It is not acceptable to use ordinary phosphate wear-resistant bricks for the firing zone of the lime rotary kiln. Because the body density of ordinary phosphate wear-resistant bricks is about 2.6, if it is used in the firing zone, the degree of temperature erosion is not suitable for ordinary bricks, and phosphate composite bricks with a body density of more than 2.75 must be used. Phosphate composite bricks are added with silicon carbide, and the wear resistance coefficient and corrosion resistance are higher than ordinary phosphate bricks.
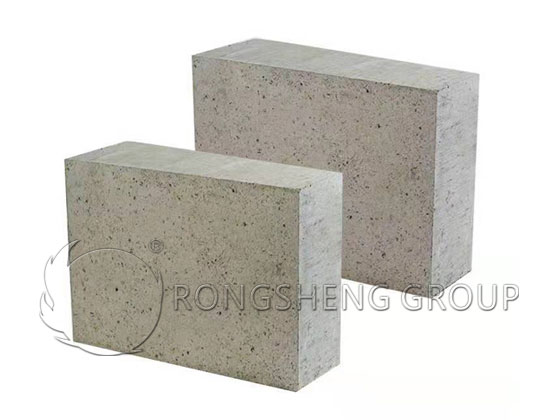
Phosphate Wear-Resistant Bricks for Firing Zone of Lime Rotary Kiln
The temperature of the lime rotary kiln is different in each zone, so it is appropriate to use different grades of phosphate bricks for the lining. Some limestone rotary kilns with small kiln diameters use high alumina bricks as transition zones. Because lime has an alkaline atmosphere, it is a good choice to use the phosphate brick series for the lining. Because phosphate bricks are also suitable for an alkaline atmosphere, which is consistent with a lime atmosphere.
If the lime kiln has a large diameter, some magnesia-aluminum spinel bricks are used as the lining. The price of magnesia series refractory bricks will be relatively higher. At present, many phosphate composite bricks are used in the market. Phosphate composite bricks have a variety of composites, some are composited with silicon carbide, some are composited with lightweight materials, and there are triple composite bricks with lightweight materials and silicon carbide. However, they are all fired with phosphoric acid.
Phosphate composite bricks compounded with lightweight materials have light kiln weight and good thermal insulation performance, which can save fuel. However, this composite also has disadvantages, that is, it is easy to break light and heavy. If it is integrated with silicon carbide composite bricks, the kiln weight is high, and the thermal insulation performance is not as good as that of lightweight composite bricks, but the composite bricks are not easy to break. That is to say, in the process of use, each has its own advantages, but it depends on the usage habits of the user manufacturer.
In general, phosphate wear-resistant bricks, if used in the firing zone, more phosphate composite bricks are used. Because this brick is wear-resistant and corrosion-resistant. However, if ordinary phosphate wear-resistant bricks are used in the firing zone, firstly, the kiln skin cannot be hung, and secondly, the matrix itself cannot meet the high-temperature requirements. Therefore, it is not acceptable to use ordinary phosphate for lime rotary kiln firing.
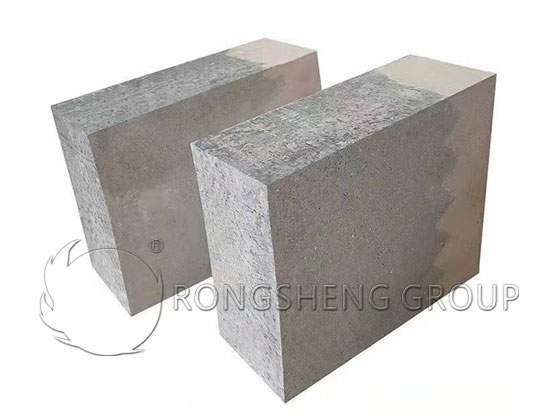
Is there a difference between phosphate bricks and phosphate composite bricks?
There is a difference between phosphate bricks and phosphate composite bricks. Although they are all combined with phosphoric acid, the internal raw material composition has changed.
Ordinary phosphate bricks generally have a body density of about 2.6. It is made by crushing bauxite with low iron or slightly higher iron content into granules and powder, using a phosphoric acid binder, and sintering at a temperature of about 550 °C. Phosphate composite bricks are made by adding a certain proportion of silicon carbide or kyanite and corundum powder to the inner matrix on the basis of ordinary phosphate and sintering at the same temperature. But the bulk density and use effect are different.
Phosphate composite bricks are available in two-component and three-component composites. Some production units are still studying the compounding of four components. However, too many components will increase the difficulty of production and the height of refractory bricks will affect the production of the furnace lining. This is also the reason why no research on this product has been formally put into use.
Phosphate composite bricks are also compounded with lightweight materials, so that the kiln lining has good thermal insulation performance during use, and the temperature of the kiln skin will decrease accordingly. In the case of good thermal insulation performance, it also saves fuel and reduces production costs. Phosphate bricks and refractory bricks made of lightweight materials are mostly used in the lining of rotary kilns. And the effect is obvious. It is favored by many manufacturers.
Phosphate bricks and phosphate composite bricks are also customized according to the needs of manufacturers. In some cases where the operating temperature and erosion of the lining are not serious, ordinary phosphate bricks are generally used. If the erosion of the lining of the kiln is serious, or the temperature of the used part is high, phosphate composite bricks will be used. Because the prices of the two kinds of bricks vary greatly, manufacturers use them to select the nature of the products they use according to different needs.
Phosphate bricks are alkaline materials and are most suitable for use in alkaline atmospheres. Most of them are used in the rotary kiln and vertical kiln of lime kiln, as well as the zinc smelting rotary kiln, and also in the transition zone of small cement kiln.
Phosphate bricks or phosphate composite bricks are suitable for use in furnace linings in alkaline atmospheres. The difference between these two bricks is that they have different wear resistance and corrosion resistance. Therefore, the two bricks have the same firing temperature and the same binder, but their properties are different. Usage is also different.
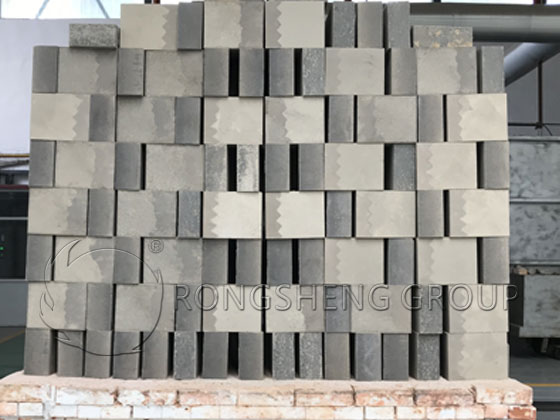
Rongsheng refractory brick manufacturers
Rongsheng Refractory Brick Manufacturer is a powerful manufacturer and seller of refractory bricks. We have rich experience in the R&D and design of phosphate bricks for lime kilns and rotary kilns. There are also many successful cases in the design and improvement of refractory linings for waste incineration furnaces and non-ferrous smelting furnaces. Save production costs for customers. The standard brick size of Rongsheng phosphate composite brick is 230*114*65 mm. We can also customize and process special-shaped phosphate composite bricks according to your needs. Contact us for a free solution and quote.