The electrolytic cell is an important component in the aluminum electrolysis process. The two main factors that affect the life of aluminum electrolytic cells are carbon cathodes and lining refractory materials. Aluminum electrolytic cell linings are divided by region and can be divided into bottom linings and side linings. Functionally, the bottom lining plays a role in supporting the cathode structure and insulating heat. The sidelining mainly plays a role in protecting the surface of the steel metal casing from erosion by the electrolyte melt.
The side lining of the aluminum electrolytic cell is an important structural part of the electrolytic cell. The side wall material of the aluminum electrolytic cell should have the following important properties at high temperatures. It has high resistivity, and good thermal conductivity, and does not react chemically with molten cryolite. The porosity is small, impermeable to electrolyte and aluminum, and not oxidized by air.
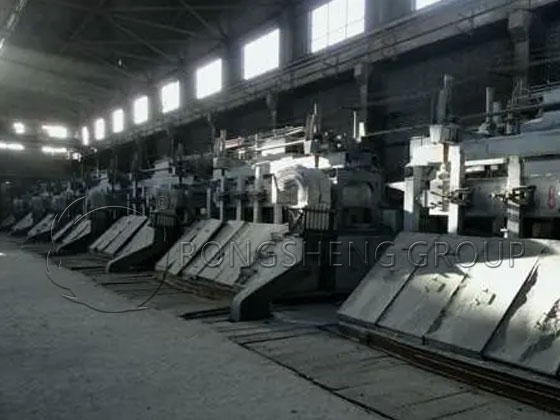
Due to the valence bond structure characteristics of silicon carbide, it has a series of excellent properties. Such as high strength, high hardness, high-temperature resistance, and oxidation resistance. High thermal conductivity, low thermal expansion rate, excellent thermal shock resistance. Good chemical stability, not wetted by non-ferrous metals, etc. In particular, it has good resistance to high-temperature chemical corrosion and is particularly suitable as a refractory material for lining aluminum electrolytic cells.
With the development of material technology and the increase in the capacity of electrolytic cells, the material structure of the lining on the side of the electrolytic cell has gradually evolved from the early structure of double carbon blocks plus insulation bricks to no insulation bricks, single-layer carbon blocks, and even Today’s silicon carbide alone is combined with silicon nitride materials.
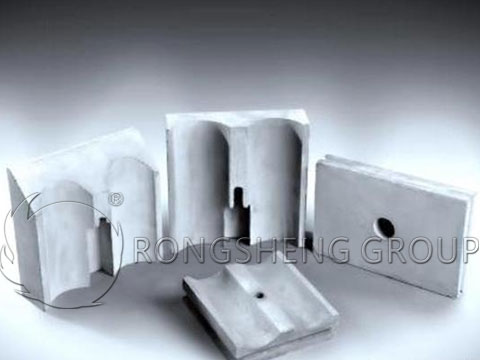
Silicon Nitride Bonded Silicon Carbide Bricks for Electrolytic Aluminum
Silicon nitride bonded silicon carbide bricks refer to refractory products that use SiC and Si as raw materials and are nitrided and fired. It is characterized by using Si3N4 as the binding agent. Si3N4 exists between Sic grains in the form of needle-like or fibrous crystals and is an important new refractory material. Generally, it contains 70%~75% silicon carbide and 18%~25% silicon nitride. It has good corrosion resistance, with a 1400 flexural strength of 50~55MPa and an apparent porosity of 15%. Prepared by high-temperature firing method. Mainly used in blast furnace tuyere, aluminum electrolytic cell lining, etc. At present, the price of silicon nitride bonded silicon carbide bricks is relatively high, generally between 18,000 yuan and 22,000 yuan/ton.
Advantages of Silicon Nitride Combined Silicon Carbide Bricks in Electrolytic Cells
The traditional electrolytic cell side wall materials are mainly pre-coated carbon bricks and graphitized carbon bricks. Although carbon materials have strong resistance to alkali erosion in non-oxidizing atmospheres, they are easily oxidized, have low strength and poor resistance to peeling. Therefore, it is easy to be damaged when used in an electrolytic cell and has a short service life. The main reasons are:
- ① The introduction of sodium causes swelling, loosening, and stratification.
- ② The formation of AL4C3 dissolved in the aluminum liquid increases the wettability of the slag to the carbon surface and further promotes the penetration of the electrolyte.
- ③ The oxidation resistance is very poor, and the designed heat transfer structure is destroyed after oxidation. The furnace side is melted, solid and liquid are in direct contact, and the corrosion rate is accelerated.
- ④The resistance is small, causing horizontal current and reducing current efficiency.
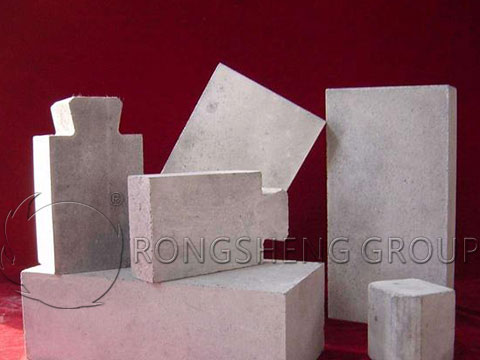
With the continuous development of industry technology, a material that is superior to graphite carbon bricks and ordinary carbon bricks is silicon nitride combined with silicon carbide bricks. Below we make a comparison of these three materials. Performance comparison of side carbon blocks, graphitized carbon bricks, and silicon nitride bonded silicon carbide bricks for electrolysis.
Items | Silicon Nitride bonded Silicon Carbide Bricks | Ordinary Carbon Bricks | Graphite Carbon Bricks |
Maximum Use Temperature in Air ℃ | 1760 | 450 | 530 |
Compressive Strength MPa | 180 | 25 | 23 |
Bulk Density g/cm3 | 2.62 | 1.50 | 1.70 |
Resistivity ×106 Ω·m | 8000 | 45 | 1.5 |
It can be seen from the above table that compared with traditional carbon blocks, the advantages of silicon nitride bonded silicon carbide bricks are:
- ①It can improve the service life. Because of its strong resistance to corrosion such as cryolite, it also has good antioxidant properties.
- ②Good mechanical strength. The thickness of the lining can be reduced to increase the working volume in the tank and the electrode energy accordingly.
- ③Reduce unit power consumption. Because the conductivity is high, it is easy to form a furnace core, which reduces the horizontal current and reduces the electrical loss accordingly.
In short, the use of silicon nitride combined with silicon carbide bricks can greatly improve the life of the aluminum electrolytic cell lining compared with the use of traditional materials (carbon blocks). It saves energy and the use of materials, thereby saving business costs, etc.
Silicon nitride combined with silicon carbide bricks are not corroded by molten aluminum and their excellent thermal properties make them widely used in the aluminum industry. Using high-quality silicon nitride combined with silicon carbide materials to replace traditional carbon materials on the side walls of electrolytic cells has achieved significant benefits. Silicon nitride bonded silicon carbide bricks have been used on the side walls of many 240KA and 320KA aluminum electrolytic cells in many companies for more than 5 years. The outer temperature of the furnace wall has not yet increased, which indicates that the furnace wall lining material has not been damaged. It is fully proved that the application of silicon nitride combined with silicon carbide bricks in aluminum electrolytic cells promotes the development of the industry.
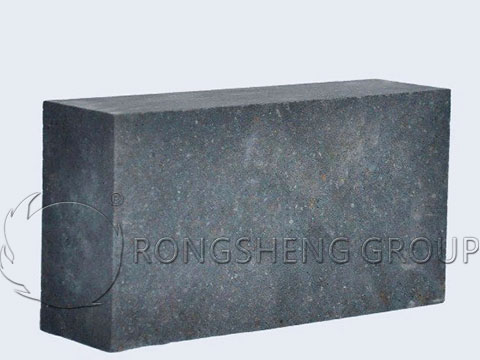
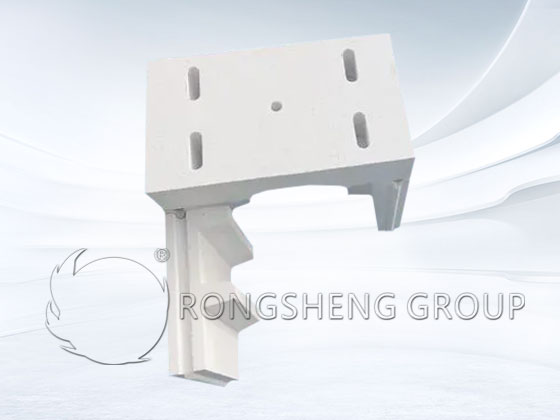
Refractory Bricks for Aluminum Smelting Reverberatory Furnace
Aluminum smelting reverberatory furnaces use high alumina bricks, corundum bricks, mullite bricks, silicon carbide bricks, etc. Aluminum smelting reverberatory furnace requires refractory materials to have the characteristics of resistance to the penetration of aluminum liquid and magnesium vapor, excellent wear resistance and thermal shock resistance. In order to meet these requirements, different types of refractory materials need to be used in different parts.
- Furnace lining Furnace lining is the part that comes into contact with liquid aluminum. It is generally built with high-aluminum bricks with an Al2O3 content of 80%-85%. When smelting high-purity metallic aluminum, mullite bricks or corundum bricks are used. These materials have good heat resistance and corrosion resistance, and can effectively prevent the penetration of liquid aluminum and magnesium vapor.
- Slopes and easily eroded areas In areas that are easily eroded and worn, such as the slope of the hearth and where scrap aluminum materials are installed, silicon nitride-bonded silicon carbide bricks need to be used. This material has good wear and corrosion resistance and can effectively extend its service life.
- Aluminum flow trough and aluminum outlet. The aluminum flow trough and aluminum outlet are severely eroded by aluminum liquid. Generally, self-bonding or silicon nitride-bonded silicon carbide bricks are used, and zircon bricks are also used as linings. These materials have good erosion and corrosion resistance and can effectively prevent the erosion and corrosion of liquid aluminum.
- Aluminum outlet blockage For the aluminum outlet blockage, vacuum cast refractory fiber can be used. This material has the function of blocking the blockage.
- Furnace linings that are not in contact with liquid aluminum are generally made of clay bricks, clay refractory castables or refractory plastics. These materials have good heat resistance and corrosion resistance and can meet the requirements of parts not in contact with molten aluminum.
- The lining of the aluminum flow tank is generally made of silicon carbide bricks, or prefabricated fused foam silicon bricks can be used. These materials have good heat resistance and corrosion resistance and can effectively extend their service life.
When purchasing refractory materials for aluminum smelting furnaces, please choose a refractory manufacturer with strong capabilities. Not only can we provide high-quality refractory products, but our comprehensive customer service can guarantee the longevity of high-temperature industrial furnaces.