Silicon carbide bricks are refractory materials made of SiC as the main raw material, containing 72% to 99% SiC. They are divided into clay-bonded, Si3N4-bonded, Sialon-bonded, β-SiC-bonded, Si2ON2-bonded and recrystallized silicon carbide bricks. Silicon carbide bricks have high thermal conductivity and good wear resistance, thermal shock resistance and corrosion resistance. They can be used for linings of aluminum electrolytic cells, molten aluminum conduits and kiln furniture for ceramic kilns, the lower part of large and medium-sized blast furnaces, furnace waists and belly, aluminum refining furnace linings, zinc distillation tank linings, etc.
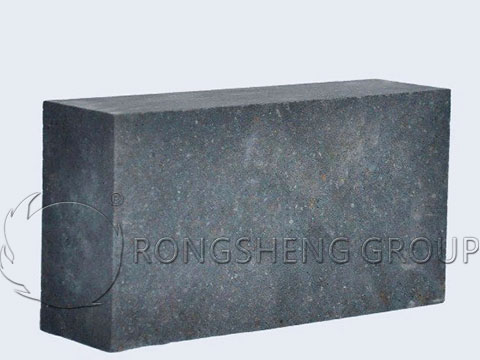
How to Judge the Quality of Silicon Carbide Bricks?
The size specifications of silicon carbide bricks should be precise. The specific gravity of silicon carbide bricks is generally between 2.45-2.6. If the specific gravity is too small or too large, it means that the material itself is not pure. Other refractory materials must be added, which greatly affects the silicon carbide content and the heat transfer performance of silicon carbide. When purchasing silicon carbide bricks, check whether there are corners and cracks on the surface of the bricks. The corners and cracks should be acceptable within the national standard. If they seriously exceed the national standard, the quality of this batch of products is unqualified.
How Should Silicon Carbide Bricks be Used?
Among the core raw materials in the field of refractory materials, silicon carbide is also one of the important raw materials for firing refractory bricks and refractory castables. When silicon carbide is used as a refractory raw material, it has good thermal shock resistance and can withstand rapid changes in temperature. Therefore, it can prevent cracks or breaks in the furnace lining. And because of its high hot strength, it can also withstand certain stress under medium and high temperature conditions and can be used as a structural material. When silicon carbide is used in a reducing atmosphere, the temperature it withstands can generally reach about 1760°C, and it has good wear resistance and can be used as a wear-resistant lining.
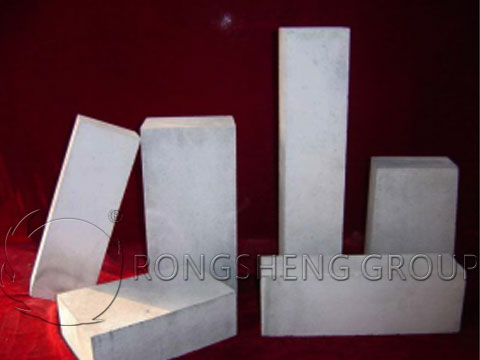
Generally speaking, silicon carbide is used to make various refractory materials that meet the requirements, and is mainly used in the following industries:
Metal smelting industry
Silicon carbide is mainly used as lining material for smelting high-temperature equipment in the non-ferrous metal smelting industry. For example, zinc distillation tower trays, aluminum electrolytic cell side wall refractory bricks, etc. The main characteristics of silicon carbide are high thermal stability and thermal conductivity; it will not be infiltrated by non-ferrous metals, and it has good corrosion resistance and high thermal conductivity.
Steel industry
Since silicon carbide is resistant to slag and molten iron, alkali metal corrosion, wear resistance at high temperature, good erosion resistance and can increase the life of the container, it can be used as refractory bricks for cooling walls of iron-making blast furnaces, combined refractory bricks for furnace belly and tuyere, lining materials for ladle and torpedo tanks, and lining materials for iron outlet grooves in the steel industry. It can also replace ferrosilicon as a deoxidizer, etc.
Kiln industry
It is mainly used in ceramic firing kilns, used as shelves, saggers, pads, columns, etc. Its characteristics are that due to its high high-temperature strength, the cross-section of the components is reduced, the effective volume of the kiln car is increased, and the heat capacity is reduced. It has good thermal shock resistance and is not prone to cracks or breaks. Its service life is significantly longer than that of ordinary clay refractory bricks.
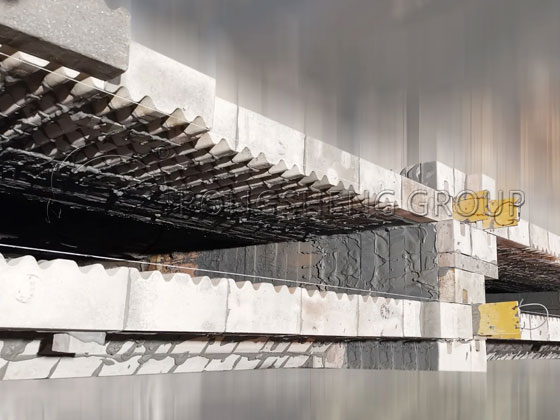
Silicon Nitride Bonded Silicon Carbide Bricks for Vertical Zinc Smelting Furnace
Vertical zinc smelting is an important zinc smelting process. The outer side of the vertical zinc smelting furnace is in direct contact with the high-temperature flame of 1 300~1 340 ℃, and the inner side is in direct contact with zinc vapor and slag with a maximum temperature of 1 200 ℃. It is subjected to high temperature, oxidation, thermal shock, scouring, chemical erosion and other effects. In addition, it is necessary to perform suspended ore operations from time to time to remove furnace tumors and iron accumulation. Moreover, the added coke is only about 800 ℃, which makes the material subject to greater thermal stress. The service life of clay bonded silicon carbide bricks, which are widely used at present, is about 20 months.
Silicon nitride bonded silicon carbide materials have the advantages of high thermal conductivity, corrosion resistance, and scouring resistance. A zinc industry has successively used silicon nitride bonded silicon carbide bricks instead of clay bonded silicon carbide bricks in 7 vertical zinc smelting furnaces, and the application effects are as follows.
Application Effect of Silicon Nitride bonded Silicon Carbide Bricks Instead of Clay bonded Silicon Carbide Bricks
- (1) Compared with clay bonded silicon carbide, silicon nitride bonded silicon carbide has higher thermal conductivity, and the temperature control in the high temperature zone is reduced by about 30 ℃ during service.
- (2) The corrosion resistance of silicon nitride bonded silicon carbide is stronger than that of clay bonded silicon carbide. After 20 months of service, the thickness of the remaining bricks in the high temperature zone is 40~50 mm larger than that of clay bonded silicon carbide.
- (3) During the service process, silicon nitride bonded silicon carbide bricks will continuously produce leaks and long cracks due to the inadequate release of thermal stress. This problem can be solved to a certain extent by adjusting the temperature system during the suspended ore drilling. If a more efficient leak repair technology can be developed in the later stage, it is expected to increase the service life of silicon nitride bonded silicon carbide bricks.
In view of the problems that occurred in the initial application of silicon nitride combined with silicon carbide in the vertical tank zinc smelting industry, optimization was carried out from the aspects of adjusting the thermal system, adjusting the material composition, optimizing the brick type, and improving the spraying method. The specific measures are as follows:
- Adjust the thermal system. The thermal system during the suspended ore operation was adjusted to reduce the heating rate and extend the heating time, which solved the problem of long cracks that are prone to appear during the suspended ore operation.
- Adjust the material composition to improve the thermal shock resistance of the product. The ratio of coarse silicon carbide particles was increased, the product density was reduced, and the appropriate amount of liquid phase was introduced to buffer the thermal stress and microcrack repair theory, which significantly improved the thermal shock resistance of the product. At the same time, the increase in the content of coarse particles significantly improved the interface bonding state between the brick surface and the spraying repair material, which is more conducive to the subsequent repair of the leak point.
- Optimization of brick type and masonry structure design. Introduce curved expansion joints and appropriately increase the size of the expansion joints. When the vertical tank masonry is subjected to thermal stress during use, the original design of thermal stress is easily concentrated to cause microcrack expansion. The overall structure remains stable.
- Improve the gunning method. The original wet gunning method for repairing leaks was optimized to fire gunning, and raw materials and special gunning equipment suitable for fire gunning were developed.
Buy high quality silicon carbide bricks, silicon nitride bonded silicon carbide bricks, please contact Rongsheng manufacturers. Get free samples and quotes.