Phosphate wear-resistant bricks are refractory bricks made of ordinary phosphate-bonded high-alumina bricks through special processes and chemical additives. Its wear resistance and load-softening temperature are greatly improved. Moreover, its high-temperature performance and thermal shock resistance are also better than those of phosphate-bonded high-alumina bricks. Phosphate wear-resistant bricks have high compressive strength at room temperature, good thermal shock stability, good wear resistance, and strong slag resistance. The application of phosphate wear-resistant bricks in rotary kilns is suitable for rotary kiln firing zone, transition zone, cooling zone, cooler, etc., as well as the high-temperature zone of a cement shaft kiln.
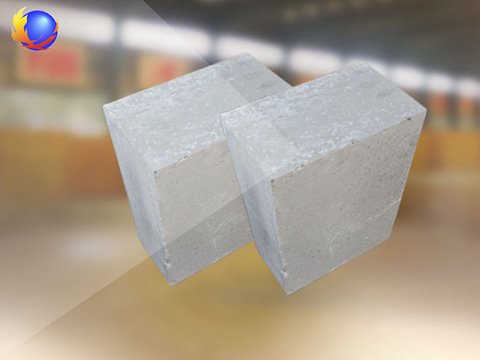
Application of Phosphate Wear-Resistant Brick in Rotary Kiln
Phosphate wear-resistant bricks are mainly used as linings for high-temperature parts of cement rotary kilns and are used for severely worn parts of cement rotary kilns. Cement rotary kiln mouth, kiln tail, cooling zone, cooler and high-temperature zone of a cement shaft kiln. Phosphate wear-resistant bricks can also be used in rotary kilns with a kiln diameter greater than 4 meters.
Phosphate combined high alumina kiln lining brick for cement kiln
Phosphate-high alumina bricks for cement kilns are widely used. It can be used in preheating zone, decomposition zone, transition zone, and cooling zone as its inner lining. It can also be used as a lining in the firing zone of a cement kiln with a diameter of fewer than 3 meters.
Phosphate-bonded high-alumina bricks for cement kilns can be divided into two types according to different binders.
- Phosphate high alumina brick. The concentration of the binding agent is 42.5%~50% phosphoric acid solution. The code name is P, and the code name of the lock seam brick is PC.
- Aluminum phosphate combined with high alumina wear-resistant brick is referred to as wear-resistant brick. The binder is an aluminum phosphate solution prepared from industrial phosphoric acid and industrial aluminum hydroxide. The molar ratio is: Al2O3: P2O5 =1:3.2, codenamed PA.
Phosphate-high alumina bricks have good thermal stability. When the temperature of the cement kiln lining changes sharply, the phosphate-high alumina bricks will not burst, or peel off, and the kiln skin will not collapse. And it is easy to hang the kiln skin and has high wear resistance, so the service life is long.
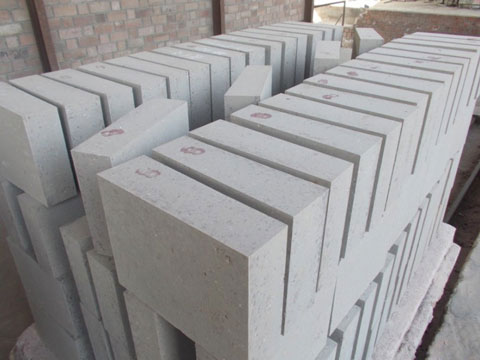
Can ordinary phosphate wear-resistant bricks be used in the firing zone of a lime rotary kiln?
It is not acceptable to use ordinary phosphate wear-resistant bricks in the firing zone of the lime rotary kiln.
Because the bulk density of ordinary phosphate wear-resistant bricks is about 2.6, the degree of erosion at the firing zone temperature is not suitable for ordinary bricks, and phosphate composite bricks with a bulk density above 2.75 must be used. Silicon carbide is added to the phosphate composite brick, and the wear resistance and corrosion resistance are higher than those of ordinary phosphate bricks.
The temperature of the lime rotary kiln is different in each zone, and it is appropriate to use different grades of phosphate bricks when the lining is used. Some lime rotary kilns with small kiln diameters use high-alumina bricks for transition zones. Because lime is an alkaline atmosphere, the phosphate brick is also an alkaline atmosphere, which is consistent with the lime atmosphere. Therefore, it is a good choice to use the phosphate brick series for the lining.
If the kiln diameter of the lime kiln is large, magnesia-alumina spinel bricks are also used as the lining. Because the price of magnesia series refractory bricks will be relatively higher. At present, there are many phosphate composite bricks on the market. Phosphate composite bricks have a variety of composites, including silicon carbide composites, lightweight materials, and triple composite bricks with lightweight materials and silicon carbide. However, they are all fired with phosphoric acid.
Phosphate composite bricks compounded with lightweight materials have light kiln weight and good thermal insulation performance, which can save fuel. However, this composite also has the disadvantage that it is easy to break light and heavy. If it is integrated with silicon carbide composite bricks, but the kiln weight is high, the thermal insulation performance is not as good as that of lightweight composite bricks, but this composite brick is not easy to break. That is to say, in the process of use, each has its own advantages, which are only determined according to the user’s usage habits and production needs.
In general, for phosphate wear-resistant bricks, more phosphate composite bricks are used in the firing zone. Because this brick is wear-resistant and corrosion-resistant. However, if ordinary phosphate wear-resistant bricks are used in the firing zone, firstly, they cannot be hung with kiln skin, and secondly, their own matrix cannot meet the high-temperature requirements. Therefore, it is not acceptable to use ordinary phosphate in the firing zone of the lime rotary kiln.