The refractory materials used in the early part of the ladle slag line were directly combined with magnesia-chrome bricks, and electrofusion combined with magnesia-chrome bricks and other high-quality alkaline bricks. After the magnesia carbon bricks were successfully used on the converter, MgO-C brick was also used in the refining ladle slag line, and good results were achieved. With the advancement of smelting technology and new requirements for refractory materials, the traditional magnesia carbon bricks have found the following problems in the long-term application and practice.
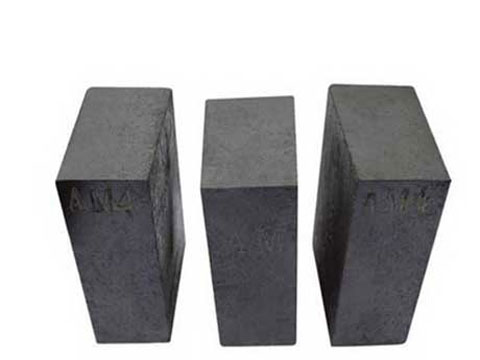
Problems in the Practical Use of Traditional Magnesia Carbon Bricks
- Due to high thermal conductivity and increased heat loss, the tapping temperature is increased and the energy consumption is increased. At the same time, a series of problems such as corrosion of refractory bricks materials have been increased;
- As the lining material of special refining furnaces, such as smelting high-quality clean steel and ultra-low carbon steel in VOD refining ladle, it will cause carbon increase problem;
- Consume a lot of precious graphite resources.
In view of the above, in recent years, the development of low-carbon magnesium-carbon bricks with low carbon content and excellent performance for refining ladle has attracted the attention of domestic and foreign industries.
Problems and Solutions of Low-carbon Magnesia-carbon Bricks in Use
The main problem caused by the reduction of carbon content in magnesia-carbon bricks is the decrease in thermal shock stability and slag resistance. As is known to all, when the carbon content in magnesium-carbon bricks is reduced, the thermal conductivity of the bricks is reduced, and the elastic modulus is increased, thereby making the bricks less resistant to thermal shock. After the carbon content is reduced, the wettability of the molten slag and molten steel with the material is enhanced, and the permeability of the material against molten slag and molten steel becomes poor.
To solve the problems in the use of low-carbon magnesium-carbon bricks, mainly from the following three aspects to improve.
1. Improve the thermal shock stability of magnesia-carbon bricks by improving the carbon structure combined with carbon.
The binder of traditional magnesia carbon bricks is mostly phenolic resin. The carbon structure of this binder after carbonization is an isotropic glass state. Therefore, the magnesia-carbon brick is brittle, the elastic modulus is high, which is detrimental to the thermal stability of the product, and the high-temperature strength of the product is also low.
After the introduction of graphitizable carbon precursors in the phenolic resin, this composite binder can be carbonized into secondary carbon with a flowing or mosaic structure under the environment of magnesium carbon bricks, or form nano-carbon fibers in situ. The thermal shock stability and high-temperature strength of low-carbon magnesium-carbon bricks are improved through the improvement of carbon structure and the enhancement of nano-carbon fiber formation.
2. Optimize the matrix structure of magnesia carbon bricks.
The thermal shock stability and slag resistance of magnesia carbon bricks mainly depend on the composition and structure of the matrix. How to increase the contact frequency of aggregate particles and carbon particles when the carbon content is greatly reduced. That is to reduce the size of carbon particles and ensure their high dispersion is one of the important measures to improve the thermal shock stability and slag permeability of low carbon magnesium carbon bricks. By adjusting the particle size composition of the matrix ingredients to control the size, shape, and distribution of the pores, it will also have a significant impact on the thermal conductivity of the material.
3. Using high-efficiency antioxidants.
With the reduction of carbon content in magnesia-carbon bricks, the oxidation protection of carbon is particularly important, so it is also necessary to use appropriate high-efficiency antioxidants.