The Hot Metal Mixer is a device for temporarily storing molten iron between the blast furnace and the converter in order to maintain the balance between the molten iron supplied by the blast furnace and the needs of the converter. The main function of the Hot Metal Mixer is to store the molten iron and to uniformize the temperature and composition of the molten iron. In order to ensure the temperature at the time of tapping, the holding furnace is usually equipped with auxiliary burners for heating. Therefore, in order to ensure the smooth progress of production, it is necessary to configure reasonable refractories for hot metal mixer furnace.
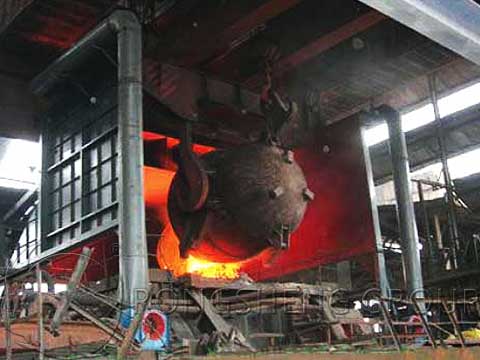
Damage of Refractory Ling for Hot Metal Mixer
The refractory materials used for the refractory lining of the hot metal mixer furnace are various, and the common masonry method is the comprehensive furnace lining. Because of the long-term storage of molten iron, the inner lining will be damaged by molten iron, molten slag, and gravity. The most vulnerable parts are the iron outlet, the slag line area, and the iron outlet.
Refractories for Hot Metal Mixer Furnace
According to the working environment of the mixed iron holding furnace and the cause of damage, it can be analyzed that the requirements for refractory materials used in the refractory lining of the Hot Metal Mixer furnace are high mechanical strength, strong slag resistance, good thermal shock resistance, low thermal conductivity, and little change in re-burning line. Therefore, refractory bricks commonly used in Hot Metal Mixer furnaces include high-alumina bricks, clay bricks, light-weight insulation bricks, and magnesium bricks. The refractory castables used include refractory fillers and spray refractory coating paints.
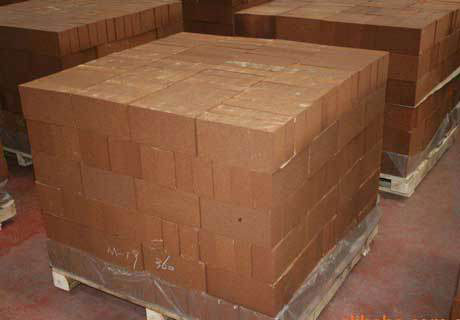
Generally, where the refractory lining of the metal iron holding furnace directly contacts the molten iron, magnesia bricks and magnesia-chrome bricks are used. Use high-alumina bricks and clay bricks for the parts that do not touch the molten iron. The iron outlet and runner are used directly combined magnesia-chrome brick and oil-immersed magnesia brick. However, some linings of hot metal mixer furnaces are made of high-alumina bricks because of the low alkalinity of slag and light erosion. In general, the refractory materials used in the hot metal mixer furnace are mainly magnesium bricks, and high alumina bricks are used in places where the slag basicity is small.
If the iron holding furnace is partially damaged, it can also be repaired using spray refractory coating paint to repair to increase the service life of the furnace lining. Some 1,000-ton hot metal mixer furnace linings can continue to produce for another 4-5 months after multiple hot spray refractory coating repairs, starting from exposing the permanent lining. Some furnace repair materials use magnesium refractory spray refractory coating paint. However, the use of high-aluminum refractory coating spray paint for repairs still accounts for a considerable proportion. The use of the high-aluminum refractory coating in a holding furnace is also good.
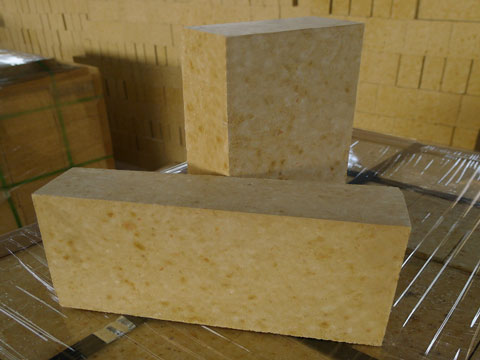
Rongsheng Refractory Material Manufacturer
Rongsheng is an experienced manufacturer of refractories. Rongsheng has an independent refractory brick production workshop and a refractory castable production workshop. RS’s refractory castable production capacity is 80,000 tons per year. Rongsheng’s refractory products have been sold to more than 60 countries and regions around the world. Such as Malaysia, South Africa, India, Indonesia, Pakistan, Netherlands, Kuwait, Kenya, Russia, United States, Philippines, Vietnam, etc. Refractory bricks’ quality is guaranteed. If you need to purchase refractory materials for holding furnace, please contact us. We will provide you with not only high-quality refractory materials but also prices that satisfy you.