Carbon roasting furnace is the core equipment for producing graphite electrodes, aluminum anodes, and other products. Its function is to coke the binder (such as coal tar) through high-temperature heat treatment, usually 800~1300℃, to improve the mechanical strength and conductivity of the product. Since the roasting process involves harsh working conditions such as high temperature, reducing atmosphere, volatile gas erosion, etc., the selection of refractory bricks directly affects the life of the furnace, energy consumption and product quality.
Carbon Roasting Furnace Working Characteristics
Carbon roasting furnace working characteristics: high temperature, high pressure, strong oxidation.
According to the heating method and structure, carbon roasting furnaces are mainly divided into: ring roasting furnace (mostly used for large-scale production) and tunnel kiln (suitable for small and medium-sized or special carbon products).
The ring roasting furnace consists of multiple furnace chambers arranged in a ring, heated by the fire channel, and the flue gas is recycled. The advantages are high thermal efficiency, suitable for continuous production, and large production capacity (such as anode roasting for aluminum). The disadvantages are high investment and complex temperature rise curve control.
The tunnel kiln products move in the kiln car and pass through the preheating, roasting, and cooling zones in turn. Its advantages are precise temperature control and suitable for multi-variety production. The disadvantages are high energy consumption and high maintenance costs.
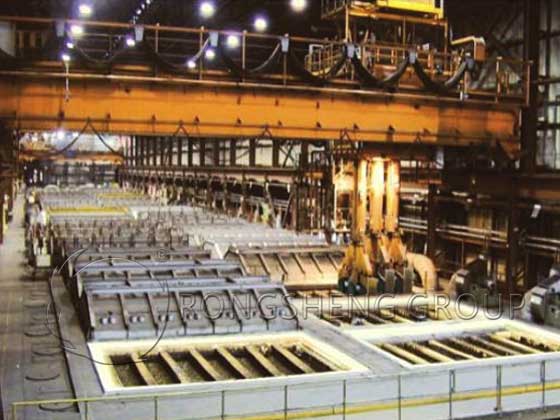
Selection of Refractory Bricks for Carbon Baking Furnace
The selection of refractory bricks for carbon baking furnace needs to comprehensively consider factors such as temperature, atmosphere, mechanical load and chemical erosion:
- High temperature zone (>1300℃): Silicon carbide combined with silicon nitride bricks is an ideal choice, but the cost is relatively high.
- Medium temperature zone (800~1300℃): High alumina bricks have the best cost performance and need to control porosity.
- Carburization-resistant core: Low porosity (≤15%) + chemically inert material (such as SiC) is the key.
Therefore, when selecting refractory bricks, the specific operating conditions of the baking furnace must be fully considered. Under the continuous influence of high temperature, the temperature peak can rise to more than 1300℃, requiring the refractory bricks not to soften or melt.
Characteristics of Various Brick Types of Carbon Roasting Furnace
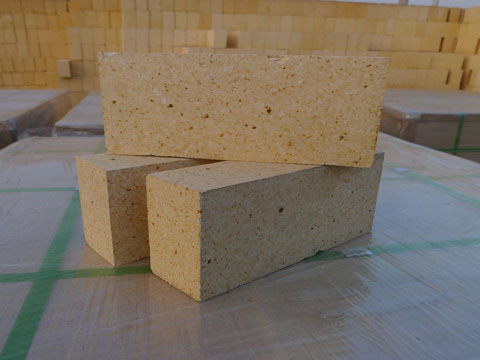
High Alumina Brick
Advantages: low cost, good high temperature resistance (refractory ≥ 1770℃).
Disadvantages: general thermal shock resistance, easy to crack under long-term thermal stress.
Applicable: furnace wall, furnace roof and other areas not directly impacted.
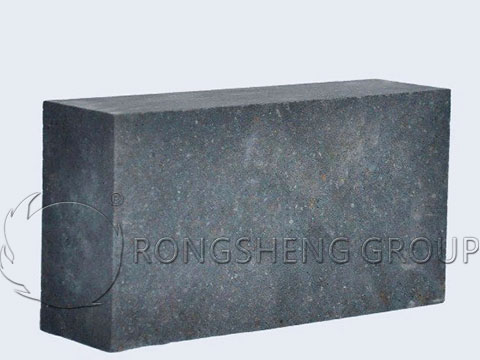
Silicon Carbide Brick (SiC)
Advantages: good thermal conductivity (15~20 W/m·K), strong thermal shock resistance, and resistance to CO/asphalt erosion.
Disadvantages: high price (3~5 times that of high-alumina bricks), slightly poor oxidation resistance at high temperatures (needs silicon nitride combined with SiC bricks for optimization).
Applicable to: high-temperature scouring areas such as fire channels and combustion chambers.
Lightweight Insulation Bricks
Advantages: low thermal conductivity (0.3~0.5 W/m·K), reducing heat dissipation of the furnace body.
Disadvantages: low strength, cannot be directly exposed to high-temperature flames.
Applicable to: furnace insulation layer, used in combination with high-alumina bricks or castables.
The performance of the carbon roasting furnace depends on the selection of refractory materials, temperature control, and maintenance management. Reasonable selection of refractory materials, such as high-alumina bricks and silicon carbide bricks, and optimization of roasting processes can significantly improve product quality and extend the life of the furnace body. The future trend is to develop in the direction of intelligence, low energy consumption, and environmental protection.