Vitrification is currently recognized as the only industrialized method that can efficiently handle high-level radioactive waste. The glass matrix can clamp various radioactive nuclear elements, and the vitrification method can ensure long-term safe storage after converting radioactive waste into a glass state. Currently, there is industrial equipment for vitrification of highly radioactive waste in Russia, the United States, France, the United Kingdom, Germany, and Japan. There are two main types of these processing equipment. The first is a direct-heating electric furnace with a ceramic melter. This method has mature technology and high production efficiency. The second method is an induction stove.
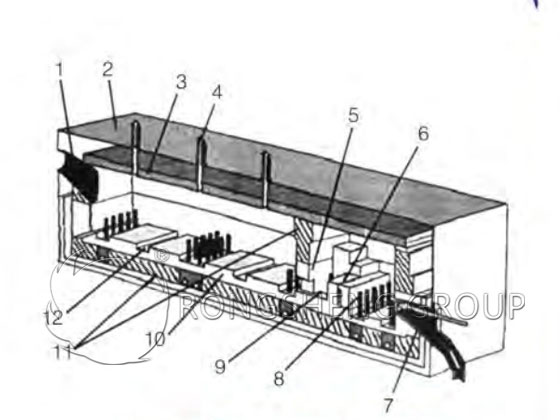
Refractory materials for radioactive waste glass solidification electric melting furnaces
Germany’s Pamela facility is the first in the world to have a ceramic melter for vitrification of highly radioactive waste. Russia’s domestic industrial-scale vitrification process for highly radioactive waste was successfully developed in 1987. A direct heating glass electric melting furnace, 9I1-500 electric melting furnace, was built in the PT-1 factory. An aluminum phosphate glass electrofusion method test was carried out, and the temperature of the electric furnace reached 1150 ℃. Since 1987, the plant has operated a total of 4 such electric furnaces. The service life of these electric furnaces ranges from 1 to 6 years.
A series of structural components on the lining masonry of the 31-500 electric furnace in industrial operation suffered the most severe corrosion. Including the melt pool furnace wall, retaining wall, overflow area furnace sill near the glass feed line, etc., which are composed of BK-33 cast zirconium corundum refractory material. For the electric melting furnace to operate safely and for a long time, it should be built with refractory materials with high corrosion resistance. The corrosion resistance of refractory materials in electric furnaces depends first on the melting temperature and composition of the molten glass frit. In domestic and foreign enterprises, borosilicate glass and aluminum phosphate glass are mainly used in electric furnace melting baths to solidify high-level radioactive waste.
The composition of glass used in different countries varies, mainly due to differences in the composition of radioactive waste. The melting temperature of aluminophosphate glass is 850~1000℃, which is lower than the melting temperature of boron silicate glass which is 1150~1250℃. However, both are highly corrosive to refractory materials.
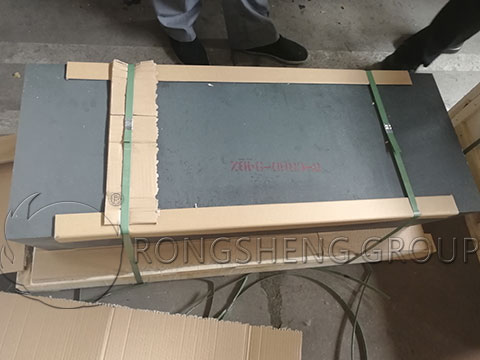
To ensure the reliable long-term operation of the high-radioactive waste glass solidification electric melting furnace, a group of more promising refractory materials compared with BK-33 bricks were analyzed. These include XIA-85 and XMT, fused-cast high-chromium bricks that have been put into industrial production, and XAL-26 chromium-aluminum-zirconium bricks that are in trial production. The sintered chromium-containing bricks produced abroad, SUPRAL RK30S and SUPRAL RK50S (RHI Company, Italy), were also compared.
Application trends of glass furnace refractory materials
When it comes to the development and application of refractories in the glass industry, there are three main drivers of change and development in refractories. The first is the need of glass manufacturers to at least maintain and often improve the quality of their glass. The second is the economic requirement of glass kilns to enable longer kiln operating cycles. The third is the impact and influence brought by the pure oxygen combustion system. These three requirements usually determine the selection of improved refractory materials when repairing kilns. These drivers are also driving glassmakers to use improved refractory products for furnace maintenance and new technology for extensive overhauls during the operating cycle.
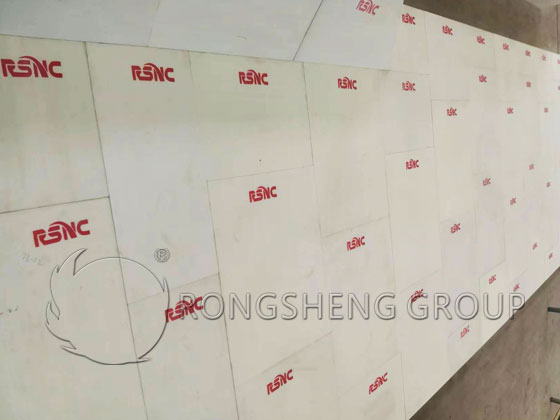
Melt-cast alumina bricks have established their application in the roof of the melting tank, mainly in pure oxygen-fired tank furnaces for melting high-quality glass. Before the advent of pure oxygen combustion technology, only β-alumina bricks were used in the superstructure of the melting pool, and no melt-cast alumina bricks were used on the top of the melting pool. Today, melt-cast products of both β-alumina and α-β alumina are used in the production of color televisions (screens and cones). and float glass and borosilicate glass on part or all of the roof of a pure oxygen-burning pool furnace. Fused-cast AZS bricks can generally be used up to 1600°C or 1650°C, depending on the glass product. Furnace roofs made of fused alumina bricks can successfully operate at 1,700°C. This creates better conditions and greater flexibility for glass manufacturers when producing refractory glass.
For many years, melt-cast AZS furnace roofs have been successfully subjected to cooling and reheating to enable them to be used for multiple operating cycles. A little experience has now been gained with the successful implementation of fused alumina furnace top cooling and reheating, which shows greater economic viability when they are used for two or more operating cycles. Fused alumina furnace roofs were observed in use (hot and shut down) and the results showed that these materials have both chemical and mechanical stability. This is the earliest observational study of this type of masonry. Because at that time there was neither reference material for fused alumina nor any experience basis for its application on furnace tops.
In the past, high-chromium refractory products were mainly used in reinforced glass furnaces and to a small extent in insulated glass pool furnaces. High chromium bricks are now increasingly being used in some soda-lime glass pool furnaces. Its main use is no longer limited to full or partial flow holes, but also to end walls and, to a limited extent, to corner bricks of feed openings. The composition of high chromium bricks presents a potential coloring hazard. So much so that high chromium products are often incompatible with very “white” glass. Initially, this product was mainly used for colored glass, but now high chromium products have also been successfully used in clear container glass furnaces. The amount of high chromium products used in a glass melting furnace depends largely on the design of the flow hole, the cooling of the flow hole, the daily output of the pool furnace, and the operation of the furnace. A glass manufacturer may use high chromium bricks for the entire cover plus the end walls of the melting tank. High chromium brick masonry’s flow holes offer the potential to increase kiln life, as this material is at least twice as resistant to most glasses as fused AZS bricks. However, certain design and operating parameters differ from fused AZS bricks and need to be discussed with the supplier.
To purchase high-quality refractory materials for glass kilns, please contact us. We can provide you with high-quality glass furnace refractory material solutions and material configurations.