Zero expansion silica brick is also called fused quartz brick or thermal shock-resistant silica brick. Coke ovens have the characteristics of extremely low thermal expansion coefficient, excellent resistance to rapid cooling and rapid heating, good high-temperature structural strength, and high SiO2 content. Therefore, zero-expansion silica bricks can be widely used in rapid thermal repair projects of various coke ovens. Zero-expansion silica bricks will not crack or peel when used under high-temperature conditions. The near-zero low thermal expansion performance makes the coke oven safe and reliable for long-term use after repair.
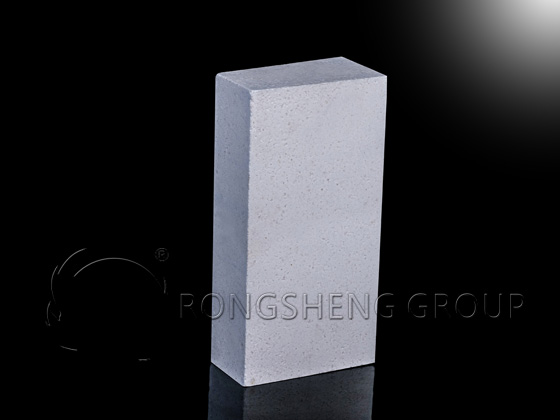
Characteristics of Zero Expansion Silica Bricks
- SiO2 content is greater than 99%, with excellent corrosion resistance and acid resistance.
- Low Fe2O3 content is less than 0.1%, no pollution to products (such as glass liquid, etc.).
- Low flux index (Al2O3+2R2O) is less than 0.3%.
- The thermal expansion rate is close to zero, so there is no need to reserve expansion joints during repairs, which increases the tightness of the masonry.
- Excellent thermal stability, the product will not explode during hot repair. Repair work can be carried out directly without stopping the furnace at high temperatures.
- After repair (hot repair), peeling and other phenomena will not occur, and it is safe and reliable for long-term use.
Application Cases of RS Zero Expansion Silica Bricks
Damage to the bottom bricks in the carbonization chamber of a coking plant customer. Adopt a plan to repair the furnace bottom bricks with zero-expansion silica bricks at temperatures above 850°C. It solves the problem of repairing the bottom bricks of the carbonization chamber and achieves a successful thermal repair.
Rongsheng Refractory Brick Production and Sales Manufacturer, as a professional refractory material manufacturer, can produce many different types of refractory bricks and refractory insulation brick products. Product types are basically classified according to materials and construction methods. Our factory produces a complete range of products. It can meet the high-temperature resistance requirements required by various power plant boilers, industrial kilns, and other thermal equipment at this stage. The product quality is worthy of your trust.
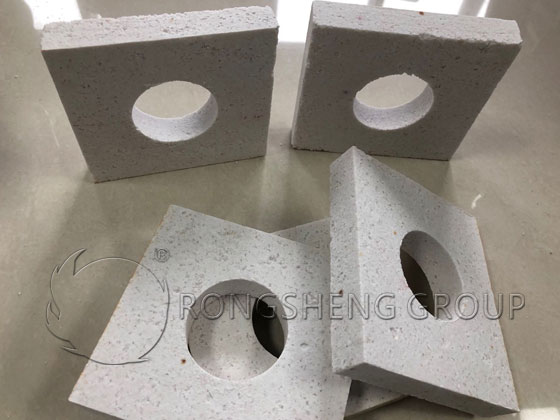
What Role Does Zero-Expansion Silica Brick Play at High Temperature?
RS zero expansion silica brick manufacturer and sales manufacturer. Zero-expansion silica bricks are refractory products and are fired at high temperatures. What role does zero-expansion silica brick play at high temperatures?
Excellent thermal shock resistance at high temperatures. Due to the periodic coal loading and coke extraction of the coke oven, the temperature of the silica bricks on both sides of the combustion chamber wall changes drastically. The normal operating temperature is unstable and will not cause serious cracking and peeling of the silica bricks. Since the temperature is above 600 degrees Celsius, coke oven silica bricks have excellent thermal shock resistance.
The volume is stable at high temperatures. In silica bricks with good crystalline transformation, the residue should not exceed 1%. The expansion during heating is concentrated at 600 degrees Celsius, and then the expansion slows down significantly.
When the coke oven is operating normally, the temperature will not drop below 600 degrees Celsius. The masonry will not undergo major changes, and the stability and tightness of the masonry can be maintained for a long time.
What are the Causes of Cracks in Zero-Expansion Silica Bricks? Factors Affecting Price
There are several types of cracks in zero-expansion silica bricks. If it is peeling or vertical cracks of bricks, it is caused by the press hammer not exhausting during the process of forming and pressing bricks. If there are transverse or network cracks, the temperature rises too quickly during the drying process. In another case, if the firing temperature is not properly controlled, horizontal cracks will also appear on the surface of the silica brick.
It should be said that cracks are an important part of the yield of zero-expansion silica bricks. If not properly controlled, costs can increase significantly. This is also one of the reasons why the price of zero-expansion silica bricks is higher.
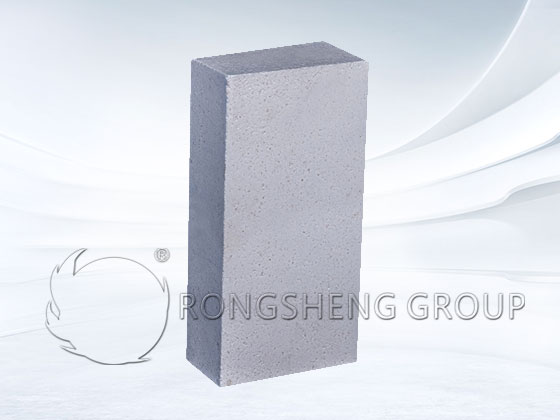
Zero-expansion silica brick is an acidic product, and compared with neutral high-alumina bricks, the yield is low. Another important reason is the high expansion coefficient of silica bricks. If the mold sizing is incorrect, the finished size of the silica brick will seriously exceed the standard.
During the firing process of zero-expansion silica bricks, the crystal changes, the volume expansion coefficient is large, and it is easy to crack. But if there are microcracks, the structural elasticity can be improved.
The cracks of zero-expansion silica bricks are divided into surface cracks and internal cracks. Among them, namely mechanical cracks and temperature-firing cracks. If the surface cracks are crisscrossed and of varying lengths. Because drying is incomplete, the moisture in the product is not exhausted and sintering begins at high temperatures. The kiln for firing silica bricks must be at least 150 meters above ground. Otherwise, the thermal insulation performance is not good, and the cracking rate of the fired silica bricks will be very high.
Lamination occurs during the product molding process. It occurs when the mold ages or the pressed bricks do not vent. Cracked zero-expansion silica bricks cannot be used, their internal quality is not good, and they cannot be used at high temperatures. This type of crack is a mechanical crack.
If it is a network crack, it is caused by large temperature fluctuations and uneven products. Another possibility is that the aggregate and powder are unevenly mixed during the mixing and grinding process, and network cracks may also appear.
During firing, transverse cracks in the silica bricks appear on the outside of the kiln car brick stack, especially on the top products. Due to the high temperature, the fire path for kiln car loading is unreasonable, and the flame is directly sprayed on the brick surface, causing uneven heating.
The cracks in zero-expansion silica bricks are also related to the process. Too many fine particles will also cause cracks, and poor-quality binders added during the proportioning process will also cause cracks. If there is no drainage during drying the kiln car is unscientific, or the firing is heated too fast, cracks will occur.
In order to well control the cracks of zero-expansion silica bricks, it is necessary to carefully control the production process from the raw material ratio to the molding and firing process, and pay attention to every link. If the technical level of the production personnel reaches a certain level, then the firing temperature of the bricks can be controlled. Then the occurrence of cracks will definitely be solved.
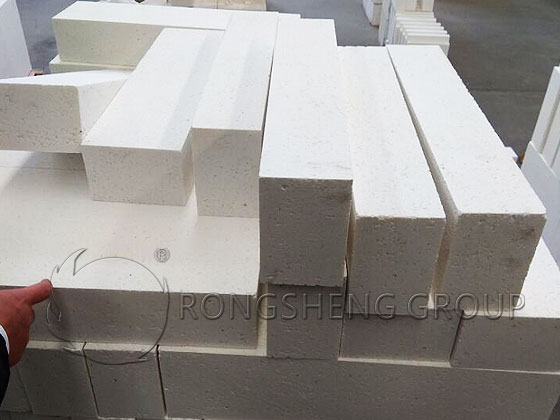
Zero-Expansion Silica Brick Manufacturer
Zero-expansion silica brick binders include molasses, leuco acid pulp waste liquid, etc. The mass fraction of silica in silica bricks is not less than 93%. It is a typical acidic refractory brick with good resistance to acid slag, Al2O3, FeO, Fe2O3, and other oxides. However, it has poor resistance to alkali residue and is easily destroyed by oxides such as CaO, K2O, and Na2O. Zero expansion silica brick is also called fused silica brick or thermal shock-resistant silica brick.
Product application of zero-expansion silica bricks
Coke ovens have low thermal expansion coefficients, and their refractory linings are required to have good resistance to rapid cooling and rapid heating. It has the characteristics of good structural strength under high temperatures and high silica content. This product can be widely used in rapid thermal repair projects of various coke ovens. The product does not crack or peel during use, and its low thermal expansion performance is close to zero, making the coke oven reliable for long-term use after maintenance.
Product raw materials and production technology
The raw material for making silica bricks is silica. The higher the silica content of the silica raw material, the higher the fire resistance. Harmful impurities include Al2O3, K2O, Na2O, etc., which seriously reduce the fire resistance of refractory products. Silica bricks are made of silica with a silica content of not less than 96%, mineralizers (such as iron oxide scale, lime milk), and binders (such as molasses, sulfite slurry waste liquid). It is made by mixing, shaping, drying, and firing.
What does zero expansion silica brick mean? What is the difference between it and silica brick?
Silica bricks are corrosion-resistant to acid slag. Higher temperature strength. The starting temperature of load softening is 1620~1670℃. It will not deform after long-term high-temperature use. The expansion of zero-expansion silica bricks is almost zero, and ordinary silica bricks will also expand, so there is a difference in price between the two.
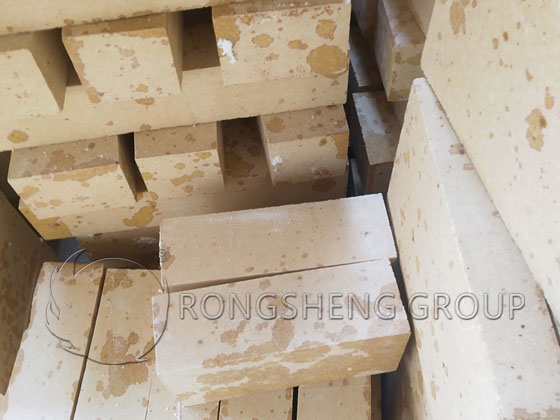
(1) The main mineral phase of zero-expansion silica bricks is amorphous silica, accounting for more than 90%.
Zero-expansion silica bricks are made of high-quality mineral raw materials through electric arc furnace smelting, cooling, crushing, screening, and pickling. The particles are mixed with a small amount of mineralizing agent and sintering agent to form semi-dry mud, which is pressed, dried, and fired. The main mineral component is amorphous amorphous fused quartz. The thermal expansion coefficient of the product is almost zero, so it is called zero expansion silica brick.
(2) Atomic structure of amorphous fused silica.
Also silica, the structure of amorphous silica is different from that of crystalline silica. Each silicon atom and oxygen atom of crystalline silica forms a silicon-oxygen tetrahedron, silica. All tetrahedrons are connected through corner vertices to form a three-dimensional network structure. Amorphous silica structure, disordered amorphous silica has vacancies in its silicon-oxygen bonds. Its atomic structure is disordered, and the bond angles between silicon-oxygen tetrahedrons are irregularly distorted, forming three-dimensional cross-links.
The thermodynamic properties of materials are determined by their atomic crystal structure. Silica has a variety of isomorphic structures. The crystal phase structures formed under different conditions are different, so the thermodynamic properties are different.
The thermal stability of silica crystals is poor because the thermal bond angles of the silica crystals change. It begins to be isomorphic at 180°C, accompanied by huge volume expansion, and cracks appear after water cooling at 1100°C. Amorphous silica has the characteristics of a small thermal expansion coefficient, good thermal stability, high-temperature viscosity, and small thermal conductivity. However, amorphous silica is unstable at high temperatures and does not change volume when heated up to 1100°C. However, as the temperature increases, amorphous silica begins to crystallize. Due to the slow crystallization process, it can well meet the construction requirements during hot repair operations.
In the production process of zero-expansion silica bricks, effective measures are taken to control the crystallization speed and crystallization ratio of amorphous molten silicon at high temperatures. Make it better meet hot patching requirements.
(3) Thermal stability test of zero-expansion silica bricks.
After the expanded silica brick was heated to a high temperature of 1100°C, it was immediately placed in normal-temperature water. After 30 water cooling cycle tests, there was no change. Zero-expansion silica bricks are directly released from room temperature to 1500°C for 12 hours. Actual test results show that zero-expansion silica bricks have better thermal stability.