Magnesia refractory bricks for steelmaking are mainly used in converters or ladle electric furnaces. Converters include alkaline converters and acidic converters, and there are more common alkaline converters. So, why use magnesia refractory bricks as furnace lining? Rongsheng Cheap Refractory Brick Manufacturer, based on years of production and sales experience, has discovered that the relationship between steelmaking and refractory materials is closely related to the damage mechanism of refractory lining materials.
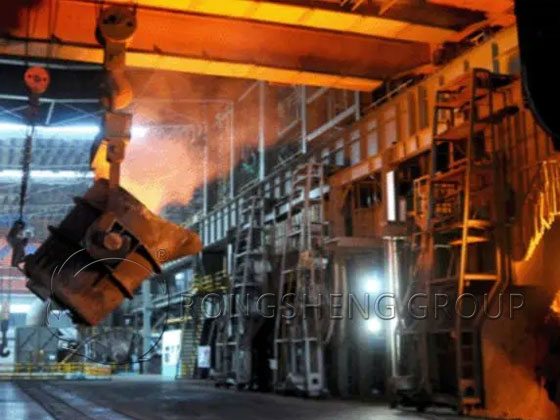
Refractory Lining Materials for Steelmaking
The damage mechanism of refractory lining materials is closely related to some very complex factors such as the chemical composition, mineral structure, and steelmaking process of refractory materials. Therefore, it is almost impossible to fully explain it in theory. However, people have done a lot of research on the high-temperature physical and chemical reactions between steelmaking melts and refractory materials, but the conclusions that can be drawn now are still only macroscopic or empirical. In summary, the causes of lining damage can be roughly divided into four categories:
- ① Mechanical impact and wear.
- ② High-temperature dissolution of refractory materials.
- ③ High-temperature solution penetration.
- ④ Gas phase volatilization at high temperatures.
Damage Mechanism of Magnesia Refractory Bricks in Converter
The main components of converter slag are CaO, SiO2, FeO, etc. When the alkalinity of the slag is low, the furnace lining refractory material mainly composed of CaO and MgO will be severely corroded, and the service life of the furnace lining will be reduced. On the contrary, when the alkalinity of the slag is high, the corrosion of the furnace lining is slight, and the service life of the furnace lining is relatively improved. When the slag contains fluoride ions, metallic manganese ions, etc., or the temperature of the molten pool rises above 1700°C, the viscosity of the solution will drop sharply. The damage rate of the furnace lining is accelerated and the service life is greatly reduced. Therefore, if the temperature of the molten steel in the converter is too high, the service life of the furnace lining will be reduced accordingly.
The components that the solution penetrates into the refractory material include: CaO, SiO2, and FeO in the slag; Fe, Si, AL, Mn, and C in the molten steel; and even metal vapor, CO gas, etc. These penetrating components settle in the capillary channels of the refractory material, causing discontinuity between the physical and chemical properties of the refractory working surface and the original refractory matrix. Under the rapid temperature changes of converter operation, cracks, peeling and loose structures appear. Strictly speaking, this damage process is much more serious than the dissolution damage process.
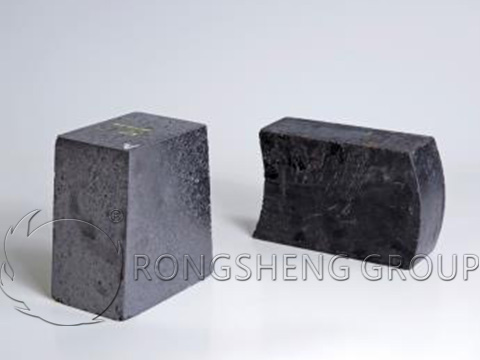
Therefore, to reduce the penetration of solution into refractory materials, measures include:
- (1) The porosity and pore diameter of the furnace lining refractory material should be reduced.
- (2) Add materials that are difficult to wet with the solution, such as graphite, carbon, etc., into the refractory materials.
- (3) Strictly control the viscosity of the solution, that is, control the smelting intensity, control the tapping temperature, etc.
Slag erosion process of magnesia carbon bricks
From the slag erosion resistance test of furnace lining materials, it can be concluded that the slag erosion process of magnesia carbon bricks is: graphite oxidation → periclase phase is eroded by SiO2 and Fe2O3 in the slag → low-melting products generated by the reaction are melted away.
In the refractory materials of carbon-containing furnace linings, the slag erosion resistance will increase with the increase of carbon content, but the higher the carbon content, the better. Because the higher the carbon content, the looser the structure of the furnace lining refractory material after oxidation and carbon loss, and the worse the use effect.
Erosion Resistance of Converter Lining Refractory Materials
Through a large number of slag resistance test studies and actual converter operations, some understandings of the corrosion resistance of furnace lining refractory materials can be derived:
- (1) The composition of molten iron has a significant impact on the service life of furnace lining refractory materials. Especially the content of silicon, phosphorus and sulfur.
- (2) Too high the end temperature of the converter will lead to a reduction in the life of the furnace lining. Especially when the end temperature is above 1700°C, the erosion rate of the furnace lining refractory material will increase significantly for every 10°C increase.
- (3) Increasing the alkalinity of slag will help reduce the erosion of alkaline refractory materials by slag.
- (4) Increasing the MgO content in the slag can reduce the erosion of the slag on the furnace lining refractory materials.
- (5) Increasing the FeO content in the slag will lead to increased corrosion of the furnace lining refractory materials.
- (6) In the early stage of converter blowing, the alkalinity of the slag is relatively low, which seriously corrodes the furnace lining. Dolomite should be used to make slag so that the MgO content in the slag is close to saturation.
- (7) The slag corrosion resistance of MgO in dolomite and magnesium dolomite refractory materials is due to CaO. However, the presence of CaO can improve the high-temperature thermoplasticity and slag penetration resistance of refractory materials.
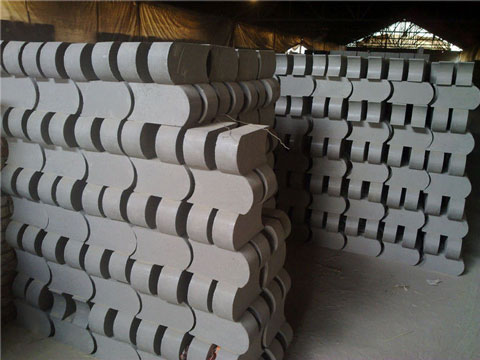
Rongsheng Magnesium Carbon Brick Refractory Brick
Magnesium refractory bricks are mainly made of magnesia, seawater magnesia, and dolomite as raw materials. Refractory bricks with periclase as the main crystal phase and magnesium oxide content of more than 80% belong to alkaline refractory bricks. Magnesia refractory bricks are mainly divided into magnesia bricks, magnesia silica bricks, magnesia aluminum bricks, magnesia calcium bricks, magnesia carbon bricks, and other varieties. The load softening point and thermal shock resistance of high-purity magnesia bricks are much better than those of ordinary magnesia bricks. It has high refractoriness and good resistance to alkaline slag and iron slag. It is an important advanced refractory material.
Rongsheng magnesia carbon bricks are made of high-purity magnesia, fused magnesia, and graphite powder as raw materials, medium-temperature asphalt as a binder, and high-pressure molding. The product has the characteristics of good thermal stability, high load softening temperature high-temperature flexural strength, and strong resistance to alkaline slag erosion.
Magnesia carbon bricks are one of the main refractory materials currently used in steelmaking furnaces. It is mainly used for the lining of the slag line of converters and electric furnaces and the ladle for refining outside the furnace. Because its performance is better than that of magnesia bricks and tar dolomite bricks, it can greatly increase the life of the furnace when used in steelmaking furnaces.
Buy high-quality refractory bricks for steelmaking and refractory lining materials for steelmaking furnaces. Contact Rongsheng refractory brick manufacturer to buy high-quality magnesia refractory bricks. Product quality is reliable and customer service is guaranteed.