Around 1975, magnesia spinel bricks began to be used in cement kilns. Japan is the first country to apply magnesia spinel bricks in cement kilns to deal with the chromium hazards caused by magnesia chrome bricks. Magnesium spinel bricks not only have excellent thermal shock stability but also chemically react with cement clinker. A protective film is formed on the surface of the magnesia spinel brick, which can prevent the liquid phase from diffusing into the interior of the magnesium spinel brick. Therefore, the spalling resistance of magnesia spinel bricks is better than that of magnesia chrome bricks.
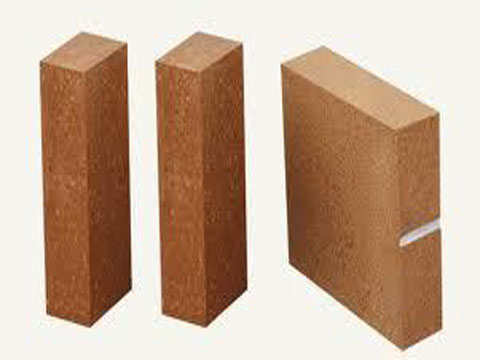
Advantages of Magnesia Spinel Bricks for Cement Kiln
Due to the harsh operating conditions of cement kilns, the lining bricks tend to shorten their lifespan. The magnesia spinel bricks exhibit good durability under harsh conditions, realize stable operation, and have cost advantages.
In the firing zone with the highest heat load, magnesia chrome bricks with good corrosion resistance and coating adhesion have been widely used. But now due to the improvement of environmental protection awareness, magnesia-chrome bricks have basically disappeared from cement kilns, and magnesia spinel bricks are mainly used in the cooling zone, firing zone, and transition zone. The burning zone is the area with the highest heat load in the cement rotary kiln, and the highest temperature is 1450℃. As a magnesium spinel brick for the firing zone, considering the corrosion resistance and thermal shock resistance, the Al2O3 content is optimized. In order to improve the adhesion of the coating and further improve the corrosion resistance, a small number of special ingredients are added.
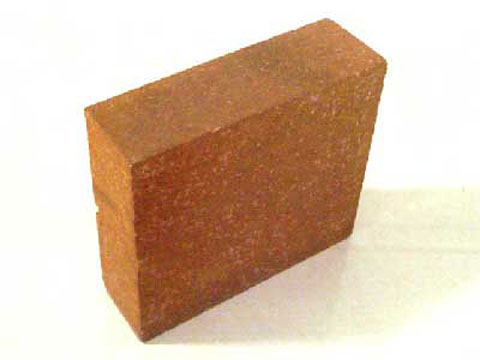
Problems of Magnesium Spinel Bricks in the Operation of Cement Rotary Kiln
Although to a certain extent, magnesia-chrome bricks can be replaced by magnesia spinel bricks and used in cement rotary kilns. However, there are still some problems with magnesia spinel bricks. The rotary kiln has a diameter of 4.2m and a length of 58m. The lining materials used to be magnesia chrome bricks, magnesia spinel bricks, high alumina bricks, etc. The average service life of the fired zone refractory bricks is less than 8 months, the maintenance and replacement cycle is frequent, and the cost of refractory materials is relatively large. Moreover, the surface temperature of the rotary kiln is too high (up to 320~350℃), which exceeds the design specification (≤280℃). Increase the energy consumption of the operation, cause energy waste, and also pose a greater safety hazard to mechanical equipment. After the furnace was shut down, it was found in the kiln that the fired zone had the most serious corrosion of refractory bricks with obvious radial cracks on the surface.
- (1) The ability to hang kiln skins is weak. Refractory bricks will be severely chemically attacked, thereby reducing the application time of the brick body.
- (2) Increase the heat loss of the cement kiln body and increase heat consumption, resulting in a waste of materials.
- (3) Under high-temperature conditions, a low melting point mineral phase is generated inside the magnesia spinel brick. Magnesium spinel bricks are susceptible to severe chemical attack and damage.
- (4) Magnesia spinel bricks can easily undergo hydration reactions.
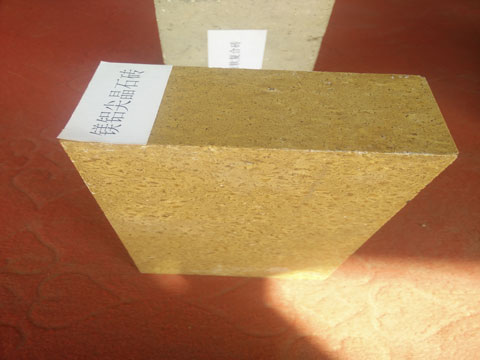
Improvement measures to improve the performance of magnesia spinel bricks in the operation of cement rotary kiln
Therefore, in order to prolong the service life of refractory bricks, improvement can be made from two aspects: its kiln-hanging performance and anti-stripping performance. Among them, the method of improving magnesia spinel brick has the following measures.
- (1) Add additives to the magnesium spinel. For example: TiO2, Fe2O3, ZrO2, etc. Adding additives is very beneficial to the firing of materials, the decrease of apparent porosity, the enhancement of chemical resistance, and the improvement of kiln skin hanging ability.
- (2) Appropriately reduce the content of magnesium spinel, so that there are micro-cracks inside the brick. Thereby reducing the thermal conductivity and improving the peeling resistance.
- (3) The study found that when the content of alumina in refractory bricks is less than 10%, the kiln-hanging performance of the bricks is better. Therefore, by reducing the alumina content in the magnesia spinel bricks, the kiln-hanging ability of the material is improved.
The operating state of the rotary kiln is that the entire kiln body is in a rolling motion. In order to reduce the load of mechanical operation, the thickness and total weight of the lining of the rotary kiln are restricted. In order to avoid the influence of the high surface temperature of the furnace shell on the furnace machinery and the waste of energy, it is required that the furnace lining must be made of thermal insulation materials to ensure thermal insulation performance. In the application of cement rotary kiln, magnesia spinel bricks with high strength, excellent thermal shock stability, and strong chemical resistance are mainly used. It is mainly used in the upper and lower transition zone of cement rotary kiln and thermal kiln equipment that requires high temperature and heat shock resistance.
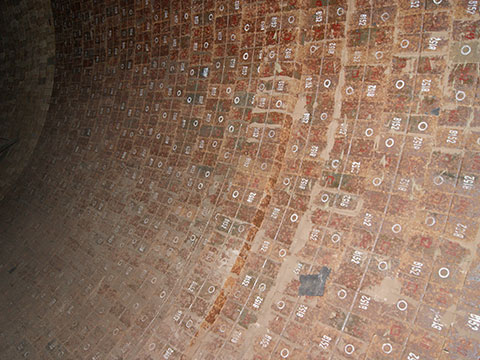
Rongsheng Refractory Bricks Manufacturer
Rongsheng refractory material manufacturer is an experienced cheap refractory bricks material manufacturer. Rongsheng’s refractory products have been applied to more than 60 countries around the world. For example, Vietnam, Laos, Thailand, Myanmar, Malaysia, Singapore, Indonesia, Philippines, Turkey, Kuwait, South Africa, Egypt, Russia Uzbekistan, etc. We have rich experience in solving the problem of refractory lining of cement rotary kiln. In addition to magnesia spinel bricks, we also provide high-quality silica mullite bricks, magnesia bricks, high alumina bricks, and other refractory brick products. In addition, our brand new fully automatic monolithic refractories production line has an annual output of 80,000 tons. It can provide high-quality wear-resistant refractory castables and plastics for rotary kilns. If you need to buy magnesia spinel bricks and get the cheap price of silicon mullite bricks for free, please contact us. We will reply to you in the shortest time according to your specific needs.