By analyzing the reasons for the damage to the furnace bottom bricks in the carbonization chamber, a plan was adopted to repair the furnace bottom bricks with zero-expansion silica bricks at temperatures above 850°C. It solves the problem of repairing the bottom bricks of the carbonization chamber and achieves a successful thermal repair.
The bottom bricks in the carbonization chamber have been damaged and fallen off in the past two years. As production progresses, the bottom bricks are damaged in the carbonization chamber and dropped gradually from the machine side to the coke side. The resistance to pushing the focus becomes larger and larger, and the current to push the focus increases. The door frame and furnace column of the coke side furnace are greatly deformed due to the increase in stress, and the curvature of the furnace column is greatly increased compared with the normal furnace number, which poses a serious threat to the life of the furnace body and production safety. After discovering the above situation, the coking plant attached great importance to it and used cold repair methods to repair the bottom of the carbonization chamber several times, but failed, and the brick falling problem gradually worsened. Later, after many studies by relevant units and departments, it was decided to use zero-expansion silica bricks to repair the bottom of the carbonization chamber under hot conditions. A detailed repair plan was formulated. After full preparation and careful construction, the repair work was finally a one-time success.
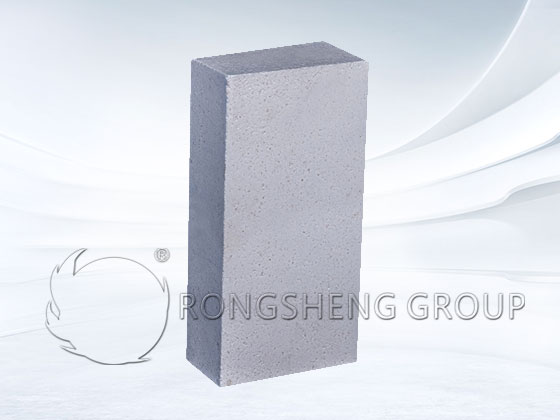
Working Conditions of the Furnace Bottom Bricks in the Carbonization Chamber
Analysis of the causes of damage to the furnace bottom bricks. There are many reasons for damage to the bottom bricks of the carbonization chamber. The refractory material of the coke oven body itself is not good, the quality of the masonry is poor, the structure of the furnace body is unevenly expanded, the temperature changes sharply when coal is loaded and coke is produced, and the corrosion effect of chemical substances in the gas at high temperatures. As well as the mechanical stress of the coke pushing rod when pushing coke, etc. will cause varying degrees of damage to the furnace body. The bottom bricks of the carbonization chamber are seriously damaged under the combined action of multiple factors.
-
Influence of refractory materials, masonry, and design
The physical and chemical indicators of refractory materials are not up to standard or there are deviations in size, and the quality of masonry is not up to standard. Defects such as too many transverse brick seams in the design of the furnace bottom bricks often cause damage to the furnace bottom bricks in individual carbonization chambers or even a certain brick. Mainly manifested in the surface erosion or fracture of the furnace bottom bricks, the refractory mud material falling off between the bricks, and the entire furnace bottom brick being pushed away during the coking process. The degree of damage is generally severe.
-
Factors affecting the focus pushing rod and its sliding shoe
The distance between the coke-pushing rod head and sliding shoe and the bottom brick of the carbonization chamber is not large. Once deformed due to the high temperature in the carbonization chamber, the furnace bottom brick will be directly scratched, or the sliding shoe will indirectly wear the bottom of the carbonization chamber by crushing a large amount of broken coke. Due to the large gravity, long stroke, and high frequency of use of the focus-pushing rod, the consequences of this defect are often universal. That is to say, using a defective coke pushing rod will cause damage to all the batches produced, and the coke side will be more serious than the machine side. The location and degree of damage to the furnace bottom brick can be seen from the sharp change curve of the coke-pushing current in the carbonization chamber.
-
Impact of Improper Production Operations
Improper production operations are caused by many factors. Hard objects such as furnace top bricks and ironware fall into the bottom of the carbonization chamber. Cause direct damage or indirect damage to the bottom brick of the carbonization chamber during coke pushing. The furnace cover is not tight and rainwater flows into the carbonization chamber. Failure or improper use of high and low-pressure ammonia water equipment causes ammonia water to enter the carbonization chamber. When the coke side furnace door is opened for too long during the coke pushing operation, the furnace bottom bricks are damaged or even burst due to strong rapid cooling and rapid heating.
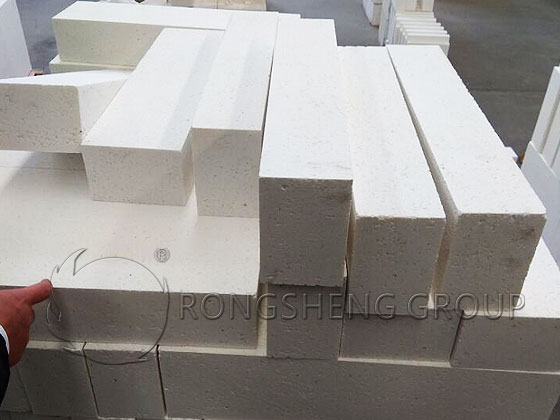
Selection of Carbonization Chamber Repair Technology
The difference between cold repair and hot repair
Renovating the entire row of furnace bottom bricks is rare among coke oven maintenance projects, and the construction is difficult. The quality of renovation is directly related to whether subsequent production can be carried out stably, and also related to the service life of the carbonization chamber and adjacent carbonization chambers. At present, the traditional repair methods include cold repair and hot repair, that is, cold repair and hot repair.
Cold repair means that after the carbonization chamber is cooled to 200~300°C, workers wear heat-insulating clothing and enter the carbonization chamber to perform repair operations such as cleaning, placing bricks, and pouring grout. In this method, the carbonization chamber needs to slowly cool down and heat up, and the construction period is also long, which takes about a week. Moreover, after the carbonization chamber undergoes rapid cooling and rapid heating changes, the damage to the furnace wall is serious. The most important thing is that the thermal stability of silica bricks is very poor. Its main mineral phases, tridymite, and cristobalite, as well as a small amount of residual quartz, cause serious changes in the volume of the masonry due to the crystal form transformation of the SiO2 variant at 180~270°C and 570°C. During the actual cold repair process of the carbonization chamber, the size of the reserved expansion joints of the furnace bottom bricks was not properly grasped. After the furnace temperature in the carbonization chamber rose to normal (1000~1100℃), the furnace bottom bricks arched, causing the repair to fail.
The method of hot repair is to use special tools to send zero-expansion silica bricks into the carbonization chamber to dry place them in a temperature state above 850°C, without workers entering the carbonization chamber, and then pour mortar for masonry construction. In this method, the temperature of the carbonization chamber does not need to be lowered too low, the construction period is short, and the impact on the furnace wall is small. Moreover, zero-expansion silica bricks are used as the renovation construction material. Under normal furnace temperature conditions, the damaged parts of the furnace bottom can be repaired directly without any expansion joints, effectively avoiding the disadvantages of the cold repair process.
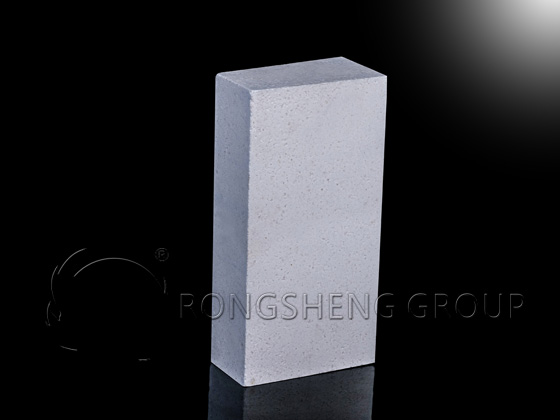
Repair effect
- (1) After the bottom of the carbonization chamber was thermally repaired with zero-expansion silica bricks, the coke-pushing current dropped from 250A to the normal 170A. So far, the coke has been pushed successfully for more than 200 times. The surface of the furnace bottom brick is smooth and there is no obvious wear. It shows that the use of zero-expansion silica bricks to repair the furnace bottom bricks has achieved the expected results.
- (2) The walls of the carbonization chamber are in good condition, with no major dents, cracks, etc. This shows that repairing the furnace bottom bricks with zero-expansion silica bricks at temperatures above 850°C has little impact on other parts of the furnace body.
Experience conclusion on repairing furnace bottom bricks in carbonization chamber
- (1) It is feasible to use zero-expansion silica bricks to repair furnace bottom bricks at temperatures above 850°C. The construction time is short, the quality is high, the damage to the furnace body is small, and the life of the coke oven body can be extended to the maximum extent. It solves the problems that are difficult to solve with traditional cold repair methods.
- (2) When there are fewer bricks falling off the bottom of the carbonization chamber, using zero-expansion silica bricks to thermally repair the bottom of the furnace will take less time and provide better results.
- (3) The remaining furnace bottom bricks during hot repair can be retained if they are in good condition, but those in poor condition should be removed.
- (4) In view of the reasons for the damage to the furnace bottom bricks, special inspection and supervision of the furnace bottom bricks should be carried out in daily production. Strengthen the inspection and correction of the focus pushing rod, strict production operation procedures and assessment, and other preventive measures. Only in this way can problems be nipped in the bud and major damage to the furnace bottom bricks avoided.