Lightweight thermal insulation refractory bricks can be divided into clay, siliceous, aluminum, and mullite according to the different raw materials used. The reason why lightweight thermal insulation refractory bricks can be insulated is that the bricks contain a small number of pores (including open pores and closed pores). Lightweight thermal insulation refractory brick, good thermal insulation performance, high-temperature resistance, suitable for the thermal insulation layer and thermal insulation layer of masonry industrial kilns. The lightweight thermal insulation refractory bricks used for the thermal insulation layer of industrial kilns can not only reduce the weight of the furnace body but also shorten the kiln time. It can also reduce thermal diffusion and maintain uniform furnace temperature. To buy high-quality lightweight thermal insulation refractory bricks, please contact Rongsheng refractory brick manufacturers, ex-factory price, and fast delivery.
Lightweight clay insulation brick
Clay thermal insulation bricks are thermal insulation refractory products with AL2O3 content of 30%-48% made of refractory clay as the main raw material. Its production process adopts the burn-out addition method and foam method. Using refractory clay, floating beads, and refractory clay clinker as raw materials, adding binder and sawdust, through batching, mixing, molding, drying, and firing, a product with a bulk density of 0.3-1.5g/cm3 is prepared. The output of clay insulation bricks accounts for more than half of the total output of insulation and refractory bricks. The Chinese standard (GB3994-1983) divides clay insulation bricks into NG-1.5, NG-1.3a, NG-1.3b, NG-1.0, NG-0.9, NG-0.8, NG-0.7, NG- 0.6, NG-0.5, NG-0.4, 10 grades. Lightweight clay insulation bricks have a wide range of applications and are mostly used in thermal equipment and thermal insulation layers of industrial kilns.
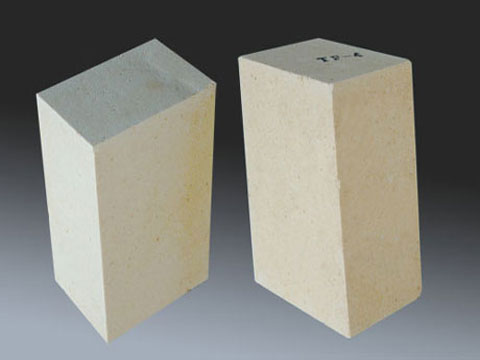
Lightweight silica brick
Lightweight silica bricks are also called silica heat-insulating bricks. It is a lightweight refractory material with a silica content of more than 91% and a bulk density of less than 1.2g/cm3. The refractoriness and softening temperature under load is not much different from ordinary silica bricks with the same composition. However, due to a large number of pores, the compressive strength, slag resistance, and corrosion resistance are not as good as ordinary silica bricks, but the thermal shock resistance is improved.
Using finely divided silica as raw material, the critical particle size is usually not more than 1mm, and the particles smaller than 0.5mm are not less than 90%. Add flammable substances to the ingredients or use the gas generation method to form a porous structure, which is obtained by firing. Can also be made into non-fired products. It is mainly used in various parts of the kiln that require heat insulation or weight reduction without direct contact with the melt, without the action of corrosive gases, and without sudden temperature changes. It can be used at high temperatures and cannot be in contact with basic refractory materials. According to different materials, the operating temperature is 1200-1550℃.
Lightweight silica brick is a very special material, mainly used in the glass industry and steel industry. In most cases, lightweight silica bricks and dense silica bricks are used as part of the structural layer. Commonly used in the glass kiln industry, mainly the insulation of the kiln vault, thereby reducing heat loss and increasing the efficiency of the melting process. In the steel industry, lightweight silica bricks are used as a lightweight thermal insulation layer for hot blast stove walls and domes.
-
Lightweight silica bricks are used in the glass industry – thermal insulation of furnace vaults
During the glass melting process, very high temperatures are reached in the raised lower part of the dome. Depending on the type of glass, the temperature is around 1600°C. Lightweight layers are usually designed as two or more layers.
Lightweight silica bricks are primarily exposed to these temperature loads. It is expected that the single layers of the vault (structural and lightweight layers) have the same or similar expansion properties. Silica bricks with a bulk density of 1250kg·m-3 or 1000kg·m-3 can meet the requirements of the dense layer. The next layer uses silica bricks with a bulk density of 800kg·m-3 or 600kg·m-3.
Lightweight silica bricks can be freely stacked on the furnace arch or bonded with silica fire clay. There is no chemical load during the furnace service period (several years). Lightweight silica bricks are mainly used because the chemical and mineral composition of the working linings is similar to dense silica bricks.
-
Lightweight silica bricks are used in the steel industry – hot blast stove
Hot blast stoves are often used for hot blasts (called blast furnace blasts). This is connected with the blast furnace’s air extractor, and it varies according to the shape and location of the hot blast furnace. The temperature range is between 1000~1300℃, and the hot air is in the range of 2300~6500m3·min-1.
This entails calculating a comparison between hot blast stoves (different component sizes and locations of use) and glass kiln vaults at different levels and loads with an emphasis on thermomechanical performance. For lightweight layers, bulk densities of 1250 kg·m-3 or 1050 kg·m-3 are used (mainly due to their higher strength).
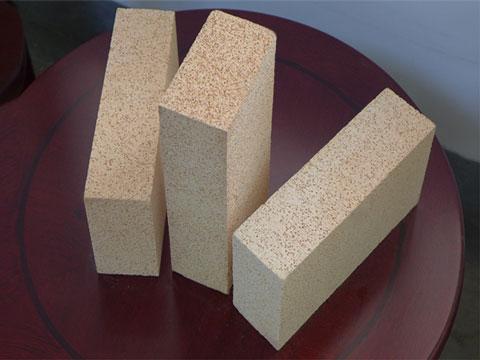
High alumina poly light brick
High-alumina poly-light insulation brick is also called high-alumina poly-light ball brick, lightweight high-alumina brick. It is produced with super-grade blast furnace charge as the main raw material, supplemented by appropriate admixtures using the polylight loss-on-ignition method. The product has the advantages of high strength, good thermal stability, little change in reburned fiber, and small thermal conductivity.
High-alumina polylight insulation bricks usually use high-alumina bauxite clinker and a small amount of clay. After grinding, it is cast in the form of mud by gas generation method or foam method and fired at 1300-1500 ℃. Sometimes industrial alumina can also be used to replace part of the bauxite clinker. It is used for the lining and heat insulation layer of masonry kilns, as well as the parts where there is no strong high-temperature molten material erosion and scouring. When in direct contact with the flame, the surface contact temperature shall not be higher than 1350℃.
Product characteristics of high-alumina polylight insulation bricks
1. High-temperature strength; 2. Good thermal insulation performance; 3. Corrosion resistance in various atmospheres; 4. Significant energy saving effect; 5. Excellent thermal shock stability performance.
Application of high alumina polylight insulation brick
High-alumina polylight bricks are widely used in furnace linings (not eroded by solutions) and thermal insulation layers in metallurgy, machinery, ceramics and chemical industries. It is an ideal energy-saving product, and its operating temperature is below 1350 ℃.
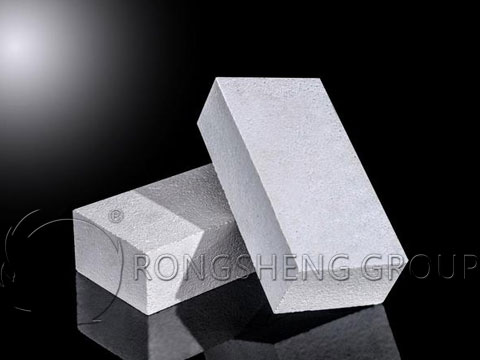
Mullite insulation brick
Lightweight mullite insulating bricks are heat-insulating refractory products made of mullite as the main raw material. Mullite thermal insulation bricks are resistant to high temperature, high strength, and low thermal conductivity, and can be directly contacted with flames. They are suitable for the lining of various industrial kilns.
Mullite insulation bricks are also classified according to different densities and are divided into light mullite insulation bricks and heavy mullite insulation bricks. According to the temperature of use, it is divided into 1350 mullite insulation brick, 1450 mullite insulation brick, and 1550 mullite insulation brick. 1550 mullite insulation bricks and above, etc., are generally used as bricks such as fire pits because the heat-resistant temperature is high.
The performance of mullite insulation bricks. High refractoriness, can withstand the high temperature of 1800 ℃. But at 1600 to 1700 degrees Celsius, mullite insulation bricks will begin to soften and will not burn. However, its normal temperature compressive strength is also high, ranging from 70 to 260MPa, and its thermal shock resistance is good. Mullite insulation brick is a new type of refractory material in my country, which can directly contact the flame, and has the characteristics of high-temperature resistance, high strength, low thermal conductivity, and remarkable energy-saving effect.
Mullite insulation brick is suitable for cracking furnaces, hot blast furnace, ceramic roller kiln, electric porcelain drawer kiln, glass crucibles, and the lining of various electric furnaces. It is used for the top of the hot blast furnace, the shaft and bottom of the blast furnace, the regenerator of the glass melting furnace, ceramic sintering kiln, furnace lining of petroleum cracking system, etc. Mullite insulation brick also has the characteristics of high load softening temperature, compact structure, low porosity, and good corrosion resistance.
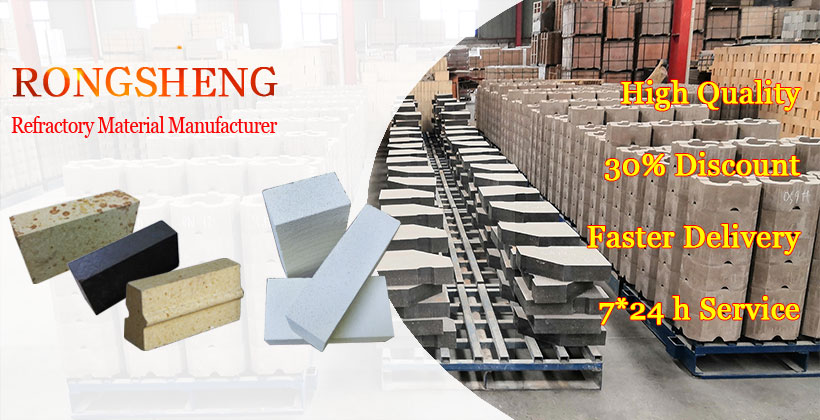
Through the above introduction of Rongsheng refractory bricks to lightweight thermal insulation refractory bricks, I believe we have a certain understanding of the choice of kiln thermal insulation bricks. Then you will not feel confused when purchasing high-alumina lightweight thermal insulation bricks, high-alumina poly-light bricks, lightweight high-alumina bricks for tunnel kilns, high-alumina thermal insulation refractory bricks, and energy-saving, high-temperature-resistant high-alumina poly-light bricks. Choose a strong refractory brick manufacturer, and the product quality is more guaranteed.