Mullite brick with thermal shock resistance and low creep, acid, and alkali resistance is better than magnesia products. With the development of domestic and foreign industrial furnaces in the direction of high quality, high efficiency, energy saving, and long service life, the technical requirements and product quality of refractory materials will be improved more. Mainly refractory materials with high load softness, low creep, and high thermal shock resistance are preferred. At present, the refractory brick lining products we commonly use are mostly made of high-alumina bauxite, mullite, andalusite, and other raw materials, and are made through batching, mixing, machine pressing, and firing. The disadvantage is that the existing heat-shock-resistant bricks are added with a large number of binders and additives, which increases the manufacturing cost and complicates the manufacturing process. And its thermal shock stability has a limited number of times of improvement. During use, peeling and cracking often occur due to rapid cooling and rapid heating. So is the Thermal Shock Resistant Low Creep Mullite Brick was developed.
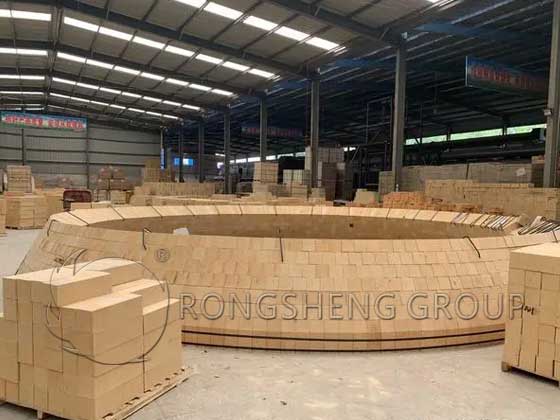
Thermal Shock Resistant Low Creep Mullite Brick
The Thermal Shock Resistant Low Creep Mullite Bricks are produced by reducing the types of components and changing the ratio. It also increases the number of main thermal shock resistance, reduces the creep rate, and increases the softening temperature under load. The Thermal Shock Resistant Low Creep Mullite Brick reduces the problem that industrial kilns use thermal shock-resistant low-creep mullite bricks, which are prone to peeling and damage. The production process is simplified and the manufacturing cost is reduced. Mullite is the main material, plus sillimanite powder, cordierite powder, alumina powder, and Guangxi white clay (40% aluminum content). The formula after adjusting the ratio is simpler than the formula components in the prior art. However, the physical properties of the high thermal shock-resistant mullite bricks prepared by this formula are significantly improved. Mainly, the number of thermal shock resistance reaches more than 120 times, the creep rate (1300℃×50h) is 0.8%, and the softening temperature under load is 1450℃. Thus prolonging the service life of the hot blast stove, and at the same time improving the safety and reliability of the bricks during use.
Low Creep Mullite Brick
Using synthetic mullite clinker and super high-alumina bauxite clinker as raw materials, and adding some high-purity quartz and additives, low-creep mullite bricks can be manufactured. Forming is carried out on a 300t friction brick press. The bulk density of the green body should be controlled above 2.70g/cm3. The green body is dried at 50~110°C for 16 hours. After drying, the residual moisture of the green body should be less than 0.5%. The highest firing temperature of the product is 1600°C, and the heat preservation time is 16h. The physical index of the product is as follows: the apparent porosity is 19~21%. Bulk density 2.55~2.60g/cm3. Compressive strength 69~116MPa. 1450℃, 50h pressure creep rate 0.12%.
Low Creep Sintered Mullite Brick
Sintered mullite bricks can be made by using andalusite as aggregate, sillimanite as intermediate particles, and common finely ground powder of sillimanite powder, bauxite powder, industrial alumina powder, and clay powder as base material. The firing temperature is 1490°C and the temperature is kept for 19 hours. The porosity of the product can reach 17.15%, the bulk density is 2.53g/cm3, the compressive strength at room temperature is 136.5MPa, and the softening temperature under load is 1627°C. 1450℃, 50h creep rate can reach 0.87%. If the firing temperature is 1450°C and the holding time is extended to 26 hours, the purpose of sintering can also be achieved. However, the physical performance index is lower than that of the product fired at 1490°C. For example, at 1450°C, the 50h creep rate is 0.98%.
What is the production process of mullite bricks?
- Raw materials: mullite and fused white corundum, with Suzhou soil as the binder.
- Aggregate preparation: artificially synthesized mullite is crushed to a suitable size for aggregate.
- Binder preparation: Fused white corundum is ground into superfine powder as a binder.
- Forming: Forming with a friction press.
- Drying: The body is dried in a tunnel dryer. The inlet temperature is 40~50°C, the maximum drying temperature is 130°C, the drying time is 48h, and the moisture content of the green body is not more than 1.5%.
- Sintering: The product is fired in a tunnel kiln at a firing temperature of 1650°C and a holding time of 10 hours.
RS Cheap Fire Bricks Factory
RS Cheap Fire Bricks Factory can provide high-quality refractory brick products and various insulation brick products, including low-creep sintered mullite bricks, mullite insulation bricks, lightweight insulation bricks, etc. Our technical team can customize solutions for refractory lining materials according to the working conditions of high-temperature industrial furnaces. If you need to buy refractory brick lining materials for high-temperature industrial furnaces, please contact us for free samples, solutions, and quotations.