbide in the production process. However, during the firing process, the firing atmosphere must be well controlled. Silicon molybdenum bricks fired in a reducing atmosphere have an obvious appearance reaction due to the action of silicon carbide. And when used as a lining in a cement rotary kiln, it can prevent the melt from forming.
It should be noted that the amount of silicon carbide added also affects the color reflection of SiC Mullite Bricks. The amount of silicon carbide added is small, and the reaction on the brick surface is relatively small. Below 8%, there will be little reaction on the surface of the brick, with only a layer of slight discoloration and no surface glaze appearing. If the temperature is too high, the surface reaction will not change much. But the most important thing is that the firing atmosphere has the greatest impact on the color of silica molybdenum bricks. Of course, the performance will also be reduced during use.
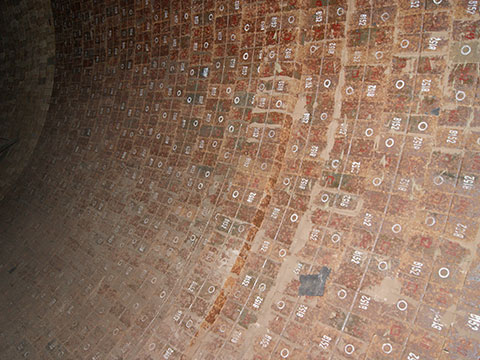
Resistance of SiC Mullite Bricks to Alkali Erosion in Cement Kilns
SiC Mullite Brick 1680 and SiC Mullite Brick 1550 performed well in the alkali erosion test, with no cracks. The change curve of K element content is consistent and concentrated in the brick surface area. The silicon dioxide generated by the oxidation of silicon carbide at high temperature reacts with potassium to form a glass phase, forming a dense layer to inhibit the erosion and penetration of K element. The alumina in the silica molybdenum brick matrix is easily eroded by alkali, and the liquid phase fills the pores of the SiC Mullite Brick to form a dense layer. After alkali erosion, the K element is mainly concentrated in the erosion surface area. The alkali erosion resistance of SiC Mullite Bricks is related to the introduction of silicon carbide and the apparent porosity of SiC Mullite Bricks.
Randomly select two pieces from the aluminum-silicon series product silica molybdenum bricks commonly used in the low-temperature zone of cement rotary kilns. One of them is SiC Mullite Brick 1680, and the other is SiC Mullite Brick 1550. The static crucible method was used to conduct alkali corrosion resistance test. Sample blocks with dimensions of 80 mm × 80 mm × 80 mm were cut from various bricks, and a cylindrical groove of φ36 mm × 40 mm was drilled in the center to make a crucible. Then cut a 60 mm×60 mm×30 mm thin plate to make a crucible cover, and dry the crucible and crucible cover. Fill each crucible with 20 g of pure chemical K2CO3, and use fire clay to seal the space between the crucible lid and the crucible. The entire crucible was dried in an oven at 110°C for 12 h, then placed in an electric furnace and kept at 1100°C for 5 h until it cooled naturally. Evaluate the alkali corrosion resistance of the sample by observing the appearance of the sample.
From the appearance photos of the two crucibles after alkali erosion, it was found that there were no cracks in the 1680 SiC Mullite Brick and the 1550 SiC Mullite Brick. Among them, the change curves of K element content in SiC Mullite Brick 1680 and SiC Mullite Brick 1550 are consistent, with the largest content at the bottom of the crucible. As the erosion depth increases, the K element content drops sharply. After the depth reaches 20 mm, the K element content is close to 1% and no longer changes. The alkali erosion resistance of SiC Mullite Bricks is related to the introduction of silicon carbide and the apparent porosity of silica molybdenum bricks. The silicon dioxide generated by the oxidation of silicon carbide at high temperatures reacts with potassium carbonate on the surface of the refractory bricks to form a glass phase to form a dense layer. It can effectively inhibit the erosion and penetration of the K element so that the K element is concentrated in the brick surface area.
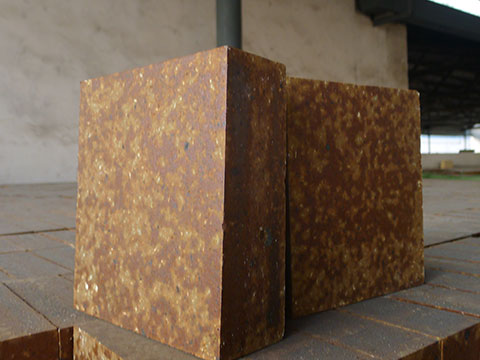
At high temperatures, the alumina in the matrix of SiC Mullite Bricks is easily eroded by alkali, and the silica and potassium generated by the oxidation of alumina and silicon carbide react to form a liquid phase. The liquid phase fills the pores of the silica molybdenum bricks, seals the pores and cracks in the contact area between the refractory bricks and the alkali, and forms a dense layer to prevent further penetration of the K element. Due to the addition of silicon carbide and partial oxidation into silicon dioxide to fill the pores in SiC Mullite Bricks 1680 and 1550, silica molybdenum bricks can significantly reduce alkali erosion and have excellent alkali erosion resistance.
Performance of Silicon Molybdenum Bricks for Cement Rotary Kiln
SiC Mullite Brick is an aluminum-silicon-based material made from silicon carbide, mullite, or alumina clinker and sintered at high temperatures. The main crystal phases of this material are corundum, mullite, and silicon carbide, and contain a small amount of cristobalite. Because of its good wear resistance, high mechanical strength, excellent corrosion resistance, and thermal shock stability. It can be widely used in all parts of the cement rotary kiln except the firing zone.
RS Refractory Brick Manufacturer and Seller
RS Refractory Material Manufacturer is a powerful manufacturer of refractory materials production and sales. Our refractory products are of reliable quality and have been sold to more than 100 countries around the world. Moreover, after our customers used our refractory lining materials, the service life of their kilns improved, and they decided to purchase refractory lining materials from us again. If you also need to extend the service life of the furnace lining or plan to modify the insulation layer of the kiln lining, please contact us to get a free solution and quotation.