The glass industry is a high-energy consumption industry. The glass melting furnace is the most energy-consuming equipment in the glass production line. The fuel cost accounts for about 35% to 50% of the glass cost. Most of the float glass melting furnaces designed in my country can consume 6500kJ/kg to 7500kJ/kg of molten glass per unit. Large foreign float glass companies only have 5800kJ/kg glass liquid. There is a certain gap between us and the international advanced level.
The thermal efficiency of glass-melting furnaces in developed countries is generally 30% to 40%, while the average thermal efficiency of glass melting furnaces in my country is only 25% to 35%. Unreasonable furnace structural design and insulation measures, as well as low-quality refractory materials used, are one of the important reasons for this gap. Secondly, the domestic float glass process operation technology is backward and management is not perfect, which are also the reasons for high energy consumption, poor melting quality and short furnace life.
So far, my country has more than 140 float glass production lines. Glass production capacity is increasing rapidly, and market competition is gradually becoming fiercer. As the main fuel for glass, the price of heavy oil continues to rise, accounting for an increasing proportion of the cost of glass. Therefore, reducing glass energy consumption is of great significance to reducing production costs, improving the market competitiveness of enterprises, reducing environmental pollution, and alleviating energy shortages.
Energy saving in glass enterprises is a long-term task, and technical personnel at home and abroad are actively conducting research. Such as optimizing the furnace structure design, oxygen-rich combustion, full oxygen combustion electric boosting, heavy oil emulsification technology, etc. At present, many companies have begun to implement energy-saving measures in the production process and are exploring energy-saving measures in glass production process control and other aspects.
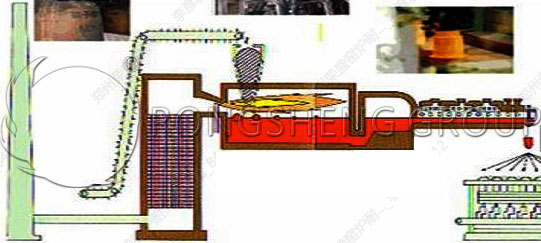
Glass Kiln Energy-Saving Methods
The proportion of broken glass.
Cullet is an inevitable product of glass production and an indispensable glass raw material. Crushed glass and batch materials are evenly mixed and added to the melting furnace in a certain proportion, which can play a better role in promoting melting. According to reports, melting 1kg of cullet and raising the temperature to 1500°C requires about 1460kJ of heat. Melting the same amount of soda-lime-silica glass requires 2300kJ to 2510kJ heat. Therefore, using as much broken glass as possible within a reasonable range will have a certain effect on reducing fuel consumption. Through practice, it is believed that for a furnace with a capacity of 400 tons/day to 600 tons/day, if the proportion of cullet glass changes to 2%, the fuel consumption can increase or decrease by 0.1 tons/day to 0.5 tons/day.
Reasonable melting temperature regime.
A reasonable melting temperature system can not only improve melting quality but also reduce glass defects. At the same time, it can also achieve the purpose of saving energy, reducing consumption and increasing the kiln life.
There are generally three types of temperature curves for float glass melting furnaces, namely “mountain” shape, “bridge” shape and “double height” shape curve. The “mountain” shaped curve is the temperature curve mainly used by domestic flat glass factories in the past, and is characterized by prominent hot spots. The temperature difference between the hot spot and the 1# small furnace and the last pair of small furnaces is large. The disadvantage is that it is difficult to fully utilize the potential of the melting furnace. The “bridge” shape curve is similar to the “mountain” shape. Its characteristic is that the temperature between the small furnaces before and after the hot spot is not much different from the maximum temperature. The melting high temperature zone is longer, which is beneficial to improving the melting speed of the glass batch and the clarification of the glass liquid.
The above two temperature curves are detrimental to energy saving and furnace life.
The “double high” curve is the “double high heat load” temperature system. Its characteristic is that more fuel is put into the 1# and 2# small furnaces with more batch materials to enhance the melting of the batch materials. Reduce the amount of fuel in the 3# and 4# small furnaces in the foam area and reduce the heat load here. Increase the amount of fuel in the 5# small furnace to facilitate the high-temperature clarification and homogenization of the glass liquid. 6# serves to adjust the molding temperature as needed. Because the “double height” curve distributes fuel properly, fuel consumption can be reduced. However, when using the “double-height” curve, the degree of concentration and dispersion of the oil volume must be grasped. Excessive concentration will cause the furnace burning loss to increase.
A comparison of the actual consumption of two temperature curves of a 600 ton/day melting furnace in a domestic factory verifies the above point of view. The consumption for the “bridge” curve is 74.6kg/min, and the consumption for the “double height” curve is 71.4kg/min. Furnace sealing Whether the sealing of the melting furnace is intact or not has a greater impact on fuel consumption. The expansion joints in various parts of the furnace generally need to be sealed after the kiln is completed. If the sealing is not good, a large amount of heat energy will be dissipated through these gaps on the one hand. On the other hand, a large amount of outside cold air will be sucked in from the gaps between the pool wall and breast wall, flue, regenerator, etc., resulting in a waste of fuel. A domestic factory’s 400 tons/day float glass production line caught fire due to the large gap between the tank wall and breast wall. At the same time, a large amount of cooling air from the tank wall continued to enter the kiln through the gaps, and the heavy oil consumption reached about 83 tons/day. By sealing the tank wall gap, heavy oil consumption is reduced to approximately 76 tons/day. This shows the importance of furnace sealing for energy saving.