High temperature refractory materials are structural materials used in high temperature furnaces with heat preservation and insulation functions. Almost all high temperature containers and equipment require matching refractory materials to achieve high temperature technical process conditions and protect the long-term stable operation of the furnace steel structure. The ability of the refractory materials in high temperature equipment to resist high temperature melt erosion directly affects the life of the refractory materials and the working life of the high temperature equipment. RS Cheap Fire Bricks for Sale Silicon Nitride Bonded Silicon Carbide Bricks – Aluminum Electrolytic Cell Side Wall Bricks, Free Quote Now!
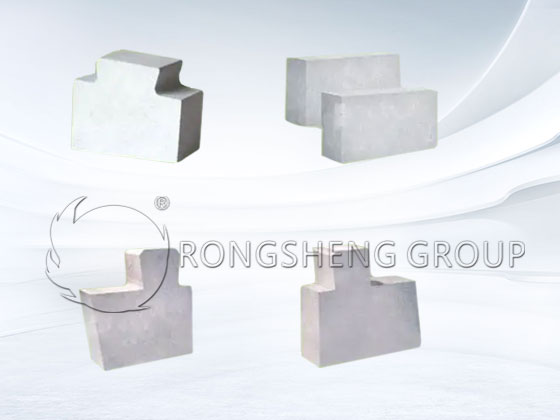
Silicon nitride combined with silicon carbide bricks – aluminum electrolytic cell side wall bricks
Among the aluminum electrolytic cell side wall bricks, after continuous research and development and technical upgrading and improvement by the new materials majors of national universities and the refractory industry, the refractory materials currently used are silicon nitride combined with silicon carbide refractory bricks, which are relatively good high-temperature refractory materials.
Compared with the composite bricks of silicon nitride combined with silicon carbide bricks and carbon refractory bricks, carbon refractory bricks are easily damaged by high-temperature oxidation, resulting in the problem of short life of the aluminum electrolytic cell body. However, the ability of silicon nitride combined with silicon carbide refractory bricks to resist the erosion of cryolite electrolyte melt is still very satisfactory. The design life of the domestic aluminum electrolytic cell body is generally about 5 years, while the actual service life of the foreign aluminum electrolytic cell body is generally more than 7 years, and some reach more than 12 years.
However, there is a gap between domestic silicon nitride bonded silicon carbide bricks and foreign ones. The main reason is that the ability of silicon nitride bonded silicon carbide refractory bricks to resist the erosion of cryolite electrolyte melt is slightly inferior to that of foreign ones. The general method adopted in China is to increase the thickness of silicon nitride bonded silicon carbide bricks to extend the working life of silicon nitride bonded silicon carbide refractory bricks. However, increasing the thickness of silicon nitride bonded silicon carbide refractory bricks not only increases the cost of bricks for the side walls of the electrolytic aluminum tank, but also adds a lot of difficulties to the manufacturing process of silicon nitride bonded silicon carbide bricks. When the thickness of silicon nitride bonded silicon carbide bricks increases, during the sintering process of the brick body, nitrogen cannot effectively penetrate into the interior of the brick body, and reacts with silicon powder to form a silicon nitride bonding phase. It is easy to cause quality problems such as incomplete nitridation of silicon powder inside silicon nitride bonded silicon carbide refractory bricks, brick body stratification, brick body sandwich, and low brick body strength. This directly affects the quality and use effect of silicon nitride bonded silicon carbide refractory bricks.
Therefore, compared with foreign countries, the technology and products of silicon nitride combined with silicon carbide bricks in China need more attention and attention. Improve the quality of products and strive to reach international standards, or even surpass foreign technical levels. RS refractory brick manufacturer is committed to providing high-quality refractory brick lining materials for high-temperature industrial furnaces, with reliable product quality and perfect customer service. It can effectively ensure the longevity and efficient operation of high-temperature industrial furnace linings.
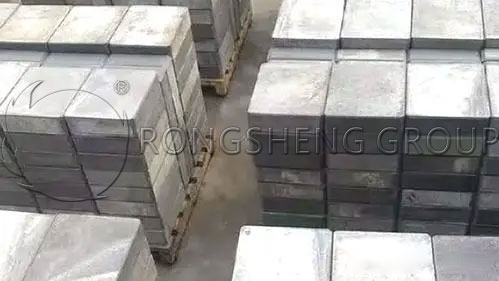
Refractory materials for electrolytic aluminum – silicon nitride combined with silicon carbide bricks
Silicon nitride combined with silicon carbide is a special high-grade refractory material and the fourth generation of refractory products. The new refractory bricks made of this material have high high-temperature strength, good thermal conductivity, good oxidation resistance and thermal shock resistance. And corrosion resistance, good high-temperature creep resistance and other characteristics. At present, refractory materials for electrolytic aluminum – silicon nitride combined with silicon carbide bricks are widely used in many industries and have excellent performance. Silicon nitride combined with silicon carbide bricks are mainly used in the side walls of electrolytic cells of modern large-scale aluminum plants, the waist of ultra-large iron-making blast furnaces with high technical content, and high-grade kiln furniture.
Silicon nitride combined with silicon carbide brick materials are a reasonable combination of coarse, medium and fine particles of SiC and Si powder. Assisted by certain additives and binders, they are fully mixed in a bell-shaped mixer. Then they are cast and formed, and after drying, they are loaded into a large atmosphere furnace and fired in a pure atmosphere. The Si in the green body is converted into Si3N4, thereby obtaining a SiC composite material with Si3N4 as the binding phase.
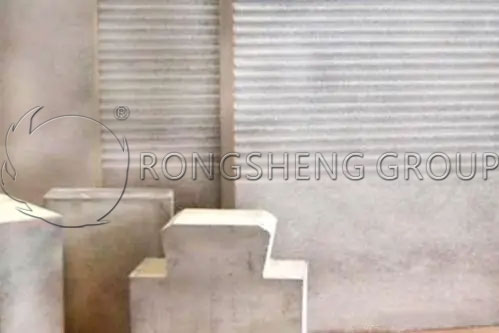
The production process of silicon nitride combined with silicon carbide bricks
The application of silicon nitride combined with silicon carbide brick refractory materials can effectively reduce energy consumption and reduce product defects. It can improve product quality and reduce the kiln furniture cost per unit product. It is an ideal new kiln furniture material. The production process of silicon nitride combined with silicon carbide bricks is as follows:
- Mixing. Mix the materials in the process and mix them in a mixer for no less than 15 minutes. After mixing, the clay needs to be screened through a 5mm screen to remove the impurities that are screened out.
- Molding. Use a brick press that has been checked and can operate normally and a size mold that has been adjusted to start pressing. Note: Before pressing, check the size, thickness and bulk density of the brick embryo ≥ 2.6g/cm. When pressing, lightly press the thickness and heavy first to ensure that the edges and corners are flat and neat.
- Drying. The brick embryo should be dried naturally in a drying room, and the temperature of natural drying should be between 20-30 degrees Celsius.
- Firing. During firing, cover the furnace at 300 degrees Celsius, blow water vapor at 500 degrees Celsius, and vacuum and fill with nitrogen at 600 degrees Celsius. Make sure the furnace pressure is +0.01~+0.045Mpa.
- Sorting out of the kiln. Stamp the qualified finished products, select the unqualified finished products, and stack them in the designated location. Make a good defect responsibility analysis and keep records.
RS refractory brick manufacturer strictly controls the raw materials of refractory bricks and the process in the production process, aiming to produce high-quality refractory brick products with a high pass rate. To meet the increasingly demanding production conditions of high-temperature industrial furnaces and extend the service life of the furnace lining. To buy high-quality silicon nitride combined with silicon carbide bricks, please choose RS Cheap Fire Bricks Factory, our customers are in more than 120 countries around the world, such as South Africa, Chile, Egypt, Colombia, Uzbekistan, Italy, Indonesia, Ukraine, Hungary, Spain, Kenya, Syria, Zambia, Oman, Venezuela, India, Peru, the United States, Ethiopia, etc. The product quality is reliable and the customer service is guaranteed. Contact us to get free solutions and quotes for refractory linings.