The carbon bake furnace is a high-pressure molded carbon material product. Under the condition of isolating air, indirect heating is performed according to the prescribed roasting temperature to improve the mechanical strength, electrical conductivity, and high-temperature resistance of the carbon product. Due to the different high temperatures of each part, the selected refractory materials are also different. For example, the brick piers and pit bricks at the bottom of a closed roasting furnace bear the weight of the upper masonry and roasted products, and the fire well withstands high temperatures above 1400°C. Therefore, bonded bricks with high mechanical strength and good thermal stability are often used to build walls. The closed roasting furnace cover, which needs to be moved during the production process, is often made of lightweight refractory bricks and is mainly used in the roasting process. Including inverted smoke kiln roasters, tunnel kiln roasters, electric roasters, and ring roasters.
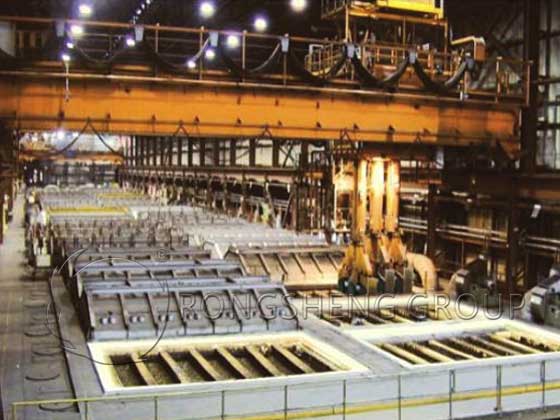
The selection of carbon bake furnace refractory materials mainly considers various factors
The first is temperature. The masonry of the upper electrode box heating wall, fire well box, and burner of the closed roasting furnace are affected by the high temperature at around 1400°C, and the temperature still changes during each roasting cycle. The second is to bear the weight of masonry and products. It is necessary to use refractory materials with high mechanical strength, high load softening temperature, and good thermal shock resistance. The use of dense clay bricks can meet the needs of the furnace charge. If the furnace cover is made of insulating refractory castables. The retort furnace then consists of forged retorts of the same size, in sets of 4. The working layer of the tank furnace body and fire escape is made of silica bricks. The working layer outside the tank working layer, tunnel masonry, heat storage body, and flue are all made of clay bricks. The rotary kiln lining can be made of high alumina bricks or phosphate bricks. Install sealing covers on kilns and kilns to avoid inhaling cold air and reduce oxidation losses. Blast furnace maintenance clay bricks are used in the lining of the sealing cover. The non-working layer uses lightweight refractory castables, and the working layer uses high-aluminum refractory castables.
Ring roasters have 18-36 roasting chambers divided into two rows. The smoke from the two roasting chambers before and after can flow in series or be blocked from each other. Realize ring segmented heating. In each baking room, the four walls of most material boxes of the same size are generally made of special-shaped hollow clay bricks or high-aluminum bricks, which are aligned up and down to form a vertical heating wall.
The non-working layer of the roaster is made of clay insulation bricks, and the working layer is made of dense clay bricks. To improve the performance of the kiln, the semi-finished roasting furnace refractory materials of the fire well annular furnace are divided into annular furnaces, downwind kilns, and tunnel kilns. For overall energy saving, lightweight refractory castables can be used for the non-working layer, and clay castables or low-cement refractory castables can be used for the working layer.
The graphite furnace is a resistance furnace with a simple structure. The furnace type is Acheson type graphite furnace, which consists of a furnace head, a furnace body, and a power supply system.
The burners, furnace bottom, rotary kiln, and furnace outer walls on both sides of the furnace body are made of dense clay bricks. The inner wall of the furnace is made of carbon blocks, and the surface is made of graphite blocks. After the electrode is installed, use graphite powder to add density to avoid electrode oxidation, sealing, and insulation. The bottom of the furnace is made of clay bricks, the walls on both sides are made of clay bricks, and the refractory castable prefabricated blocks are movable walls.
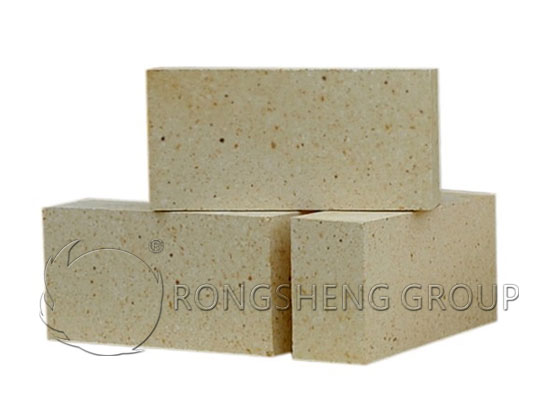
What are the refractory bricks for an anode carbon bake furnace?
Anode carbon bake furnace consists of a furnace bottom, furnace wall, horizontal wall, fire channel wall, and furnace top. The refractory bricks used include prefabricated bricks, high alumina insulation bricks, mullite insulation bricks, low porosity clay bricks, low creep clay bricks, andalusite bricks, and prefabricated large bricks.
At present, anode carbon production uses covered and open roasting furnaces. According to the form of furnace loading, it is divided into horizontal filling and open vertical filling. The anode carbon bake furnace allows high-pressure molded carbon materials to be heated indirectly while isolating air to improve the mechanical strength, electrical conductivity, and high-temperature resistance of the product.
It can be said that the entire kiln of the anode carbon bake furnace is made of refractory materials, so the amount of refractory materials used is very large between 10,000 and 20,000 tons. The performance of the refractory material determines the service life and energy consumption of the kiln.
High alumina insulation bricks are used for the 6th floor of the bottom of the anodized carbon bake furnace and the surrounding walls of the furnace. Lightweight refractory bricks are mainly composed of mullite and glass phase or corundum. Bulk density 0.4~1.35g/cm3. The porosity is 66% to 73%, and the compressive strength is 1 to 8MPa. Good thermal shock resistance.
Mullite insulation bricks are used in two layers of the furnace bottom. Mullite series lightweight insulation bricks have a bulk density of 0.5-1.25g/cm3 and a service temperature of 1300 degrees to 1550 degrees. The formula of each level is uniquely designed to meet the user’s requirements for use in different environments.
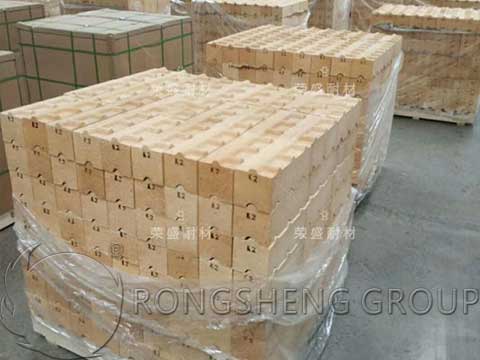
Low porosity clay bricks, 2 layers are used for the furnace bottom. It contains 30% to 46% alumina, has a refractory degree of 1580 to 1770°C, and is a weakly acidic refractory material. It has good thermal shock resistance, and corrosion resistance to acidic slag, and is widely used. Among clay bricks, those made from refractory clay as the main raw material are called clay refractory bricks. They are made from burnt gem clinker and have an apparent porosity of less than 17%.
Low-creep clay bricks for cross walls and fire channel walls of anode carbon roasters. It uses burnt gemstone, andalusite, and fused mullite as the main raw materials, and adds a small amount of additives. Using three-stage ingredients, co-grinding fine powder, and other processes, the porosity is 13-15%, the creep rate is 05-08%, and the 0.2Mpa load softening temperature is 1472°C. The clay brick has good high-temperature volume stability, creep properties, and wear resistance. With the expansion of roasting furnace types, higher requirements have been placed on the performance of refractory materials. Currently, some manufacturers are beginning to use low-creep mullite bricks for their firewalls.
Andalusite bricks are used for fire-drawn wall tiles. It is mainly characterized by a combination of special corundum, mullite, andalusite, and sillimanite. According to the high alumina brick production process, andalusite bricks with good creep resistance and thermal shock resistance are produced.
Rongsheng refractory brick manufacturer can provide high-quality anodized carbon bake furnace refractory bricks. Product quality is reliable, shipping is fast, and customer service is perfect. If you need to purchase a refractory furnace lining, please contact us.