How do we make the service life of the glass furnace wall longer? Solutions for extending the life of glass kiln wall tiles. As the part in contact with the molten glass, the wall of the glass furnace requires the refractory material to have good resistance to the erosion of the molten glass, and at the same time, it must not pollute the molten glass. Glass kiln pool wall bricks usually use fused AZS zirconium corundum bricks.
The liquid level line of the pool wall bricks is located at the three-phase interface of gas, solid, and liquid, and is subject to the direct erosion of the material pile and glass liquid at high temperatures (~1500°C). The operating environment is very harsh, so this part is the most severely corroded. The rate of liquid line erosion not only affects the time it takes to lay bricks for the first time but also affects the overall life of the kiln, including the stability of the superstructure. So, what are the factors that affect the liquid level of pool wall tiles? How can we extend the service life of the pool wall?
The Corrosion Mechanism of Electrofused AZS by Soda-Lime Glass
- The alkali (Na) in the glass liquid diffuses into the brick through the glass phase of the AZS brick.
- The infiltrated Na causes the dissolution of eutectic, mainly Al2O3, forming a “glass-refractory” interface layer enriched in Al2O3 and a small amount of ZrO2 crystals. See Figure 1. When the interface cannot be completely digested by the glass liquid, the interface layer (rich in Al2O3 and ZrO2) is the origin of glass defects (striations, primary zirconium stones).
- The renewal of the “glass-refractory” interface layer, that is, glass liquid flow and convection, brings fresh glass liquid into contact with the refractory material, accelerating erosion.
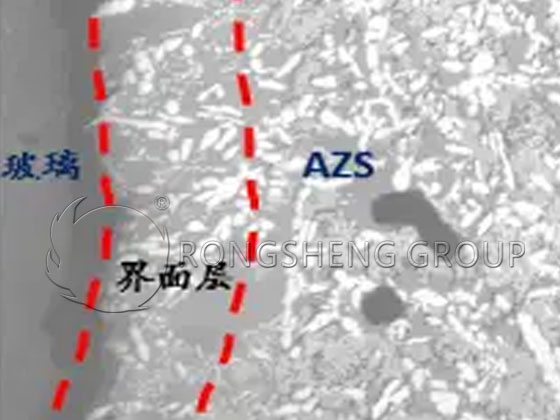
Factors Affecting Liquid Level Line Erosion
For a given glass composition, several factors influence the rate of erosion at the liquid level.
- The brand of AZS bricks (ZrO2 content) and their quality (glass phase and impurities, oxidation degree and density, etc.).
- The quality of the kiln (are there serious cracks in the pool wall tiles?).
- Operating conditions:
-
- – Temperature, pulling amount and glass flow rate.
- – Control of the material pile (whether it touches the tank wall).
- -The shape and length of the flame.
- The life and design of hook bricks.
(1) The Influence of the Quality of AZS Bricks Themselves.
When exposed to molten glass, the corrosion resistance of fused AZS pool wall tiles is different, as shown in Figure 2. Among them, the ZrO2 content and the quality of the glass phase are the main influencing factors.
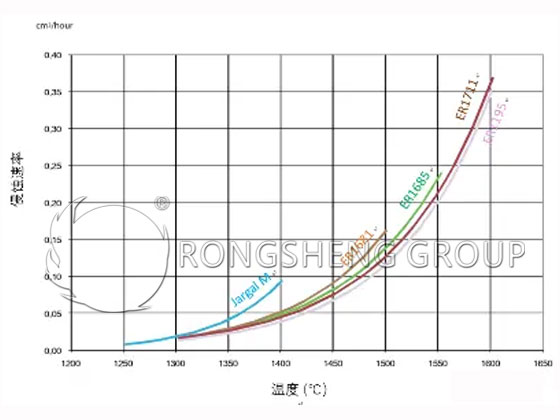
When choosing fused AZS refractory materials, people often focus only on the ZrO2 content and the density of the bricks. Although these two parameters are important, they are not the only parameters to consider when selecting AZS refractory materials. The most important performance difference comes from the quality of the glass phase.
The glass phase in AZS bricks accounts for about 21% by weight, but about 33% by volume. The glass phase is an essential component in the manufacture of fused AZS bricks, which is the component with the lowest melting point in AZS bricks. Therefore, this has become the weakest component of AZS refractory material in the corrosion resistance process.
(2) Influence of Kiln Quality
During the kiln baking process, due to the local insulation on the back of the pool wall bricks, the AZS bricks generate stress due to the large overall temperature gradient. These stresses can sometimes cause cracks on the cold side of the pool wall tiles, mainly vertical cracks. See Figure 3.
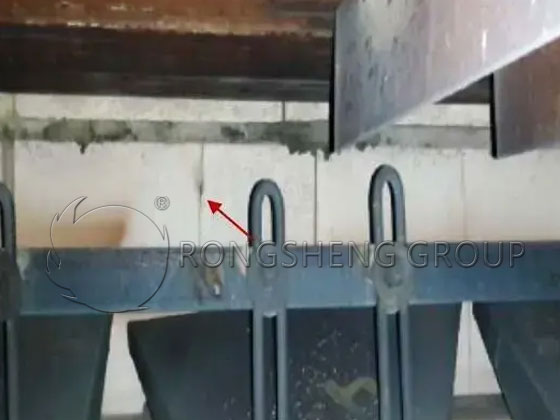
During the kiln baking process, the pool wall bricks will more or less have vertical cracks. Vertical cracks will not affect the kiln age. Figure 4 shows a kiln after 2 years of operation. A shut down the furnace. The vertical cracks on the cold side of the pool wall tiles are long and wide, while the corresponding cracks on the hot side are in a state of compressive stress, so the glass liquid will not penetrate into the cracks.
However, it is necessary to avoid horizontal cracks or explosions during the kiln-baking process. Transverse cracks will significantly advance the time of first tiling, affecting the service life of the pool wall tiles.
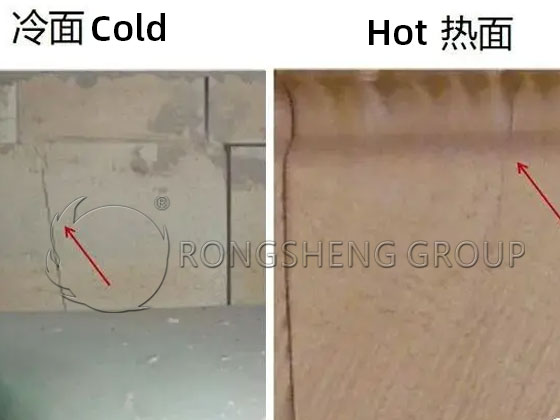
Although the cooling effect at the liquid level line is limited in the initial stage of production, the pool wall cooling air should be turned on as early as possible during the kiln baking period. At least before the temperature reaches 500°C, in order to reduce the thermal stress that causes vertical cracks on the top surface of the pool wall tiles.
(3) Effect of Temperature
The erosion rate of AZS bricks increases significantly with the increase of temperature, as shown in Figure 5. For every 50°C increase in the glass-refractory interface, the erosion rate almost doubles.
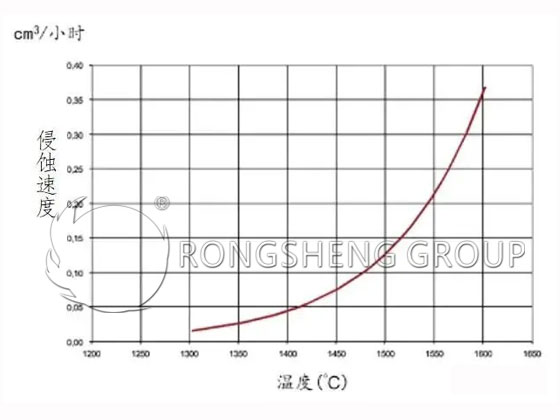
Through proper cooling and good protection of the hook bricks (protection against heat radiation), the lowest refractory interface temperature can be maintained.
Cooling of the backside of pool wall tiles is one of the most effective methods of slowing erosion at the liquid level. Usually, air cooling is used, as shown in Figure 6. The recommended cooling air flow rate at the liquid level is 1000 liters/second and the wind speed is 30 meters/second. The minimum air volume for severely eroded areas is 1300 liters/second and the flow rate is 50 meters/second.
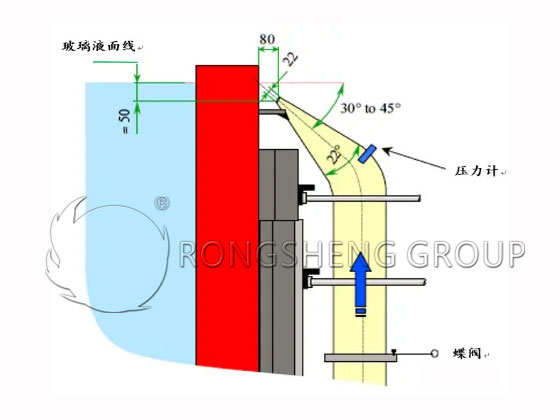
(4) Influence of Glass Flow Rate
The erosion rate of AZS accelerates as the glass flow rate (the flow rate of the glass liquid close to the refractory interface) increases. See Figure 7. The flow rate of molten glass is related to the pulling amount and the speed of glass convection occurring in different parts of the kiln.
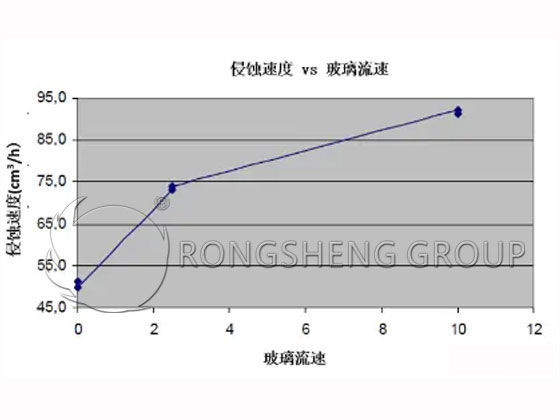
(5) The Protective Effect of Hook Bricks
The hook brick is located above the pool wall brick, and its function is equivalent to a “protective umbrella” for the liquid level line. See Figure 8. It can block the heat radiation from the flame space and reduce the temperature of the liquid level line. At the same time, it also prevents steam, dust and flowing materials from corroding the liquid level line.
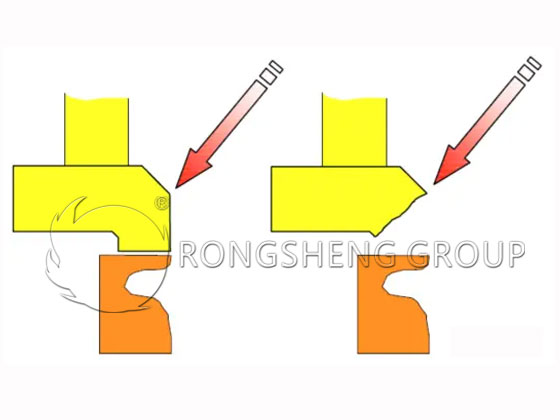
The working environment of hook bricks is harsh. The temperature gradient is high and it can withstand the erosion of batch dust, alkali vapor, and parapet flow. Thermal stress changes are caused by combustion reversal and tiling operations, interruption, and restart of cooling air.
After the kiln has been in operation for 4 to 7 years or during the kiln baking period, the hook bricks sometimes “turn around”. See Figure 10. The most serious parts are small furnaces No. 1 to No. 3 of the float kiln and under the combustion gun of the bottle kiln.
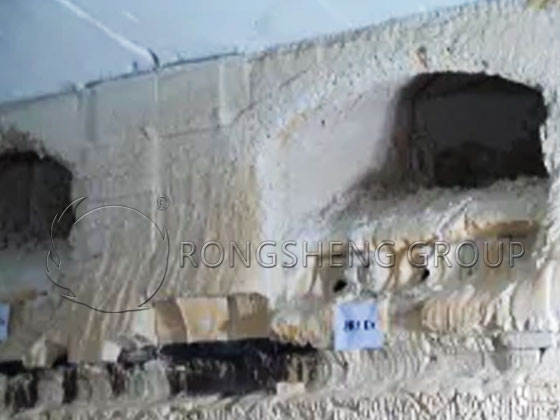
Solution for Hook Brick Fracture
In view of the fracture phenomenon of hook bricks, the following improvements have been made:
- Hook brick shape. Right-angle hook heads will cause stress concentration and lead to cracking, see Figure 11. The use of obtuse angles (cold surfaces) can limit the occurrence of cracks. At the same time, the round hot surface reduces the accumulation (erosion) of runoff. The improved shape is shown in Figure 12.
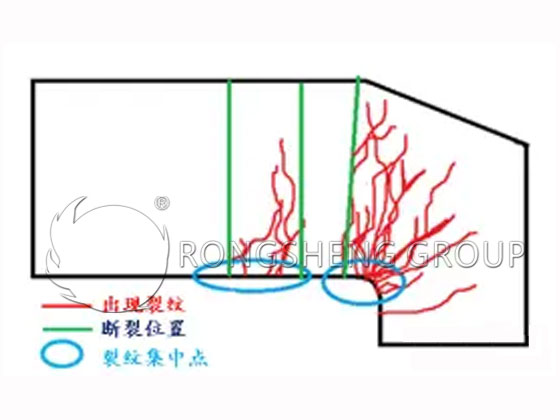
- The bottom surface is insulated. Because the iron plate conducts heat quickly, an integrated composite insulation board is installed on the bottom of the hook brick (see Figure 13). The temperature gradient of the hook brick can be reduced, thereby improving the thermal shock resistance of the hook brick.
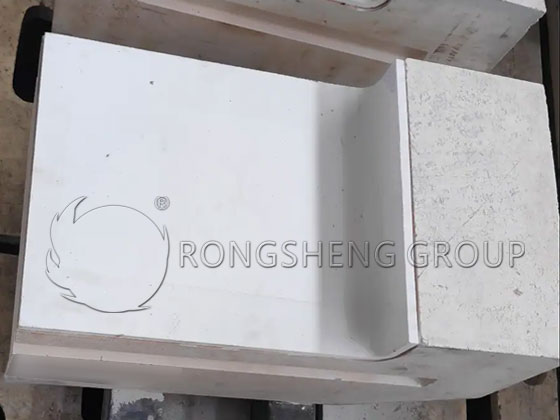
Solutions for Pool Walls
Throughout the kiln period, the remaining thickness of the liquid level line of the pool wall bricks continues to decrease. The erosion rate changes throughout the kiln period.
In the early stage of production, the cooling wind has little influence on the temperature of the refractory interface at the liquid level line, and the erosion is rapid. However, as the thickness of the pool wall bricks at the liquid level continues to become thinner, the influence of the cooling wind gradually increases, and the temperature of the refractory interface drops sharply. Thus erosion slows down. See Figure 15, The relationship curve between the remaining thickness at the liquid level line of the pool wall tiles and the refractory interface temperature.
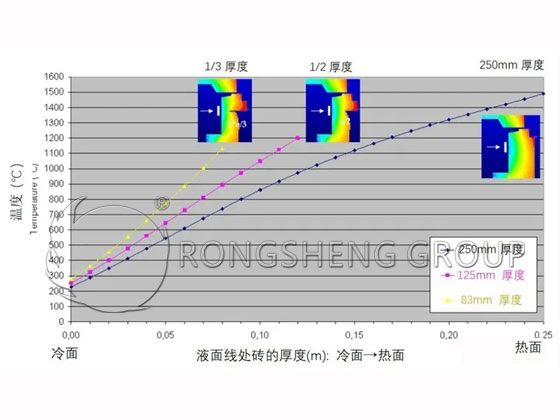
(1) Tiling the Pool Wall
Generally speaking, the service life of European float glass furnaces is 15 to 18 years. The first tiling is usually done after 4 to 6 years of operation, and the locations are No. 3 and No. 4 small furnaces.
When the remaining thickness of the pool wall at the liquid level is about 30~40mm, it is necessary to consider tiling outside the furnace to prevent glass leakage accidents (see Figure 16). Tiling other parts can be done later.
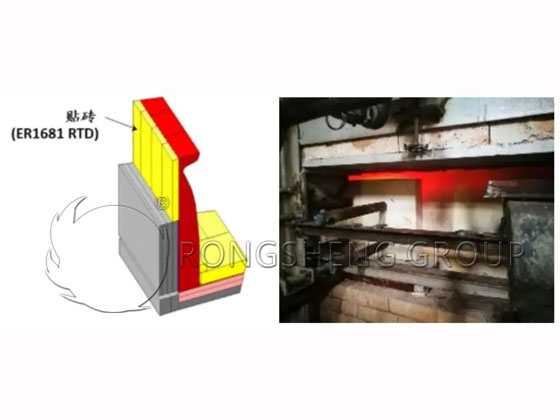
The thickness of the tiles is usually 75mm for the best cooling effect. The height of the tiling is 300~600mm, which depends on the location of the kiln (erosion condition), tiling time (first, second, or third time), and available space.
The service life of each brick laying is about 2 years, and the bricks can be laid up to 4 times during the entire kiln period. For ultra-white glass kilns, during the second tiling, the glass manufacturer will adopt overall (entire height) tiling in areas with severe corrosion.
(2) Heat Supplementation of Pool Wall
Some parts of the glass kiln are severely corroded, but they cannot be tiled because of the narrow space and complex shape. For example, the corner of the charging port of the bottle furnace or the corner of the neck of the float furnace.
In response to the erosion of this kind of area, the hot repair product HOT OVERCOAT AZS has been launched. This is a self-leveling multi-functional thermal patching material made of electrofused AZS aggregate, as shown in Figure 17.
First install the tire mold, and then pour HOT AZS mud into the tire mold. Because this castable has good fluidity and a wide construction temperature range, it is easy to fill in place. This thermal patching solution is easy to construct, has dense filling, and has a long service life.
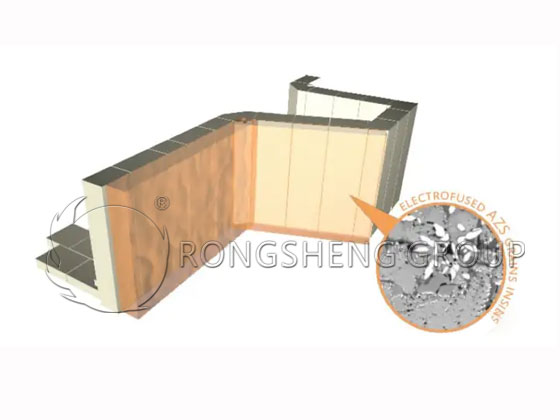
After understanding the corrosion mechanism of pool wall tiles, controlling the various factors that affect erosion, and then assisting with maintenance solutions such as tiling and hot repair will help extend the service life of pool wall tiles. Regarding glass kiln pool wall tiles, contact us for free to get more solutions.