Anti-stripping high alumina bricks were developed in cooperation with scientific research departments since the 1980s. It is widely used in the transition zone before and after the new dry process cement rotary kiln. The following is the performance of anti-stripping high alumina bricks analyzed by Rongsheng refractory fire bricks manufacturers.
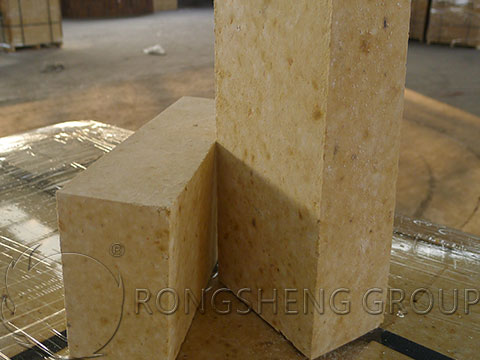
The Performance of the First Generation of Anti-stripping High Alumina Bricks
The first generation of anti-stripping bricks has been well used in large and medium-sized cement precalciners, kiln tail smoke chambers, indoor decomposition zones, coolers, and other parts with low temperature. The first generation of anti-stripping high alumina bricks is made of high alumina bauxite and zircon. It mainly uses the reaction of alumina and zircon during sintering to generate mullite and zircon to improve the thermal shock resistance of the material. The key point of the process is to control the sintering temperature and the particle size of zircon to produce a certain amount of oblique zircon and obtain higher compressive strength.
- One reason for the high thermal shock resistance of the anti-stripping high alumina brick is that the high alumina bauxite reacts with the added zircon to form mullite and oblique zircon, and microcracks are generated due to the phase transformation of zirconia. The delivery index of the anti-stripping brick under load softening temperature is ≥1470℃, and the actual index of load softening should be 1470~1500℃. Therefore, the firing temperature of anti-stripping high alumina bricks should be controlled below 1450℃. If the firing temperature is too high, part of the bricks will be deformed under pressure during firing, and the size of the bricks will be difficult to control.
- Another reason for the high thermal shock resistance of the anti-stripping high alumina brick is that the compressive strength of the brick is only 45MPa. Due to its low strength, it is beneficial to increase the thermal shock resistance factor RN.
- In addition, the anti-stripping brick contains a certain amount of ZrO2. After being corroded, a part of ZrO2 will melt in the liquid phase, increasing the viscosity of the liquid phase and delaying corrosion. Therefore, the corrosion resistance of anti-flaking bricks may be better than ordinary high alumina bricks.
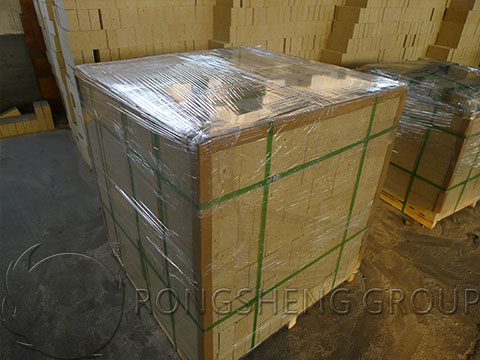
The Second-generation Anti-stripping High Alumina Brick
As a result, in the 1990s, scientific research departments once again cooperated and developed the second generation of anti-stripping high alumina bricks. It uses high alumina bauxite and zircon powder as additives, combined with resin. Give full play to the “toughening” effect of zirconia microcracks. Improved high-temperature resistance. And this material was tested in the transition zone of Huaxin 5000t/d new type dry process cement plant.
The thermal shock resistance of the first-generation anti-stripping brick and the second-generation anti-stripping brick are equivalent. However, the high-temperature flexural strength, load softening temperature, and compressive strength of the second-generation products are greatly improved compared with the first-generation products. Especially in the transition zone of cement rotary kiln, the effect is greatly improved.
The second generation of anti-stripping high alumina bricks uses high alumina bauxite as raw material, zircon powder as an additive, and water-soluble synthetic resin as a binder. After mixing and molding, the second generation anti-stripping high alumina brick fired at 1500~1550℃. Due to the complete reaction of alumina and zirconia at high temperatures, the mullite and zirconia matrix is formed, which fully exerts the “toughening” effect of the microcracks of zirconia. The refractory material obtains good high-temperature resistance and thermal shock resistance at the same time.
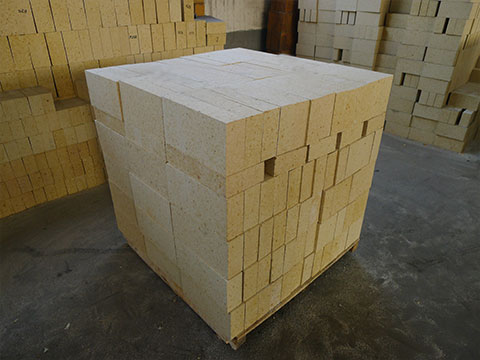
Compared with high alumina bricks, the second generation anti-stripping high alumina bricks have the following properties.
The flexural strength of high alumina bricks is 20MPa. After 20 times of forced air cooling at 1100°C, the flexural strength retention rate is about 70%. The flexural strength of the second-generation anti-stripping brick is 16MPa. After 20 times of forced air cooling at 1100°C, the retention rate of flexural strength is about 100%. Obviously, the thermal shock resistance of spalling bricks is much better than that of high alumina bricks.
- After sintering, the combination of aggregate and matrix in the high alumina brick is quite firm. There are large cracks at the interface between the aggregate and the matrix in the anti-stripping brick. However, the interface cracks of the anti-stripping brick did not penetrate the matrix. Therefore, the flexural strength of high alumina bricks is higher. Although the strength of the anti-stripping brick is low, it is not a big problem because the cracks around the aggregate do not penetrate the matrix.
- After 1100℃ water cooling for 20 times, the original dense structure of the high alumina brick was destroyed to a great extent. The crack developed quickly and penetrated into the matrix, and the flexural strength was reduced by nearly 30%. After the thermal shock, the interfacial cracks of the anti-stripping brick develop further, and the interfacial cracks also begin to communicate. But the crack did not penetrate into the matrix. Therefore, the loss of flexural strength is not large.
- Currently, on the market, the transition zone of the white ash-fired rotary kiln is also useful for anti-stripping bricks, and the firing zone of the rotary kiln that burns gemstones is also useful for anti-stripping bricks. There are some small diameter rotary kilns for non-ferrous metal smelting, and some choose to use anti-stripping bricks. In short, the peeling resistance high alumina brick is not as strong as the high alumina brick, but the high-temperature resistance and thermal shock resistance are much better than the high alumina brick.
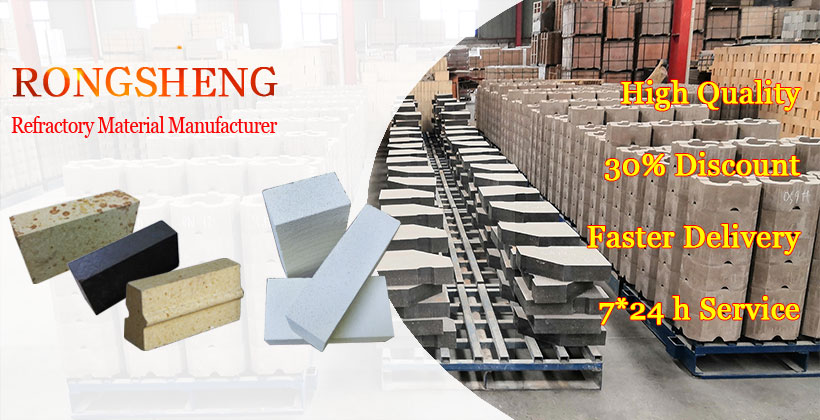
Rongsheng Refractory Brick Manufacturer
Rongsheng is an experienced cement kiln refractory manufacturer. Rongsheng’s refractory bricks and refractory castable products have successively received recognition from customers in more than 60 countries around the world. For example, India, Pakistan, Kuwait, South Africa, Malaysia, Vietnam, Netherlands, Philippines, Singapore, Egypt, Russia, etc. If you need to buy refractory materials for cement kilns, such as magnesia chrome bricks, silica mullite bricks, etc., please contact us or send us an email. We will provide you with services according to your specific needs.