Silica bricks undergo homopolycrystalline transformation and are accompanied by volume changes during heating. High load deformation temperature is an excellent characteristic of silica bricks, which is close to the melting points of tridymite and cristobalite (1670°C, 1713°C), and fluctuates between 1640 and 1680°C. The volume of silica bricks is stable from above 300°C to close to the melting point. During use, there is approximately 1.5~2.2% total volume expansion when heated to 1450°C. This residual expansion will cause the masonry joints to seal tightly, ensuring good air tightness and structural strength of the masonry body. The biggest disadvantage of silica bricks is low thermal shock stability (heat exchange in water is about 1 to 4 times). Secondly, the refractoriness is not high (generally 1690~1730℃), which greatly limits its application range.
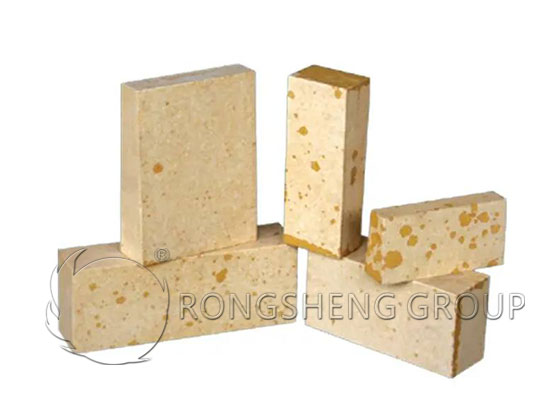
Why do Silica Bricks Expand?
First, the expansion of silica bricks comes from homopolycrystalline transformation.
SiO2 has seven variants and one amorphous variant under normal pressure. And β-quartz, α-quartz, γ-quartz, β-tridymite, α-tridymite, β-cristobalite, α-cristobalite and quartz glass. The transitions between the above variants can be divided into two categories.
The first type is the transformation between quartz, tridymite and cristobalite. During the transformation, the original crystal structure must be destroyed (the Si-O bond is broken up) and a new structure must be reorganized. That is, the rearrangement of atoms is completed. Due to the large activation energy required, the transformation temperature is high and slow, accompanied by a large volume effect.
The second category is the transformation of the α, β, and γ types among the above-mentioned variants. Since they are very similar in structure and properties, the transformation is just a structural distortion and the Si-O bond is not dismantled. Therefore, the transformation occurs at a certain temperature, is a block, and is reversible. The time required to complete the transition between such variants is short-lived. At the transition temperature, the surface and surface of the crystal undergo an instantaneous transformation, and this variant can only coexist at the transition temperature.
Then, there is the firing expansion of the silica bricks.
Silica bricks undergo phase changes during the firing process and have large volume changes. In addition, the amount of solution formed by bricks at the firing temperature is small (about 10%), making it much more difficult to fire than other refractory products. The firing system of silica bricks and a series of physical and chemical changes that occur in the bricks during the firing process. Factors such as the quantity and nature of the additives, the shape and size of the green body, and the characteristics of the firing kiln are related.
- Physical and chemical changes of silica bricks during the firing process. Silica bricks undergo the following changes in temperature sequence during the firing process. Residual moisture is discharged from the bricks below 150°C. At 450°C, Ca(OH)2 begins to decompose. At 450~500℃, the dehydration of Ca(OH)2 is completed, the combination of silica particles and lime is destroyed, and the strength of the green body is greatly reduced. In the range of 550~650℃, β-quartz transforms into α-quartz. Since the transformation process is accompanied by a volume expansion of 0.82%, the quartz crystal will have microscopic cracks with varying densities. Between 600 and 700°C, the solid phase reaction between CaO and SiO2 begins, and the strength of the brick increases. Starting from 1100°C, the transformation speed of quartz increases greatly and the specific gravity of bricks also decreases significantly. At this time, the brick volume is greatly increased due to the transformation of quartz into a low specific gravity variant. Although the liquid phase is also increasing at this time, cracks will still occur in the temperature range of 1100~1200°C.
- The volume of siliceous bricks changes during the heating process, which is different at different temperature stages. According to the changing characteristics of various types of silica green bodies, they can be divided into stages below 600°C, 600~1100°C, 1100~1250°C and above 1250°C. There is significant expansion between 500 and 600°C due to the transformation of β→α quartz. At 700~800℃, there is a solid phase reaction between CaO and SiO2, which causes microscopic shrinkage. At 1000~1100℃, the shrinkage is more significant due to the formation of liquid phase. Starting from about 1200°C, the green body begins to expand violently due to the acceleration of quartz transformation.
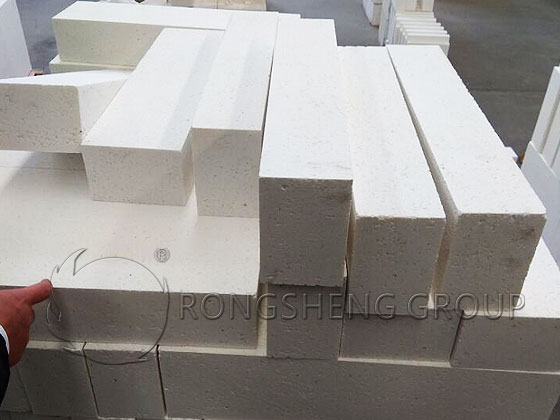
Zero Expansion Silica Brick
Zero expansion silica brick, also known as fused quartz brick or thermal shock resistant silica brick. It has the characteristics of extremely low thermal expansion coefficient, excellent resistance to rapid cooling and rapid heating, good high-temperature structural strength, and high SiO2 content. This product can be widely used in rapid thermal repair projects of various glass kilns and coke ovens. This product will not crack or peel off during use, and its low thermal expansion performance is close to zero, making the kiln safe and reliable for long-term use after repair.
Characteristics of zero expansion silica bricks
- SiO2 content is greater than 99%, with excellent corrosion resistance and acid resistance.
- Low Fe2O3 content is less than 0.1%, no pollution to products (such as glass liquid, etc.).
- Low flux index (Al2O3+2R2O) is less than 0.3%.
- The thermal expansion rate is close to zero, so there is no need to reserve expansion joints during repairs, which increases the tightness of the masonry.
- Excellent thermal stability, the product will not explode during hot repair, and can be repaired directly at high temperatures without stopping the furnace.
- After repair (hot repair), peeling and other phenomena will not occur, and it is safe and reliable for long-term use.
- There is no need to bake for a long time after masonry; no preheating is required. Main uses: In the chemical industry, it is mainly used as the roof and other parts of glass melting furnaces. Zero-expansion silica bricks are easy to make into large pieces due to their small expansion rate, high thermal stability, and high compressive strength, and their surfaces are smooth and do not deposit carbon.
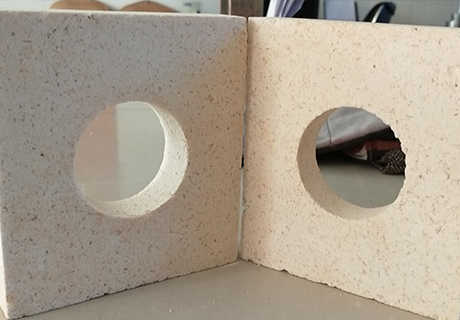
Main uses of fused quartz bricks
It is widely used in high-temperature thermal equipment such as glass melting furnaces, coke ovens, and hot blast furnaces. In particular, high-temperature thermal equipment can be repaired arbitrarily without stopping the fire.
Application of Silica Bricks and Zero-Expansion Silica Bricks in Glass Kilns. Silica bricks refer to acidic silica products with SiO2 content greater than 93%. The properties of silica bricks include chemical mineral composition, true density, bulk … Read More for Free Quote
What are the Advantages of Fused Silica Bricks for the Hot Repair of Coke Ovens? During the long-term use of coke ovens, the furnace body will inevitably gradually aging due to high temperature, mechanical force, and physical and chemical reactions. The … Read More for Free Quote
Categories, Refractory Bricks, Silica Bricks, Zero-Expansion Silica Bricks, Fused quartz brick, fused silica brick
The Differences and Characteristics Between Silica Bricks and Zero-Expansion Silica Bricks
Silica bricks refer to acidic silica products with SiO2 content greater than 93%. The properties of silica bricks include chemical mineral composition, true density, bulk density, refractoriness, load softening temperature, high-temperature volume stability, thermal shock resistance slag resistance, etc. It is closely related to many factors such as the nature of raw materials, crystal transformation status, and manufacturing process. It is mostly used in coke ovens, hot blast furnaces, glass kilns, vaults of tunnel kilns, shelf bricks of various kilns, etc. In particular, coke ovens (carbonization chamber, combustion chamber, regenerator) use a large number of silica bricks.

Characteristics of silica bricks for glass melting furnaces
- 1 High-temperature volume stability. The furnace body will not change due to temperature fluctuations. Due to the high load softening temperature and low creep rate of silica bricks. The glass-melting furnace can maintain the furnace body without deformation and the structure is stable at 1600°C.
- 2 No pollution to glass liquid. The main component of silica bricks is SiO2. If there are any pieces falling off or surface droplets during use, it will not affect the quality of the glass liquid.
- 3 Resistant to chemical attack. The silica bricks of the superstructure are corroded by gases containing R2O in the glass batch. A smooth metamorphic layer is formed on the surface, which reduces the erosion rate and plays a protective role.
- The volume density is small, which can reduce the mass of the furnace body. The true density of high-quality silica bricks is 2.32-2.36g/cm3, and that of general silica brick products is 2.38-3.42g/cm3.
Although the refractoriness of silica bricks is not very high, their softening temperature under load is high and their high-temperature structural strength is high. And it has good stability when used for a long time above 600℃. When heated to 1450°C, the total volume expansion is about 1.5% to 2.2%. This residual expansion will cause the seams to close tightly, ensuring that the masonry has good air tightness and structural strength. It also has the advantages of long service life and reduced energy consumption. Can resist the erosion of acidic slag. Therefore, it is currently mainly used for building glass furnaces and coke ovens. The partition wall of the coke oven carbonization chamber is built with silica bricks, which has good stability and air tightness under high temperatures and has a service life of 10-15 years. If used properly, it can last more than 25 years.
Silica bricks for glass kilns, characteristics of zero-expansion silica bricks
- SiO2 content is greater than 99%, with excellent corrosion resistance and acid resistance.
- Low Fe2O3 content is less than 0.1%, no pollution to products (such as glass liquid, etc.).
- Low flux index (Al2O3+2R2O) is less than 0.3%.
- The thermal expansion rate is close to zero, so there is no need to reserve expansion joints during repairs, which increases the tightness of the masonry;
- Excellent thermal stability. The product will not explode during hot repair, and can be repaired directly without stopping the furnace at high temperatures.
- After repair (hot repair), peeling and other phenomena will not occur, and it is safe and reliable for long-term use.
- Good corrosion resistance. Due to the lack of calcium, erosion cannot form.
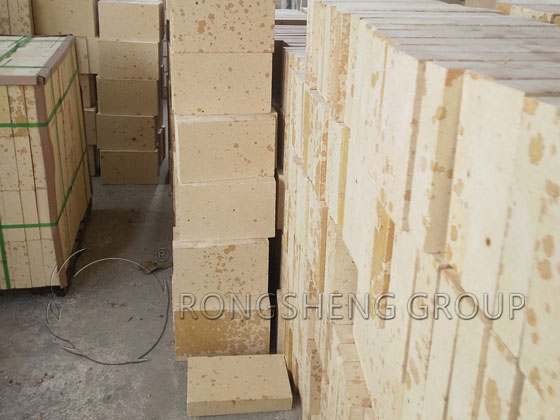
Zero expansion silica brick is also called fused quartz brick or thermal shock-resistant silica brick. Resistant to acidic slag erosion. Higher high-temperature strength. The load softening starting temperature is 1620~1670℃. It will not deform after long-term use at high temperatures. Good thermal shock stability, heat exchange in water is 1~30 times. It uses natural silica as raw material and adds an appropriate amount of mineralizing agent to promote the transformation of quartz in the green body into tridymite. In a reducing atmosphere, it is slowly fired at 1350~1430℃. In the process of firing silica bricks, why should they be fired slowly? The main thing is to convert quartz into tridymite. The more tridymite, the smaller the true specific gravity and the higher the melting point. And because phosphoquartz is a spearhead-shaped twin crystal, the spearhead-shaped twin crystals will form an intertwined network structure, giving the product a higher load-softening temperature and mechanical strength. Therefore, it is generally hoped that there will be as much tridymite in the fired silica bricks as possible. Followed by cristobalite, the less residual quartz, the better.
Buy high-quality glass kiln refractory bricks, please contact us. We can provide free refractory solutions and free prices.