Semi-graphite carbon blocks of 500*400 are used to build the furnace bottom, and semi-graphite carbon blocks are used to surround the furnace bottom. Rongsheng manufacturer implements the physical and chemical indicators of pre-baked carbon bricks and the national standard YB/T2805-2006. Rongsheng refractory brick manufacturer can provide high-quality semi-graphite carbon bricks, furnace wall and bottom building carbon bricks, blast furnace carbon bricks, carbon brick caulking agents, electric paste, etc.

Semi-Graphite Carbon Blocks for Furnace Bottom Masonry
Specifications of Semi-Graphite Carbon Blocks for furnace bottom masonry. Prebaked carbon bricks, ash content ≤8%, volatile matter ≤2%. Compressive strength ≥32Mpa, apparent porosity ≤25%. Fixed carbon ≥85%, volume density ≥1.52g. Cm3, average pore size ≤2.4μm.
- Dimensions of carbon bricks for furnace wall and furnace bottom. Standard size, 400*400* (400-1800mm), 400*500* (400-2500mm), 600*650* (600-2000mm), 800*800* (800-1900mm). The length can be customized according to customer requirements. Various types and specifications of special-shaped carbon blocks, furnace mouth carbon blocks, etc. can be processed according to customer requirements.
- Packaging: Ordinary wooden pallet or export fumigation pallet packaging, straw rope, or steel belt packaging.
- Transportation: Choose truck or rail transportation according to customer requirements. The transportation is priced according to the prevailing transportation market price. The specific delivery location is different, and the transportation cost is different.
The carbon products operated by Rongsheng manufacturers include graphite carbon block products, self-cultivated pre-coated carbon blocks for various submerged arc furnaces, and anode carbon blocks for aluminum melting furnaces. Electricity, electric paste, carbon clay, cold ramming paste, and carburizing agent. Electric calcined coal, petroleum coke, activated carbon, silicon carbide products, etc.
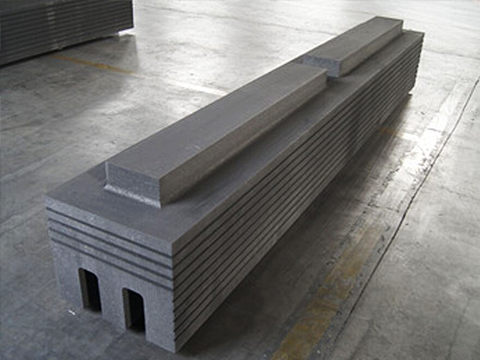
Carbon Bricks Production Process
Electric furnace carbon bricks use high-quality low-ash anthracite, graphitized metallurgical coke, graphite chips as aggregates, coal pitch, and a small number of additives as binders. It is produced through screening, batching, kneading, pressing, roasting, fine milling, machining, and other processes. Because carbon bricks are used as structural materials on large electric furnaces, they have a long service life. Therefore, we selected high-quality smokeless electric calcined coal with good heat resistance, high strength, and low ash content to improve the chemical stability of the carbon bricks. At the same time, at the high roasting temperature of 1250°C, the roasting quality is ensured and the excessive secondary shrinkage of the carbon bricks when used in the blast furnace is reduced. Rongsheng manufacturers can provide customers with self-baked carbon blocks, pre-baked carbon blocks, semi-graphite carbon blocks, etc. based on their actual needs.
Physical and Chemical Indicators of Graphite Carbon Blocks
- Prebaked carbon blocks for submerged arc furnaces. It is made from calcined anthracite and metallurgical coke as the main raw materials. Carbon blocks are used as furnace linings and conductive materials for submerged arc furnaces such as ferrosilicon furnaces, yellow phosphorus furnaces, silicon violent furnaces, and calcium silicate furnaces.
Physical and chemical indicators of prebaked carbon blocks
Items | Indicators |
Ash Content %, ≤ | 8 |
Volatile Matter %, ≤ | 1.5 |
Compressive Strength MPa, ≥ | 38 |
Apparent Porosity %, ≤ | 20 |
Fixed Carbon %, ≥ | 90 |
Bulk Density g/cm3, ≥ | 1.56 |
Average Pore Size μm, ≤ | 2.4 |
Sizes: 400*400, the length can be customized according to customer requirements. |
- Self-baking carbon blocks for calcium carbide furnaces. It is mainly made of high-temperature treated smokeless electric calcined coal as the main raw material and is made through a molding and high-frequency vibration molding process. Self-baking carbon blocks are used for building the bottom of large and medium-sized calcium carbide furnaces and the lining of the molten pool.
Physical and chemical indicators of self-baked carbon blocks
Items | Ash Content %, ≤ | Fixed Carbon %, ≤ | Residual Shrinkage (800℃) % | Compressive Strength MPa, ≥ | Bulk Density g/cm3, ≥ | Apparent Porosity %, ≤ | |
Block-1 | Before Baking | 7 | 84 | – | 21.6 | 1.64 | 10 |
After Baking | 8 | 91 | 0.05 | 32 | 1.58 | 21 | |
Block-2 | Before Baking | 9 | 82 | – | 19.6 | 1.62 | 15 |
After Baking | 10 | 88 | 0.10 | 29.4 | 1.55 | 25 |
Carbon brick processing dimensional deviation and appearance requirements standards
Dimensions: The height tolerance of the carbon bricks on the furnace bottom and furnace wall sides is ±3 mm, and the height tolerance is ±5 mm. For carbon bricks without free ends, the length tolerance is ±5 mm. The length tolerance of carbon bricks with free ends is ±10 mm.
Cracks: The cracks on the carbon bricks have a width of less than 0.5 mm and a length of less than 200 mm. There should be no more than two cracks on each side, and the length of each side of cross-edge cracks should not be greater than 100 mm.
Notches and bee holes: Individual notches and bee holes on the carbon bricks, with a width not exceeding 20 mm and a depth not exceeding 10 mm.
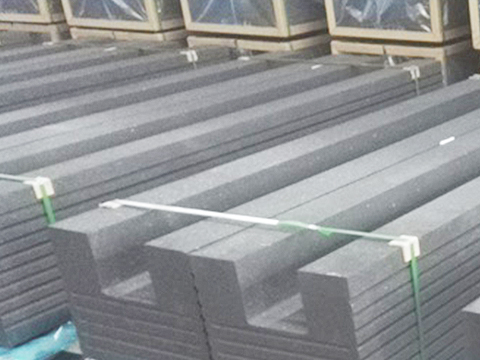
Semi-graphite carbon-silicon carbide carbon brick
In the production and development of semi-graphite carbon blocks, a unique green silicon component is used as an additive, which improves the conventional physical and chemical indicators of the carbon bricks and significantly improves the conventional working performance of the carbon bricks. The effect of additives is directly proportional to the degree of dispersion, and they are all added in differential form. After roasting and at working temperature, the role of the additive is that the reaction product between the additive and the carbon is oxidized in preference to the carbon, thereby protecting the carbon. In addition, the products of the reaction between the additives and other substances in the carbon block (asphalt, anthracene oil, graphite, carbon, etc.) change the microstructure of the product, fill the pores, and improve the density and chemical erosion resistance of the carbon block. The melt index, thermal conductivity, alkali corrosion resistance, oxidation resistance, and erosion and wear resistance of various high-temperature solutions have been improved step by step. The amount of residual shrinkage is effectively reduced, and the overall quality of the carbon block is close to and reaches the quality level of foreign high-quality carbon blocks.
Rongsheng Semi-Graphite Carbon Blocks Sales
Rongsheng Manufacturer is a refractory material manufacturer with rich production and sales experience. Our refractory products have been sold to more than 100 countries around the world, such as South Africa, Chile, Egypt, Colombia, Uzbekistan, Italy, Indonesia, Ukraine, Hungary, Spain, Kenya, Syria, Zambia, Oman, Venezuela, India, Peru, the United States, Ethiopia, etc. The quality of our products has been recognized by customers for a long time, and customers can continue to purchase from us. Moreover, our perfect customer service also includes after-sales service for our products. To ensure the effectiveness of customers’ high-temperature furnace linings and extend the life of refractory furnace linings. This further reduces the number of furnace shutdowns and furnace repairs, saves production costs, and improves economic benefits.