Rongsheng Methods of Increasing the Service Life of Silica Bricks in Glass Melting Furnaces. Traditional and new refractory materials are used for glass kiln construction and repair. Traditional refractory materials for industrial use include clay bricks, dense clay bricks, mullite silica bricks, mullite bricks, mullite corundum bricks, and corundum bricks. High-temperature insulation materials and high-purity magnesium spinel refractory materials. Unshaped refractories include plasticized aluminum silicate cement, high-alumina cement, and low-cement castables. Silica Bricks for the Glass Kiln, The use of refractory materials in glass melting furnaces. Silica bricks are widely used in glass-melting furnaces, and the main component is silicon dioxide (SiO₂).
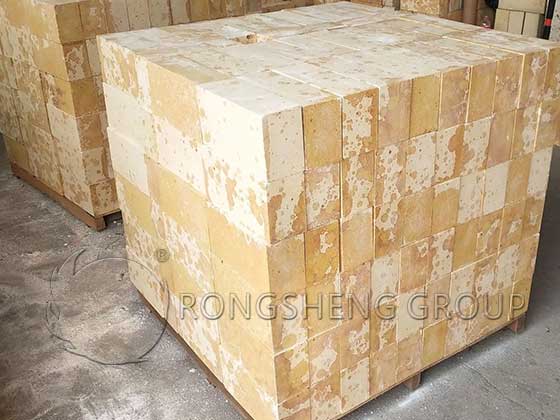
The silica brick used in the glass melting furnace requires a SiO₂ content of 94% or more, a maximum operating temperature of about 1600~1650℃, and a density of 1.8~1.95g/cm³. The apparent porosity is required to be less than 22%. The larger the porosity, the worse the quality of the silica brick. The appearance of silica bricks is mostly white crystals, and the microscopic composition is tridymite crystals. Because silicon bricks undergo crystallization conversion and volume expansion at high temperatures, especially at 180~270℃ and 573℃, the crystallization conversion becomes more intense. Therefore, in the process of baking kiln and cold repair, it is necessary to adapt to the crystal transformation of silica bricks and take appropriate measures such as elastic strips. The silicon brick masonry should be left with expansion joints. Rongsheng Silica Bricks for Sale.
How to Improve the Performance of Silica Brick in a Glass Kiln
The advantages of siliceous materials are high-temperature strength, good creep resistance, low density, no pollution to glass, and low price. The working temperature of silica bricks is about 200℃ higher than that of clay bricks, but the corrosion resistance to molten glass and alkaline flying materials is poor. Therefore, it is used for masonry structures such as masonry, parapets, and small furnaces. When masonry, use high-silicon refractory mud or silica brick powder and other materials close to the composition of silica bricks as the cementing material. RS High-Quality Silica BricksWays to Improve the Life of Silica Bricks. In the 1980s, my country introduced advanced silicon brick manufacturing technology for glass kilns from the United States. In order to distinguish it from the original product, the product manufactured with imported technology is called high-quality silica brick.
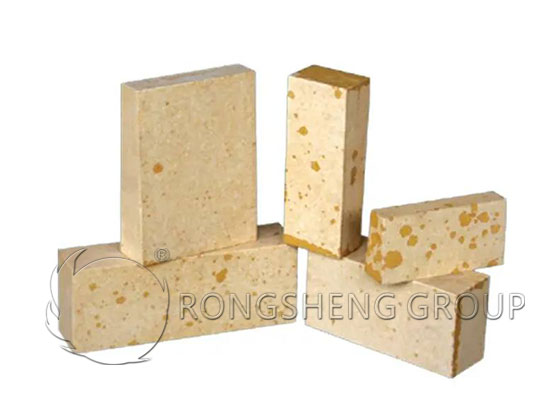
How to Distinguish High-Quality Silica Brick from the Original Product
The composition (W) of high-quality silica bricks is cristobalite 45%, phosphorite 50%, glass phase 1%~2%, and a small amount of residual quartz. Melt index (2R2O+Al2O3)<0.5%.After adopting oxy-fuel combustion technology, the life of silica bricks has been drastically reduced from 5 to 10 years to 2 to 3 years. Rat holes and erosion are the main causes of damage. The rat-hole is caused by the alkali in the gas leaking from the kiln condensing in the cracks of the brick to corrode the silica brick. The methods to improve the life of silica bricks are as follows:1) Improve the dimensional accuracy of bricks. Control size tolerance <0.5mm, brick gap width <1.5mm. The cracks between the bricks are narrowed, the kiln gas leaks less, the erosion is light, and the mouse hole is also small.2) Reasonably design the kiln lining structure. Move the condensation temperature zone of the alkali to the sealing layer behind the silica brick.3) Use low-calcium silica bricks with good corrosion resistance (w(CaO)≈0.8%). Figure 4 shows the corrosion resistance test results of low-calcium silica bricks and high-quality silica bricks. It can be seen from Figure 1 that when the alkali vapor pressure is low, the corrosion resistance of low-calcium silica bricks is better than that of high-quality silica bricks.
Cheap Silica Refractory Brick for Sale, The Influence of Alumina Content on the Performance of Silica Brick for Glass kilnThe increase of Al2O3 content is unfavorable to the refractoriness, softening temperature under load, true density, and mineral composition of the product. However, it has no obvious influence on the apparent porosity, residual line change, and creep rate. Development of High-Purity, Corrosion-Resistant Glass Kiln Silica Brick China’s glass output has ranked first in the world. The main task for the future development of refractory materials for glass kilns is to improve the design, masonry, and maintenance of the kiln, reduce the adverse effects on the quality of glass, and extend the service life of the glass kiln. Silica brick is the main refractory material in the masonry of the glass furnace and is mainly used for the ceiling, hanging wall, and front and back walls of the glass furnace.
To increase the service life of glass furnaces, higher requirements must be put forward on the quality of silica bricks. Therefore, the study of high-quality silica bricks for glass kilns with high purity and corrosion resistance can extend the service life of glass kilns to a certain extent.
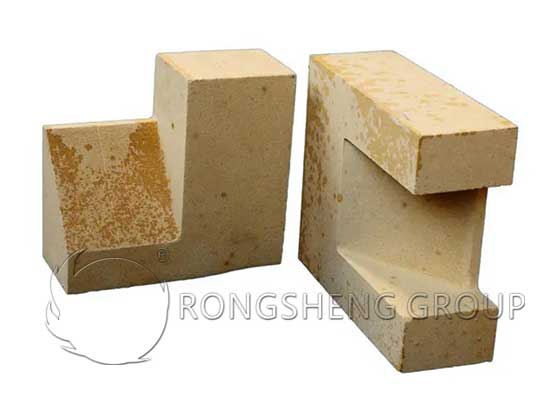
RS Refractory Bricks Factory Silica Brick For Glass Kiln
Silicon brick is the most commonly used refractory for glass furnaces in the structure of glass tank furnaces. At present, silicon brick is developing towards high purity, low porosity, and no untransformed quartz crystal. Since the highest melting point of SiO2 crystal is 1725℃, the refractory of silicon brick cannot exceed this temperature. With the increase of melting temperature, the silicon brick is likely to be replaced by fused cast refractory material with higher refractory and better corrosion resistance.
However, silicon brick is still a very good refractory material when used in pool furnaces with a melting temperature of no more than 1630 ℃. The main advantages of silicon brick are 1. High softening temperature under load. The softening temperature of high-quality silicon brick under load can reach 1705℃, and that of general silicon brick can reach 1630℃;.2. Good shock resistance in high temperatures. The volume of the silicon brick will hardly change above 700℃, so the temperature fluctuation above 700℃; will not cause damage to the silicon brick.3. The components are easy to melt and diffuse in the glass, and have little pollution to the glass liquid. The main component of silicon brick is SiO2, which is the main component in general glass. Therefore, the eroded material of silicon brick is easy to melt and diffuse in the liquid glass, thus the formation of stones and stripes is less than that of other bricks.4. Low price and easy to manufacture. The glass kiln brick should be stored in a waterproof warehouse. It can still be used after being wet with water and slowly dried at a temperature below 100℃. The strength of water-bearing silicon brick is affected after freezing, and it needs to be checked again after drying. Expansion joints shall be set aside according to the expansion rate provided by the manufacturer.
Oven or periodic use of temperature for a time curve should be reasonable, to be specific before 600℃, and expansion intense to be strictly controlled. The quality of the mud used in bricklaying should be appropriate to the bricks. Sometimes brick damage is due to the erosion of the brick joints leading to alkali vapor injection.In order to improve the melting temperature and extend the whole life of the furnace, some glass factories have changed the furnace mouth and parapet into fused cast brick, and some have changed the arch or part of it into other materials. The consumption ratio of silicon bricks may be small, but silicon bricks have the advantages of high softening temperature under load, lightweight, and low price. The glass kiln arch and part of the furnace superstructure will still use silicon bricks.
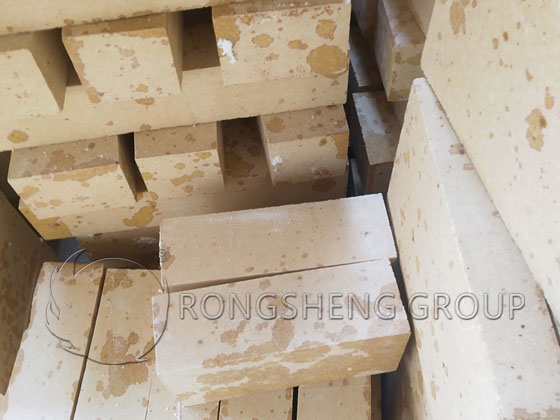
High-Quality Silica Bricks in Glass Kiln
Therefore, it is still important to improve the quality of silica bricks in glass kilns. We are a high-quality silicon brick manufacturer, the quality is stable and reliable, the price is reasonable, has reached friendly cooperation relations with domestic and foreign customers, welcome everybody to come to consult to purchase, and we will wholeheartedly serve you. Email Us: sales@cheapfirebricks.com.
Rongsheng Refractory Brick Manufacturer is an experienced refractory material manufacturer and sales manufacturer. Rongsheng Refractory products have been sold to more than 60 countries and regions all over the world. For example, Russia, South Africa, Kazakhstan, Philippines, Chile, Malaysia, Uzbekistan, Indonesia, Vietnam, Kuwait, Turkey, Zambia, Peru, Mexico, Qatar, etc. Obtain high-quality refractory products for glass kilns, such as AZS bricks, silica bricks, fused corundum bricks, checker bricks for regenerators, etc. Please contact us, we will provide you with services according to your specific needs.